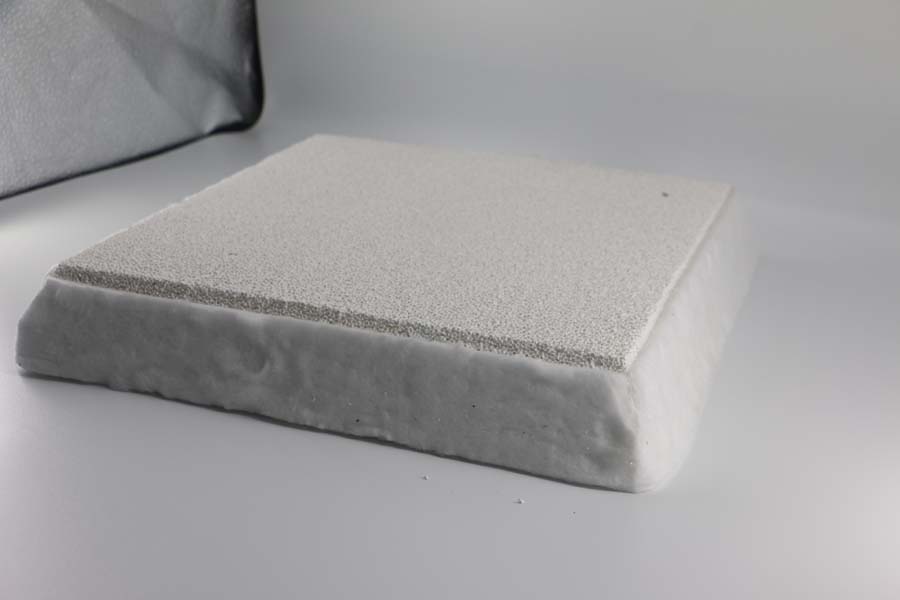
21 10月 Molten Aluminum Filter Aluminium Siberia
Molten Aluminum Filter Aluminium Siberia is mainly used for aluminum and alloy filtration in foundries and foundries.
Alumina ceramic filter has excellent resistance to the harshness and corrosion of molten aluminum, can effectively remove inclusions, reduce entrained gas and provide laminar flow, so that the filtered metal is significantly cleaner.
Cleaner metals result in higher quality castings, less scrap and fewer inclusion defects, which helps improve the bottom line.
Advantages of Molten Aluminum Filter Aluminium Siberia
-Reduce the amount of waste related to inclusions.
-Reduce costs associated with inclusion defects.
-Improve productivity through higher extrusion or rolling speeds.
-Due to the easy replacement of alloys, the flexibility of castings is improved.
-There is no fixed metal.
Application of alumina ceramic filter
Alumina ceramic filtration
It is made on the basis of a carrier and has a strong network structure and combined pores of organic foam.
The production process is as follows: The carrier is placed in the thixotropic alumina slurry, a square is applied at the center of the automatic extrusion correction process, so that the slurry is evenly deposited in the carrier foam, and after drying and solidification, the carrier is transformed into the final product. Firing and molding at a high temperature of 1180°C.
Installed in the filter bowl to filter the impurities in the molten aluminum alloy, which helps to meet the production requirements of high value-added and high-tech precision aluminum alloy castings such as computer hard disks, printed polyphenyl plates, canned materials, turbojet fan blades and PhD.
The hydrogen is absorbed and eliminated by the bubbles.
Removal of alkali metals through chemical interaction with chlorine (chloride formation);
The inclusions are trapped by bubbles and then rise to the surface of the melt as slag is formed.
Degassing efficiency standard design Box design Quality standard design Rotor standard design Immersion heater thermowell Gas standard design Standard design Seal design
The average degassing efficiency of the degassing box is 60%. When the liquid aluminum fueled by argon is ≤1%, the best degassing effect can reach 0.09 cm3/100 g.
The lining is made of high-silicon melt. The average service life of the inner cavity is 2 years, and the longest can be up to 3 years. Good non-stick aluminum effect. It will not pollute the aluminum melt. The internal structure has a baffle to ensure the stability of the surface of the aluminum melt. This can prevent the oxides from winding on the air surface and the aluminum melt into the aluminum melt, as well as the outflow of bubbles or residues.
According to Adtech China, the deputy CEO of Rusal stated that the company plans to substantially increase its supply to China next year and plans to sign a series of long-term contracts.
Rusal plans to supply 300,000 to 400,000 tons of aluminum to China in 2021, basically the same as in 2020.
Due to the plan to start the Taishet smelter, Rusal’s total production of Lu in 2022 will increase to about 4.3 million tons. It is expected that the global aluminum market will have a gap of more than 1.5 million tons this year, and the gap in 2020 will be 1.4 million tons.
No Comments