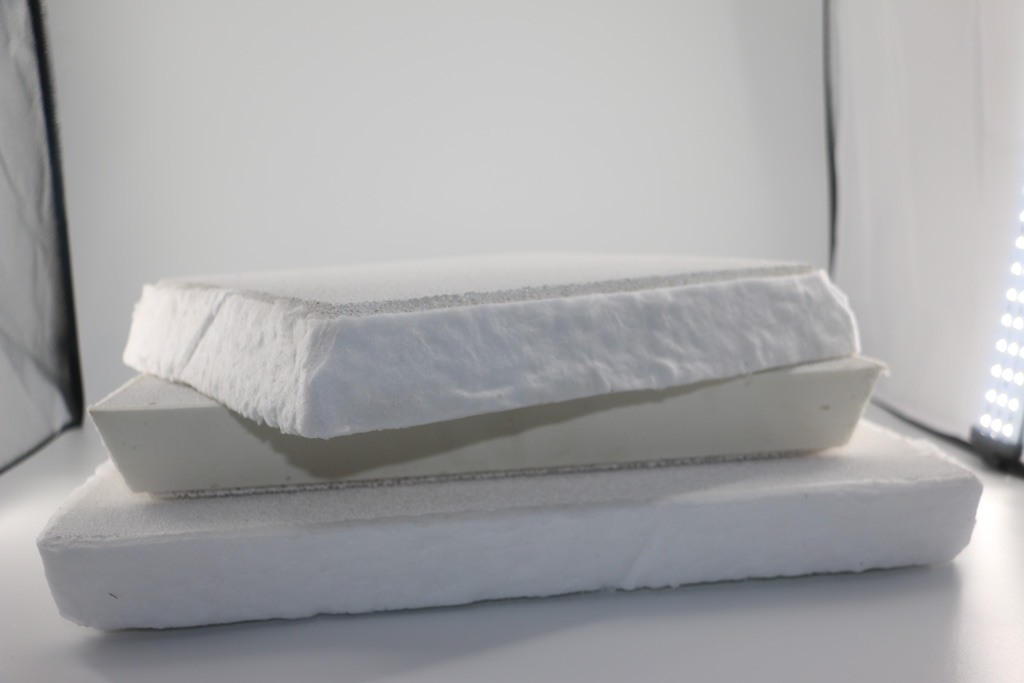
21 2月 Ceramic Filter Product
Ceramic Filter Product can effectively remove various impurities in the aluminum melt, greatly improving the cleanliness of the metal, thereby improving product quality, reducing costs, and improving productivity to varying degrees.
The operation is simple, the process is easy to control, does not require excessive investment, and is worthy of promotion and application.
The process and equipment of foam ceramic filtration and aluminum liquid purification are applicable to all aluminum production departments, including book plates, strips, foils, rods, tubes, wires, extrusion materials, forgings, original aluminum ingots, recycled ingots and continuous casting.
Advantages of Ceramic Filter Product
It is estimated that regardless of the huge benefits brought by the use of ceramic foam filter plates to purify molten aluminum and aluminum foil and their products (such as cans, car sequins, PS printing plates, etc.), aluminum alloy manufacturers have several obvious advantages as far as it is concerned. :
1. Improve extrusion efficiency
When using the filter plate to purify the 6063 alloy extruded billet, the extrusion speed is increased by about 20%, and the productivity is increased by nearly 15%.
2. Extend mold life and reduce mold maintenance times.
3. Reduce stress
4. Greatly improve the surface quality of aluminum profiles.
from above. In terms of reducing production costs and improving product quality, the use of ceramic foam filter plates to purify aluminum melt has great advantages.
The ceramic filter plate is used to purify molten aluminum. The equipment is an ordinary steel shell lined with prefabricated refractory materials.
It is prepared horizontally in the metal flow cell, that is, between the orifice and the casting well.
Therefore, there is no need to make major changes to the existing casting system, but only a small space.
Moreover, the filter plate can effectively filter a molten metal, and it is very convenient to remove or replace after use. It is also suitable for horizontal or vertical casting systems.
Purchase installation and function of aluminum ceramic foam filter from Adtech
The filtration efficiency of the foam ceramic board is closely related to its correct installation and use.
At the same time, due to the filtration process, the conventional and necessary measures taken to reduce the generation of inclusions in process operations such as smelting, furnace treatment and casting cannot be ignored.
It is also necessary to prevent re-contamination of the filtered clean aluminum liquid.
Its installation and use usually need to pay attention to the following aspects:
1. Correct use of filter plate:
The size of the filter plate and the number of holes must be selected according to the flow range of the specific casting type, the maximum level of the metal during the filtration process, the total filtration volume and the cleanliness of the original aluminum liquid.
2. The pre-melting filtration treatment cannot be ignored:
Such as ordinary slag from aluminum melting furnace and holding furnace, cleaning furnace; furnace refining. In particular, an online degassing device is still needed, because it not only reduces the hydrogen content of the melt, but also removes some non-metallic inclusions.
3. The filter plate must be compatible with the square refractory block:
The two are suitable for sealing to prevent the metal from flowing into the casting box from the gap without being filtered, and also avoid the foam filter plate from floating in the aluminum water due to the light weight.
4. Warm up before use:
Preheat to remove moisture and facilitate initial transient filtration. Electric heating or gas heating can be used for preheating. Normally, it takes about 15 minutes.
5. In the normal filtering process, no slag is needed to avoid knocking and vibrating the filter plate. At the same time, the washing tank should be filled with molten aluminum, so as not to worry too much about molten aluminum.
6. After casting, drain the metal in the flow cell and filter plate. There is a vibrator abroad, which is placed on the filter plate and shaken for one minute to shake off about 75% of the remaining liquid metal from the filter plate.
7. Finally, clean the periphery and remove the filter plate after curing.
No Comments