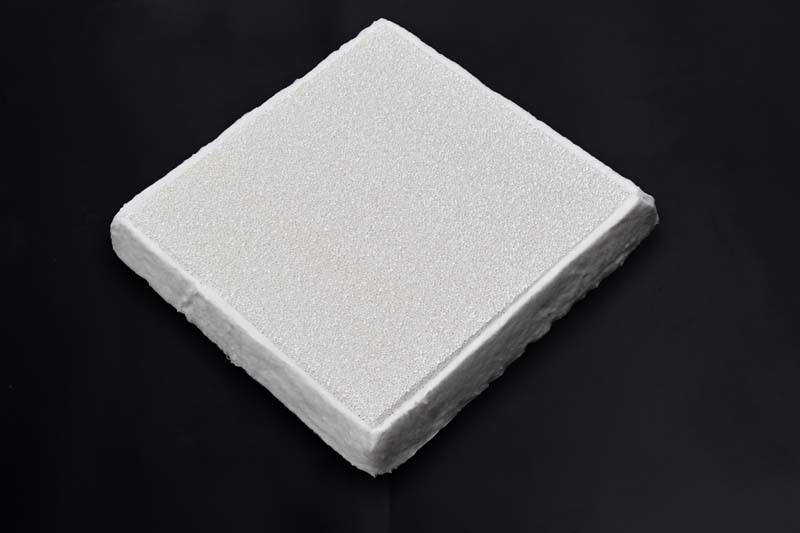
24 8月 Japan Aluminium Ceramic Foam Filter
Japan Aluminium Ceramic Foam Filter is widely used in the aluminum casting industry for aluminum and its alloy materials that require higher and higher purity and quality.
According to its different mechanisms and forms, purification methods can be divided into adsorption purification, physical purification and filtration purification.
When Japan Aluminium Ceramic Foam Filter is filtering liquid aluminum, the liquid aluminum flows through the tortuous holes of the ceramic filter plate. The combined action of force, etc., is retained on the inner surface of the hole of the ceramic filter plate and the gap cavity, thereby separating the slag and the molten aluminum.
After a period of filtering, the slag remaining on the ceramic filter plate also participates in the adsorption of the slag, which can play a filtering role.
Since the performance of the slag adsorbed on the ceramic filter plate is exactly the same as that of the slag to be adsorbed in the molten aluminum, the surface area ratio is much larger than that of the ceramic filter plate, and the surface activity is also much greater than that of the ceramic filter plate.
Therefore, the ability to adsorb and trap the slag in the molten aluminum is far greater than that of the Alumina Ceramic Foam Filter. Because of this, the ceramic filter plate can filter out the fine slag that is many times smaller than its own hole.
Ceramic Filter can melt the molten metal into a smooth, uniform and clean liquid after passing through the honeycomb holes.
The unique honeycomb structure can adsorb some small particles on the surface.
Remove impurities that cause surface problems, low strength and hardness.
Such as some non-metallic particles, slag, refractory fragments, etc., the stable metal laminar flow makes the filling effect better.
On the one hand, the bubbles overflow, on the other hand, it reduces the erosion of the sand mold and reduces the scrap rate of the product.
It can effectively remove non-metallic inclusions in liquid metal, improve the structure and mechanical properties of castings, produce high-quality precision castings, reduce casting scrap rate, and reduce tool wear during casting processing.
The foam ceramic casting filter has significantly improved economic and social benefits.
There are many reasons for aluminum pollution. On the one hand, during the smelting process, aluminum is exposed to the atmosphere in the furnace in a molten or semi-molten state. It is easily oxidized, reacts with water vapor and absorbs hydrogen, and is easy to form various forms of non-melt. Metal slag (such as furnace lining fragments, chlorides, carbides in flux, etc.) and coarse intermetallic particles.
No Comments