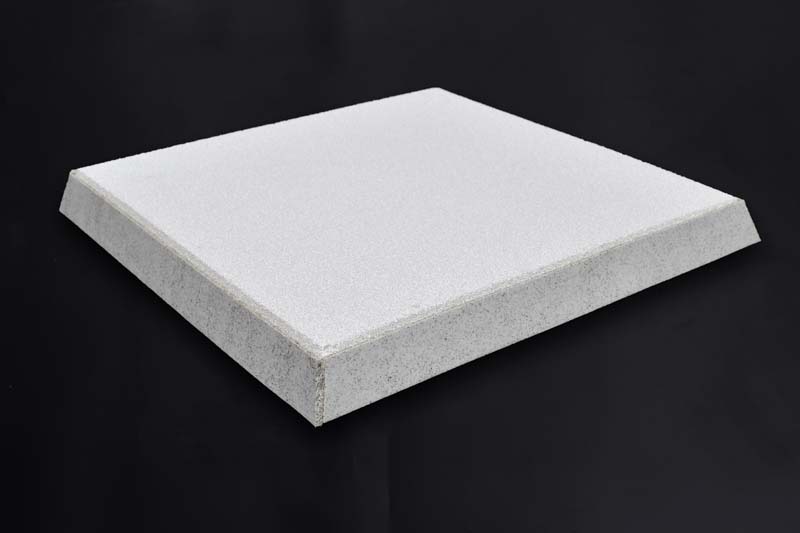
23 8月 Chuo Kosan Ceramic Foam Filter
Chuo Kosan Ceramic Foam Filter is used to purify molten aluminum in the process of aluminum rods and ingots in aluminum melting and casting plants. It is placed in an ordinary steel shell lined with prefabricated refractory brick pads. It is arranged horizontally in the metal launder, that is, between the runner and the casting well.
Therefore, there is no need to make major changes to the existing casting system, and only a small space is required.
In addition, the filter plate can effectively filter all metals within one melting time, and it is very convenient to remove or replace after use.
Alumina filter production ceramic filter plate gasket
There is a sealing gasket around the ceramic filter plate, which acts on the contact surface of the filter plate and the filter box to prevent the aluminum liquid from leaking through the contact surface.
Our filter plates use three different specifications of sealing gaskets: fiber paper edge; fiber cotton edge; puffed cotton edge.
Advantages of Chuo Kosan Ceramic Foam Filter
1. Adopt the principle of adsorption to filter, which can effectively remove large inclusions in molten aluminum and effectively adsorb micron-level inclusions. The filtration accuracy of the same mesh size is very high.
2. No slag drops, effectively reducing the pollution of molten aluminum.
3. Good thermal shock resistance and improved corrosion resistance to molten metal.
Description of Chuo Kosan Ceramic Foam Filter
1. Check and clean up the debris on the surface of the filter box, and keep the filter box clean and undamaged.
2. Gently put the filter plate into the filter box, and then press the gasket on the filter plate with your hand to prevent the aluminum liquid from flowing or floating.
3. Preheat the filter box and the filter plate evenly to make it close to the temperature of the molten aluminum, and the preheating temperature of the filter plate is not less than 260°C. Preheating to remove adsorbed water helps to immediately open the initial filter pore size and prevent thermal expansion and contraction from causing clogging of the filter plate. Electric heating or gas heating can be used for preheating. The normal heating time is 15-30 minutes.
No Comments