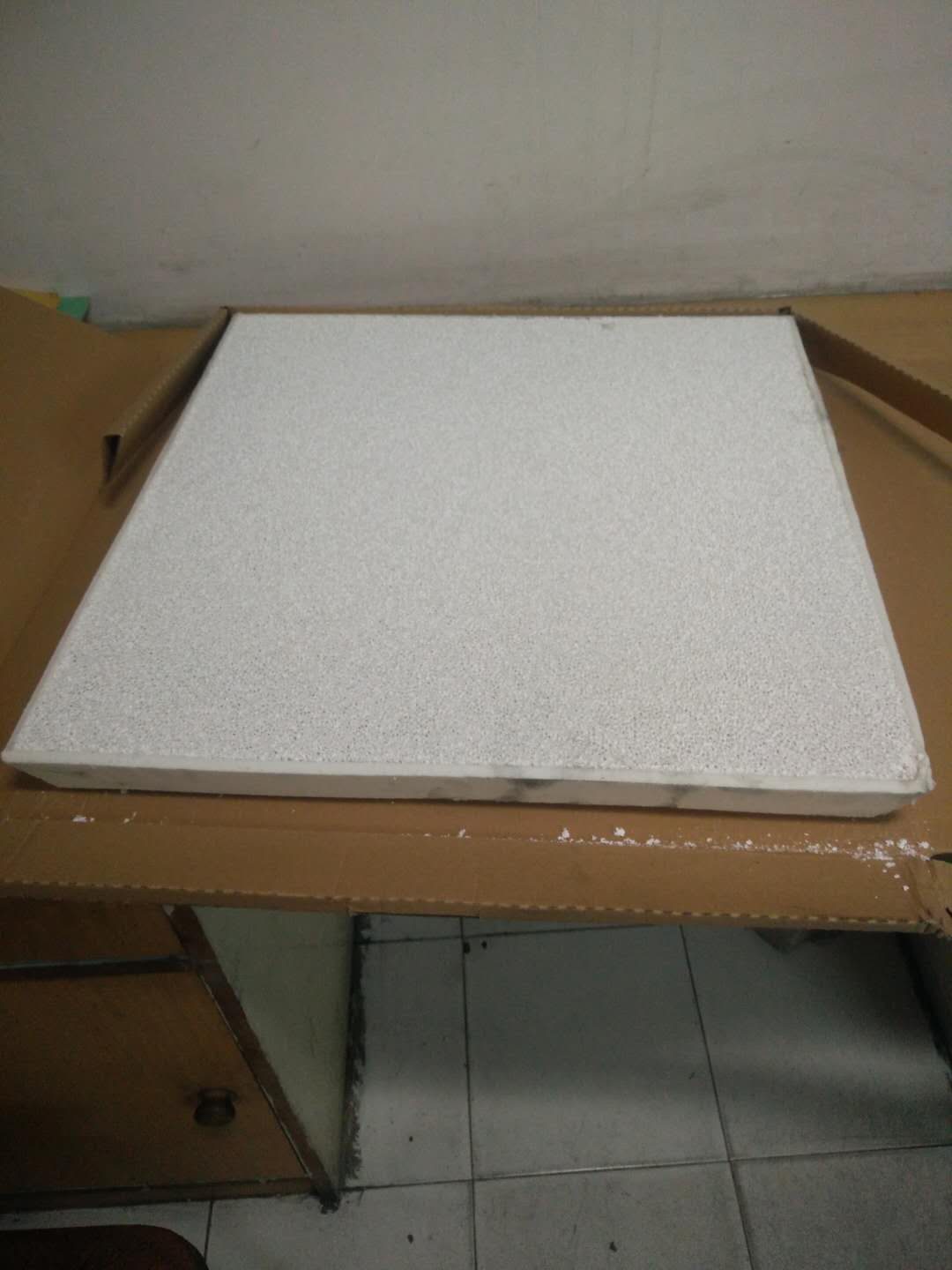
12 4月 Melt Aluminum Foam Ceramic Filter
Melt Aluminum Foam Ceramic Filter has the advantages of large filtering area, good thermal shock stability, high chemical stability, good molten aluminum erosion resistance and good filtering efficiency.
Therefore, as a new type of high-efficiency filter in the aluminum melt filtration and purification technology, it has attracted people’s attention.
At present, its application range has been extended to precision casting, cast steel industry and foundry industry.
Foam ceramic filters can improve the mechanical properties of castings, reduce the rate of casting rejects, increase the rate of finished castings, and extend the service life of metal cutting tools.
The molten metal foam filter can filter out non-metallic impurities in the metal casting process.
During the entire melting and casting process of liquid metal, non-metallic impurities enter the melt, which will adversely affect the quality of the melt. This is known to steel manufacturers, casters and metal workers.
Most non-metallic inclusions are refractory oxides whose melting point exceeds the melting temperature of steel.
These are mainly oxides of magnesium, calcium, aluminum, and silicon, which are part of the slag and lining materials.
Due to the deoxidation of steel, a large number of non-metallic inclusions are formed in the melt. The solubility of oxides in pure iron is negligible or nonexistent.
Non-metallic inclusions usually appear as solid dense particles. The oxide film in the melt is in a liquid state, but the viscosity is significantly higher than that of the molten metal.
Performance of Melt Aluminum Foam Ceramic Filter
1. The ceramic foam filter should have good room temperature strength, and no slag should be dropped during transportation and operation.
2. It has a certain high temperature strength, thermal shock resistance, and liquid metal corrosion resistance.
3. Good chemical stability, does not react with liquid alloy.
4. It has a suitable pore size, and has good filtering ability for alloy liquid and non-metallic inclusions; appearance 5. Good quality: no deformation, small size deviation, uniform pore size, and no clogging.
The filter is a large ceramic foam made of highly refractory material with a certain number of pores and a specific surface area.
The melt cleaning mechanism using ceramic foam filters is quite complicated and little-known, but despite this, the cleaning efficiency of this method is unique. This can be confirmed by the foundry workers, who can use similar materials produced abroad to produce high-quality castings.
Depending on the molten metal foam filter and its configuration, the melt can be completely and selectively degassed. When the contaminated metal passes through the filter, an electromotive force is generated inside the ceramic matrix, which can be controlled by the phase and chemical composition, and the specific surface flow rate of the ceramic and the metal. When the liquid metal flows through the ceramic filter, in addition to being purified, it is further homogenized. This of course will affect the quality of the casting.
The existing world experience uses ceramic foam filters to clean low-melting metals, and uses investment casting to filter steel through precision casting. Appropriate structural improvements will allow you to clean larger volumes of liquid metal.
When the filter overgrows in one layer, the metal rises to the next layer of the filter, which may have a different structure and number of holes. There is no filter in the upper layer of the holes in the partition. In this way, when casting metal according to its level, it is possible to control the quality of the steel ingot according to the content of non-metallic inclusions. “Coarse” and “fine” filters can be installed in the opening of the partition wall.
At present, we are working with a number of metallurgical companies to test this method of cleaning non-metallic inclusions in molten metal, and to test the composition and parameters of ceramic filters.
No Comments