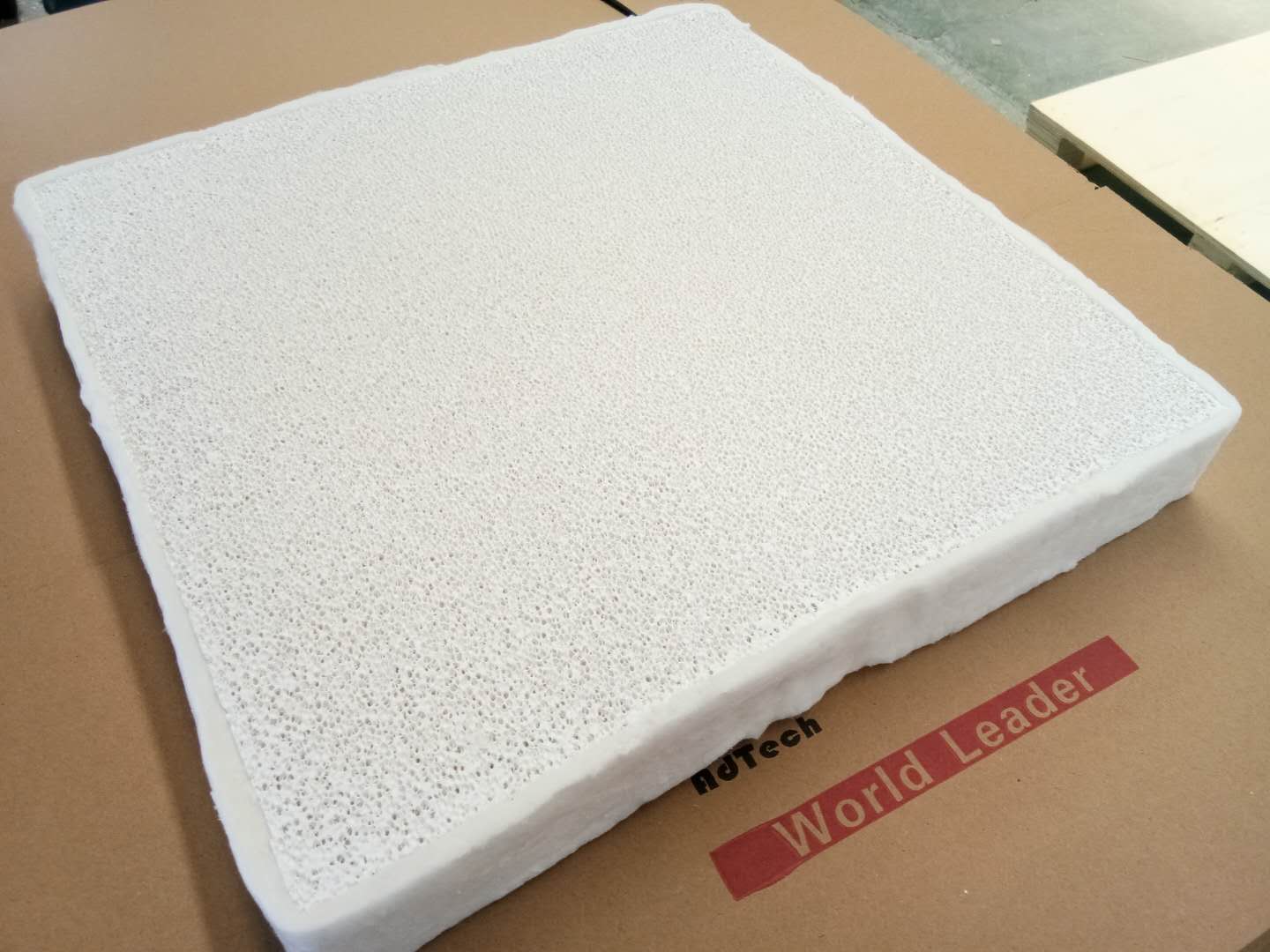
19 10月 Molten Aluminum Filter Hindalco Industries
Molten Aluminum Filter Hindalco Industries can effectively remove various impurities in molten aluminum. The sealing ceramic fiber gasket is attached around the filter plate to help seal the filter plate in the filter box and ensure that there is no molten aluminum on the edges.
Below we introduce the use of Molten Aluminum Filter Hindalco Industries for casting products
1. Check and clean up the debris on the surface of the filter box to keep the filter box clean and damaged.
2. Gently insert the Molten Aluminum Filter into the filter box, and then press the gasket on the filter plate to prevent the aluminum liquid from flowing or floating.
3. Preheat the filter box and the filter plate evenly to make it close to the temperature of the molten aluminum. The preheating temperature of the filter plate is not lower than 460℃.
Expanded cotton fabric is automatically sealed by thermal expansion.
The filter plate is not easy to float, and the adsorbed water is removed by preheating.
These parts are more suitable to help open the opening of the initial filter, prevent thermal expansion and contraction, and bring some plugs into the filter plate.
Electric heating or gas heating can be used for preheating. Normal heating is 15-30 minutes.
4. Pay attention to the change of the aluminum hydraulic head during casting, and maintain the required aluminum liquid flow rate. The typical starting indenter is 100-150 mm. When the molten aluminum starts to pass,
The indenter will move below 75-100mm, and then the indenter will gradually increase;
5. In the normal filtration process, knocking and vibrating the filter plate should be avoided. At the same time, the water tank should be filled with molten aluminum to avoid interference from molten aluminum.
6. After the filtration is completed, please remove the filter plate in time and clean the filter box.
The harm of metallurgical defects to aluminum processing deformation production and the mechanical properties of the final product cannot be ignored. Therefore, attention should be paid to the purification treatment of aluminum melt. Before the filter is used, the gas and slag content is too high, which will cause the ceramic foam filter to block. Therefore, adding a degassing device before filtering can make the purification process of liquid aluminum more smooth.
For the production of industrial and architectural aluminum rolled products, such as ingot casting or extrusion round ingot, ceramic filters can only be used in casting to meet product quality requirements. Single-layer filtration or double-layer filtration can be selected according to product requirements.
For the production of high-end products, deep bed filtration is recommended for process configuration: degassing device + deep bed filtration device + Casthouse Molten Aluminum Filter Medium. Ceramic plate filtration is used before casting to avoid media loss due to deep bed filtration, which will cause too many inclusions to accompany molten aluminum during casting, resulting in a lot of waste. And according to the output and production plan, consider the corresponding deep bed preheating method (online or offline). The process configuration recommendations for the use of tubular filters: degassing device + tubular filters (at least two parallel), most of the aluminum processing enterprises in Japan use this arrangement. In order to achieve energy saving and emission reduction and form an “electrolytic aluminum-aluminum processing” industrial chain, some enterprises use electrolytic aluminum liquid as raw materials to produce steel ingots. Since the impurity composition of electrolytic aluminum is complex and there are many non-metallic slags, it is recommended to use a ceramic filter device before the tubular filter.
Filtered with molten aluminum
After cleaning the filter box, coat the inner surface of the CFF filter box with a layer of BN refractory material, and then gently place the foam ceramic filter plate on it.
Correct preheating is an important part of the use of ceramic foam filter plates. Incorrect preheating methods often lead to the following problems:
Preheating of cracks;
The filter plate cannot be started (aluminum liquid cannot pass through).
No Comments