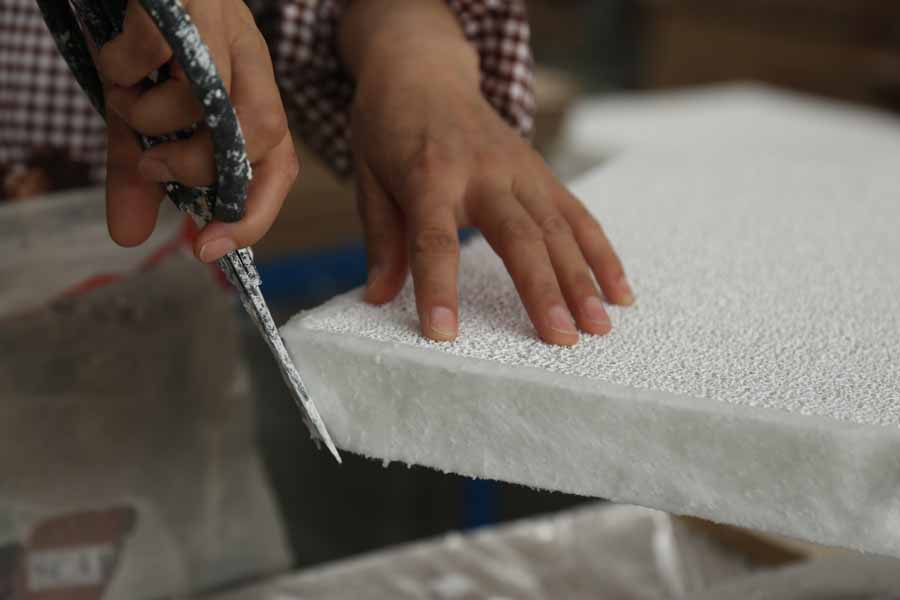
10 8月 Ceramic Foam Filter Bharat Aluminium Korba
Ceramic Foam Filter Bharat Aluminium Korba has an excellent filtering effect on molten aluminum. It uses a three-dimensional structure to effectively remove oxide inclusions and other non-metallic inclusions by blocking capture and adsorption. Whether it is aluminum rods, aluminum ingots or aluminum plate melted castings after filtering, the product quality will get satisfactory results.
In the use of Ceramic Foam Filter Bharat Aluminium Korba, two aspects must be considered.
1. Filtration makes the flow of molten aluminum become orderly and relatively calm, without turbulence.
2. The solid slag in the molten metal is effectively removed, and the quality of castings is rapidly improved.
Ceramic foam filter Dimension
660x660x50(26 inch)
584x584x50(23 inch)
508x508x50(20 inch)
432x432x50(17 inch)
381x381x50(15 inch)
305x305x50(12 inch)
228x228x50(9 inch)
178x178x50(7 inch)
The aluminum ingot casting process uses molten aluminum to be injected into the mold. After being cooled into a cast slab and taken out, the injection process is a key step for the quality of the product.
The casting process is also the physical process of crystallizing liquid aluminum into solid aluminum. The process flow of casting aluminum ingots is roughly as follows:
Aluminium tapping-slagging-weight checking-batching-furnace loading-scouring-casting-aluminum ingots for remelting-finished product inspection-finished product checking-warehousing
Aluminium tapping-slagging-weighing-batching-furnace loading-refining-casting-alloy ingot-casting alloy ingot-finished product inspection-finished product inspection-warehousing
Commonly used casting methods are divided into continuous casting and vertical semi-continuous casting
Continuous casting
Continuous casting can be divided into mixed furnace casting and external casting. All use continuous casting machines. Mixing furnace casting is the process of casting molten aluminum into the mixing furnace, and is mainly used to produce aluminum ingots for remelting and casting alloys.
Outer casting is carried out directly from the ladle to the casting machine, which is mainly used when the casting equipment cannot meet the production requirements or the quality of the incoming materials is too poor to be directly fed into the furnace.
Since there is no external heating source, it is required that the ladle has a certain temperature, generally between 690°C and 740°C in summer and 700°C to 760°C in winter to ensure that the aluminum ingot has a better appearance.
No Comments