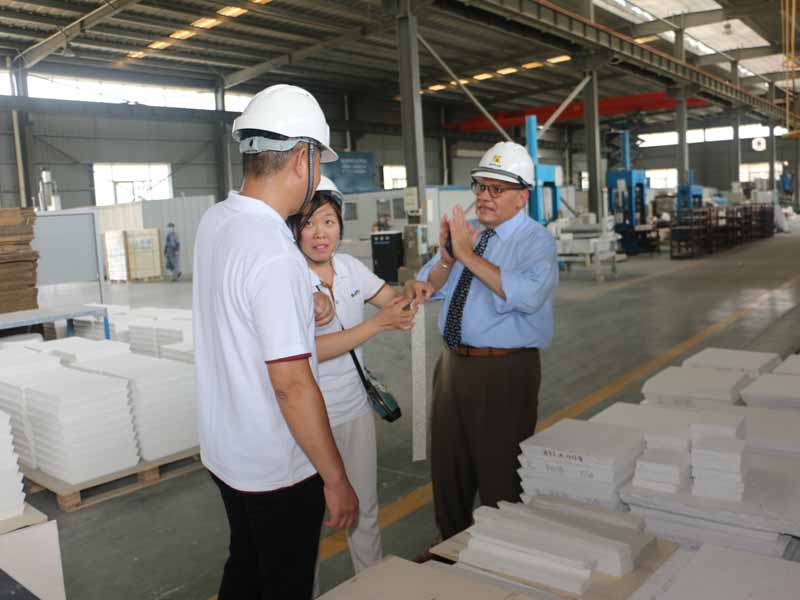
23 7月 Ceramic Filter Plate
Ceramic Filter Plate
A general term for aluminum-based alloys based on aluminum.
The main alloying elements are copper, silicon, magnesium, zinc and manganese. The secondary alloying elements are nickel, iron, titanium, chromium and lithium.
The aluminum alloy has low density, but high strength, close to or exceeds high-quality steel, good plasticity, can be processed into various profiles, has excellent electrical conductivity, thermal conductivity and corrosion resistance. It is widely used in industry and is used second only to steel.
Aluminum alloy is a kind of non-ferrous metal structural material widely used in industry, in aviation, aerospace, automobile, machinery manufacturing, shipbuilding.
Smelting and casting of aluminum alloys is the main link in casting production.
Strictly control the whole process of smelting and casting, and play an important role in preventing casting defects such as pinholes, inclusions, under-casting, cracks, pores and shrinkage.
Since the aluminum melt has a large tendency to absorb hydrogen, has a strong oxidizing ability, and is easy to dissolve iron, it is necessary to take simple and cautious precautions in the smelting and casting process to obtain a high-quality casting.
Characteristics of Ceramic Filter Plate
Ceramic Filter Plate can effectively remove large inclusions in aluminum fluid and adsorb fine inclusions particles of micron size, which plays a role in improving surface quality, product performance and microstructure, and improving yield. It is widely used in the production fields of aluminum profile, aluminum foil and aluminum alloy.
Ceramic Filter Plate production process
Ceramic Foam Filter adopts organic Foam Foam with three-dimensional mesh structure and connected pores as carrier to invade into special Ceramic slurry with thixotropy.
Special roller extrusion process is adopted to evenly spread Ceramic slurry onto the framework of the carrier, which is then baked and cured at high temperature.
Ceramic Filter Plate method of use
1.Clean the filter box.
2. Gently put the filter plate into the filter box and press the sealing gasket around the filter plate with your hands to prevent the side flow of liquid aluminum.
3. Uniformly preheat the filter box and filter plate to make it close to the temperature of liquid aluminum. Preheat to remove moisture and facilitate initial instantaneous filtration. Preheating may be done by electric or gas heating. Normally, it takes about 15-30 minutes.
4. when casting attention to observe changes in aluminum hydraulic head, normal starting pressure head is 100-150 mm. When aluminum begins through, pressure head will drop to 75-100 mm less, then pressure head will slowly increase.
5. During the normal filtration process, avoid knocking or vibration on the filtration plate. Meanwhile, the flow trough should be filled with aluminum-water to avoid too large disturbance of aluminum-water.
6. Take out the filter plate and clean the filter box after the filtration.
Ceramic Filter Plate light transmittance
Light transmittance refers to the effective filtration area of ceramic foam filter plate.
The higher the light transmittance is, the fewer the blind holes are, and the more effective filtering holes.
The foam ceramic filter plate to be tested is placed on the light box with built-in 200W incandescent bulb, and the transparent square plastic plate with uniform cloth 5.0×5.0mm square is used to measure the light transmittance of the large surface of the filter plate.
So as to calculate the light transmittance of the tested filter plate.
In this standard, the light transmittance (through-hole rate) of the filter plate shall be more than 95%.
Sorry, the comment form is closed at this time.