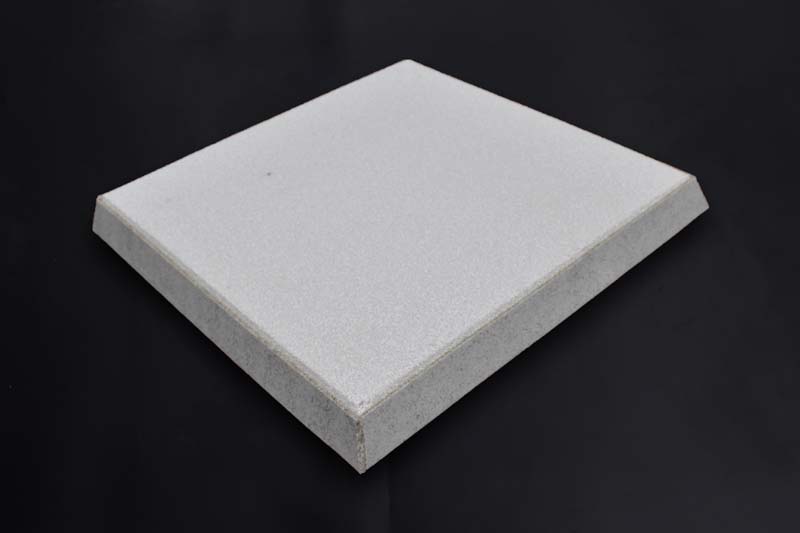
23 8月 Katagi Aluminum Ceramic Foam Filter
Katagi Aluminum Ceramic Foam Filter has developed from 15, 20, 30, 40, 50ppi to 60, 70ppi, and there are many new varieties to choose.
Inclusions and gases in the metal have a significant impact on the strength, fatigue resistance, corrosion resistance, and stress corrosion cracking performance of the material.
Effectively controlling the oxidized inclusions in the melt and improving the quality of cast rods and rolled plates have become a common goal pursued by the metallurgical, casting and material industries of all countries.
At present, alumina Cff is widely used to remove inclusions in aluminum alloy melts.
For products with higher quality requirements, developed countries generally use two-stage cast ceramic filters.
The pore size of the first-stage filter plate is relatively coarse, and the pore size of the latter-stage filter plate is relatively small, such as 30/50, 30/60ppi, or even 40/70 configuration, etc. China Southwest Aluminum also uses 30/50ppi second-stage foam ceramic filter plate to filter double zero The self-designed and manufactured secondary heat preservation filter box of aluminum sheet, PS plate base, canning materials and other melts has been installed with a filter plate to produce 7 continuous smelting, which greatly reduces the cost of filtration.
According to Katagi Aluminum, Foundry Filter uses ceramic foam filters to provide several important advantages to improve the quality of high-quality aluminum castings.
Improve mechanical properties
Reduce dye penetration
Reduce non-metal X-ray evidence
Reduce rework/scrap
Improvement of processing characteristics
The number of inclusions in molten aluminum has an important impact on the quality of aluminum and aluminum alloy ingots. In order to improve the purity of molten aluminum, Katagi Aluminum Ceramic Foam Filter is usually used in the production process of aluminum and aluminum alloy ingots to remove non-metallic inclusions in the melt. .
The current filtration methods mainly include glass cloth filtration, deep bed filtration, ceramic tube filtration and foam ceramic filter plate filtration.
Foam ceramic filter plates are widely used because of their convenient use, low cost, and high filtration efficiency. Has become the first choice for filtering molten aluminum.
As the quality requirements of ingots increase, the requirements for the purity of molten aluminum in the casting process are also getting higher and higher. Therefore, when the ceramic foam filter plate is used to filter molten aluminum, the pore size of the filter plate is getting smaller and smaller.
No Comments