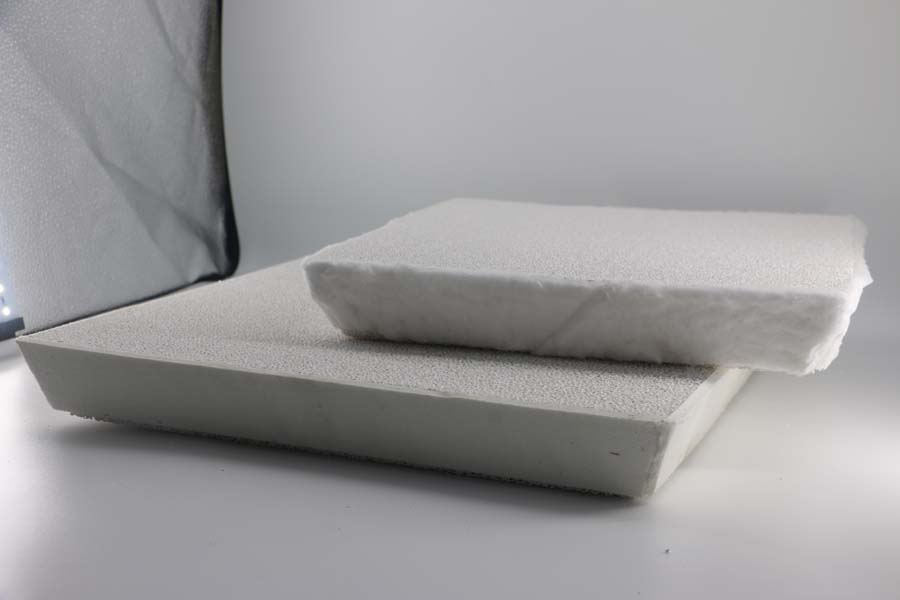
16 8月 Ceramic Foam Filter Irkutsk Aluminium
Ceramic Foam Filter Irkutsk Aluminium is mainly used for filtering aluminum and aluminum alloys in aluminum foundries. It can effectively remove molten aluminum inclusions, and then the filtered metal is significantly cleaner.
Ceramic Foam Filter Irkutsk Aluminium has excellent resistance to molten aluminum erosion and corrosion. They continue to provide high-quality clean aluminum and aluminum alloy products during the aluminum casting process, reducing aluminum ingots, aluminum rods, and inclusion defects, all of which help To increase profits.
Ceramic foam filters can be manufactured through specific procedures and have unique skeleton pores, just like the shape of foam (called three-dimensional connected channels) and countless pores (only found under a large microscope).
The Irkutsk Aluminum Smelter is one of the largest aluminum smelters in Russia and the oldest smelter in Eastern Siberia.
One of the oldest smelters in Siberia, put into operation in 1962.
In 2010, the smelter was equipped with a new casting workshop, which increased the plant’s annual production capacity by 165,000 tons.
At present, the IrkAZ product range includes more than 100 aluminum alloy technical specifications and more than 30 export rod specifications.
High value-added products accounted for more than 70%. The output of the highest grade aluminum is 95%.
In 2015, IrkAZ launched the Eco-Soderbergh project to transfer the 1, 3, and 4 series of IrkAZ electrolysis to this technology.
The implementation of the EcoSoderberg project will reduce emissions to the atmosphere by 30% and significantly improve environmental performance.
The project is expected to be completed in 2020.
The 5th series of the Irkutsk aluminum smelter completed by RUSAL in 2008 was put into operation. It was the first major industrial project in the Baikal region in modern Russian history.
The construction of the new electrolysis building was completed within 3 years, and the commissioning of the new facility has increased Irkutsk’s aluminum output by 170,000 tons per year. The project investment exceeds 600 million U.S. dollars.
The IrkAZ 5th series is known for its advanced technology, which helped significantly reduce the environmental impact of production during construction. The dry gas cleaning system installed in the 5th series can capture 99.5% of fluoride and electrolytic dust, and the electrolytic cell with flame anode running at 300 kA, which is much more efficient than similar.
Also in 2008, the Irkutsk Aluminum Smelter implemented a project to expand the casting capacity developed by SibVAMI experts.
No Comments