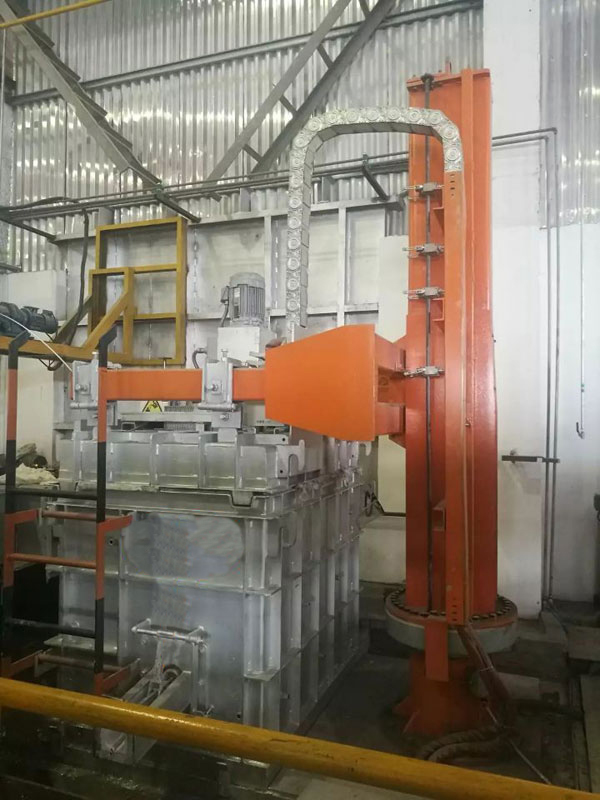
19 4月 Degassing Machine Pune
Degassing Machine Pune
Degassing Machine Pune is based on the principle that dissolved hydrogen gas will move from an area of high concentration (in the melt) to an area of low concentration (in the inert gas).
Hydrogen gas disperses in molten metal as it would if it were released in any confined space.
It will maintain a constant concentration throughout the melt.
Hydrogen gas can migrate in liquid metal almost as fast as it can in air.
Therefore, it is unnecessary to bring every ounce of metal in contact with the inert gas.
The efficiency of aluminum degassing is determined by two factors, the transfer rate across the metal/gas interface and the total surface area available for transfer.
Chlorine was the original gas of choice but due to its hazardous nature, most foundries switched to other gases.
However, many foundries have not considered the hazardous materials released by the breakdown of any specialty gas used.
Degassing Machine Pune bubbled specialty gases (Chlorine, Freon, or SF6) through the metal to speed the hydrogen transfer across the metal gas interface into large bubbles.
There was a practical limit to hydrogen removal on humid days because as the large bubbles would break the surface, an increased surface area of metal was created which then absorbed more hydrogen from the humid atmosphere.
Degassing Machine Pune works on the principle of increasing the surface area of an insert gas exposed to the metal.
The larger surface area increases the rate of transfer from metal to the inert gas.
Degassing Machine Pune Procedures
Degassing is usually accomplished in one of three areas of the metalcasting facility:
1. In the transfer ladle, used to convey metal between melting and holding furnaces.
2. In crucible furnaces, usually just before the molten aluminum is cast.
3. In an in-line system, when the metal is conveyed to holding furnaces through a launder.
The first two options are most common and the degassing operation for both is typically accomplished using a rotary impeller degasser (RID).
In practical terms, all rotary degassers are not created equal. It is important to have an optimum head design to produce highly efficient, small bubbles. Significant cost savings may be realized from shorter treatment times and reduced gas usage.
In the past, the metalcasting industry has gravitated toward simple head designs, which are less costly to machine but produce larger bubbles.
This path presents a false economy due to reduced efficiency.
Degassing Machine Pune Adjusting Process Parameters
Once the Degassing Machine Pune RID unit is fully lowered into the liquid metal with the shaft in place, the degassing operation can begin.
The best shaft location is slightly off the centerline of the crucible or ladle to help avoid vortex formation with its circular rotation in the liquid metal.
An offset distance of 2-4 in. from the centerline is usually sufficient.
The use of a baffle plate also is a good idea, because the baffle opposes the circulation movement of metal and reduces vortex formation.
No Comments