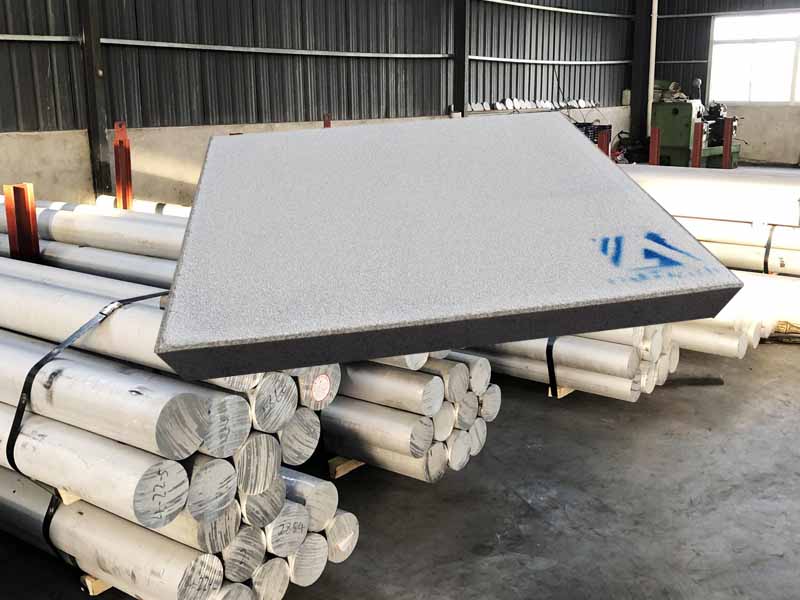
09 11月 Ceramic Filter Malaysia Aluminium
Ceramic Filter Malaysia Aluminium has the characteristics of large filtering area, good thermal shock stability, high chemical stability, good resistance to metal erosion and good filtering efficiency.
Therefore, in the metal melt filtration and purification technology, as a new type of high efficiency filter, it has received the attention of aluminum melting and casting plants.
Ceramic Filter Malaysia Aluminium is an alumina-based ceramic foam filter, which can be widely used for filtering in the casting process of aluminum, aluminum alloy and other non-ferrous metals. This type of filter can be placed in standard filter boxes, holding furnaces , etc.
The role of ceramic foam filter
Filter inclusions in molten metal.
Rectification, turbulent flow of molten metal; the ultimate goal is to improve the quality of castings and improve the surface defects of castings. However, the design is unreasonable during use, resulting in worsening of casting defects.
1. The casting: 10~25ppi
2. Semi-continuous casting: 30~60ppi
3. High-quality aluminum or sheet: 50~60ppi
4. Continuous casting and rolling: 50~60p
Malaysia Aluminium introduces the usage of Ceramic Filter
1. Check and clean up the dust on the surface of the Casthouse to keep the Casthouse clean and undamaged.
2. Gently put the Asian Foundry Filters into the filter box, and press the gasket around the filter plate to prevent the aluminum liquid from flowing or floating.
3. Preheat Casthouse and Asian Foundry Filter to make it close to the temperature of molten aluminum. The preheating temperature of Asian Foundry Filter is not lower than 460℃, and the expanded cotton is automatically sealed by thermal expansion. Asian Foundry Filter is not easy to float, heat to remove absorbed water. The parts are more conducive to opening the opening of the initial Asian Foundry Filter aperture, preventing thermal expansion and contraction from causing some blockages to enter the filter plate. Electric heating or gas heating can be used for preheating. Normal heating is 15-30 minutes;
4. Pay attention to the changes of the aluminum hydraulic head during casting to maintain the required aluminum liquid flow rate. The normal initial pressure head is 100-150mm. When the molten aluminum starts to pass,
The indenter will drop below 75-100mm, and then the indenter will slowly rise;
5. In the normal filtering process, knocking and vibration of the Asian Foundry Filter should be avoided. At the same time, the launder should be filled with molten aluminum to prevent the interference of molten aluminum;
6. After the filtering is completed, remove the Ceramic Foundry Filter in time and clean the Casthouse.
No Comments