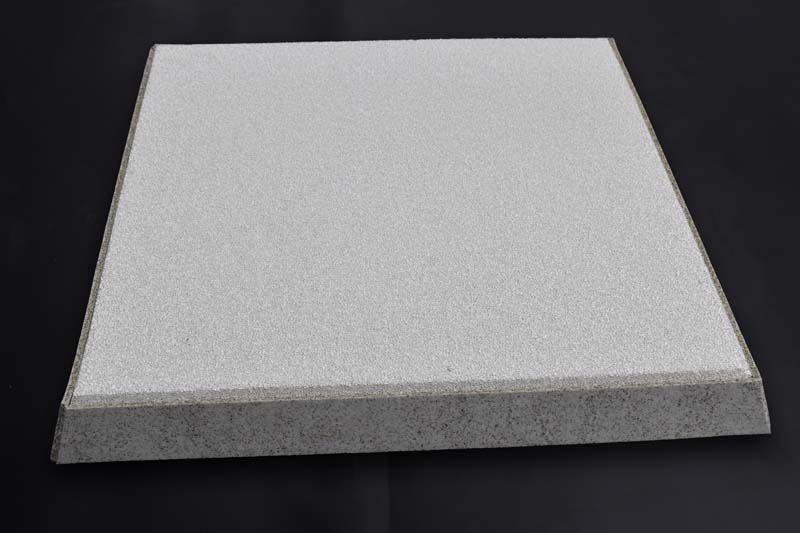
23 8月 Toyo Alumi Ceramic Foam Filter
Toyo Alumi Ceramic Foam Filter is the most commonly used product in the aluminum casting industry. It is used to remove molten aluminum during the casting process of aluminum ingots.
Ordinary aluminum castings usually use 10-40ppi ceramic filter plates.
Aviation and high-quality aluminum materials usually use 30-60ppi ceramic filter plates.
Aluminum alloy is easy to inhale air and oxidize during the casting process of aluminum rod and ingot. Therefore, there are different degrees of gas and various non-metallic inclusions in the melt, resulting in the appearance of pores, pores, inclusions and other defects in the aluminum rod ingot.
After using Toyo Alumi Ceramic Foam Filter, the mechanical properties, processing properties, fatigue resistance and corrosion resistance of aluminum rods and ingots have been greatly improved.
Aluminum melting filter media is the most commonly used ceramic foam filter in the aluminum casting industry.
Ordinary aluminum castings usually use 10-40ppi ceramic filter plates.
Aviation and high-quality aluminum materials usually use 30-60ppi ceramic filter plates.
Toyo Alumi will recommend to the local aluminum factory to recommend the contact information of the Chinese supplier of Ceramic Foam Filter. For more detailed information, please visit www.adtechamm.com. Prices can be obtained through sales@adtechamm.com.
What happens to aluminum and aluminum alloys during the melting process?
Melting aluminum casting is to convert liquid aluminum into aluminum ingots, bars or other finished or semi-finished products through the steps of batching, stirring, standing, refining, and slag reporting.
During the casting process, aluminum and aluminum alloys will experience varying degrees of loss due to oxidation, refining, and slag.
The so-called aluminum melting loss is the general term for the unrecoverable metal loss and the metal contained in the aluminum slag due to oxidation, volatilization, and interaction with the furnace wall and refining agent during the smelting process of aluminum and aluminum alloys.
Causes of aluminum melt loss
Statistics were carried out in the melting and casting workshop of Chinalco. Among them, the unrecyclable pure aluminum ash accounts for about 90% of the casting loss (oxidation, scorching and slagging), and other factors account for about 10%.
According to other factors accounting for 10%, further statistical analysis of the data, mainly the secondary furnace burning loss of bulk aluminum and inferior aluminum, and the aluminum content in aluminum ash (the main raw material of aluminum ash aluminum).
Therefore, the main inherent main causes of casting loss are oxidation burning loss, secondary burning loss such as inferior aluminum, and the aluminum content in aluminum ash.
No Comments