05 9月 Ceramic foam filtersin China’s aluminum processing industry application
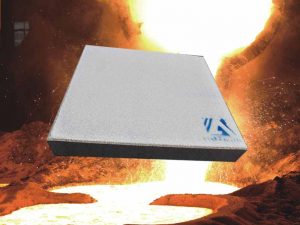
Ceramic Foam Filter
The application of ceramic foam filter plates in China’s aluminum processing industry has been popularized. There are two main modes of application in the purification of deformed aluminum alloy melts:
One is on the semi-continuous casting line of aluminum alloys. In the furnace, the melt is refined by spraying with flux powder, and the foam ceramic plate is used for filtering outside the furnace. The ceramic foam filter plate is to be replaced every time it is cast. A trough-type online degassing unit is added at the front to improve the purification effect.
The second is in the continuous casting and rolling line, according to the pressure difference before and after the filter plate to determine its replacement cycle. As for the size of the filter plate to choose, it depends on the flow rate per unit time of the molten aluminum and the total amount of the molten aluminum. The higher the cleanliness of the liquid is, the smaller the pore size is to be selected.
Filtration and purification of ceramic foam filters are the last processes of purification of molten aluminum. Before this process, flux powder spraying refining or online rotary degassing has been used. So the particles of C hydrogen that have not been removed in molten aluminum are more fine and dispersed. How to promote the accumulation and growth of impurity phases and hydrogen adsorption in the filtration of foam ceramics is particularly important. The mechanical interception of the “filter cake” effect of foam ceramics alone cannot achieve outstanding results. A new generation of foamed ceramic filter material is the research goal of this topic.
No Comments