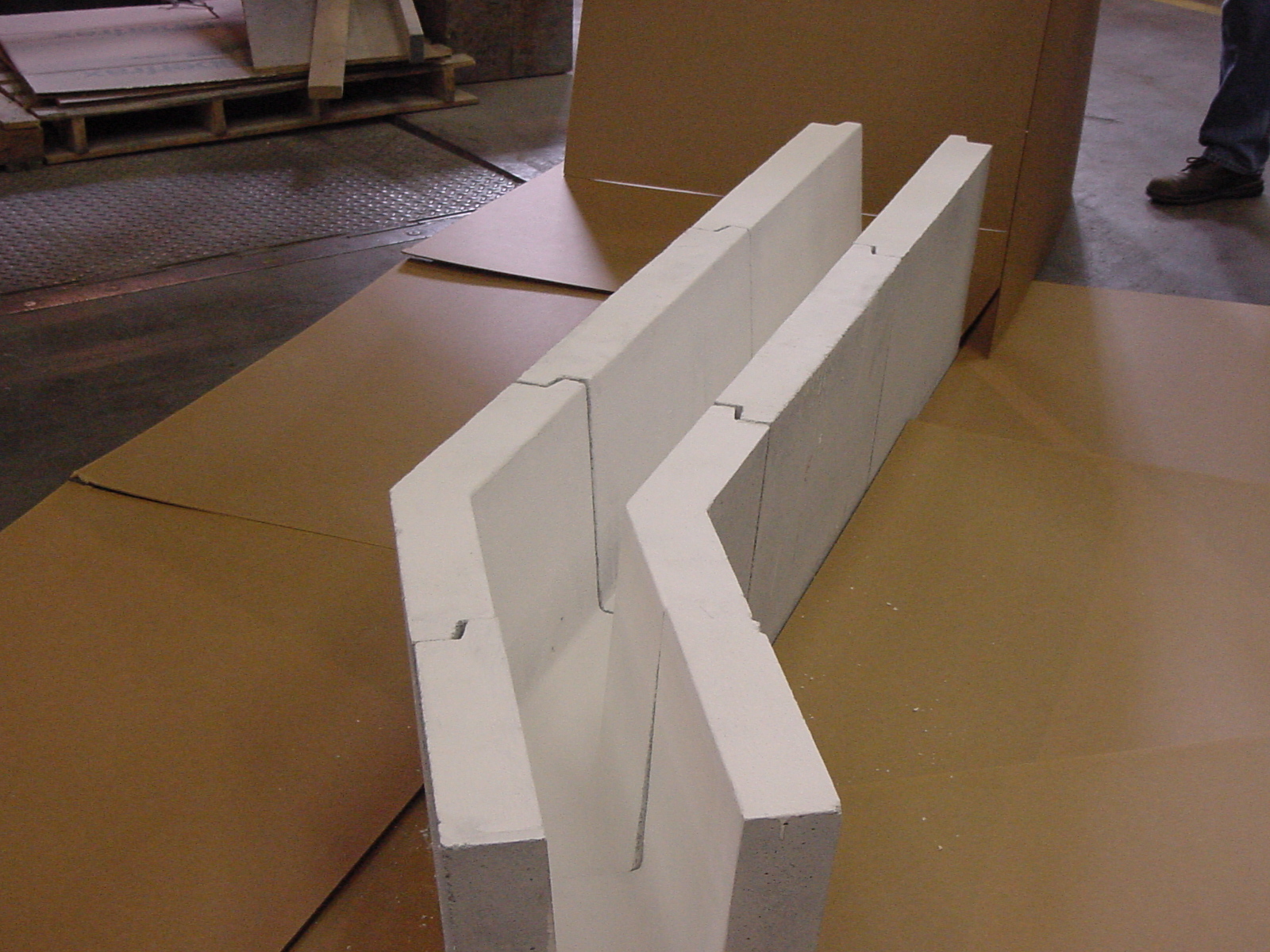
08 12月 Casting Line
Casting Line
Adtech offers complete refractory engineering services for aluminium casting lines and their associated systems:
Inspections
Material evaluation and selection
Thermal studies
Complete design of new launder lines or launder line extensions
Fabrication and installation drawings
Technical specifications
Tender documents and forms
Launder Casting Line
Molten metal is transferred from the remelt/holding furnace through a launder line to the casting machine. If the launders are not covered and heated, the metal cools as it travels the length of the launder line. Because casting machines require metal at a specific temperature, the operating temperature of the furnace is related to the thermal efficiency of the launder line. Therefore a thermally efficient launder line, allowing a lower operating temperature in the furnace, usually results in energy savings and reduced hydrogen absorption in the molten aluminium.
When launders are not fully preheated, heat is absorbed from the molten metal until the launder line reaches equilibrium. This usually results in the first metal of each casting being drained off into pans until the temperature stabilizes and the metal can be redirected into the casting machine. The preheat temperature and the thermal efficiency of the launder line affect the amount of metal lost each casting and the time required before the system reaches equilibrium.
The metal going into the casting machine must be free of “inclusions”. The surface quality of the launders can affect the risk of refractory pieces being included in the metal flow.
For a number of years Adtech has fabricated high quality refractory casting line launders.
Through much time and energy spent on research and development, Adtech has developed forming and casting techniques that result in launders with an unparalleled quality of surface finish.
Further, Adtech’s specialized forming techniques reduce stresses on the launders during deforming. This reduces the occurrence of micro-cracks and permits the launders to retain their maximum mechanical and thermal shock resistances.
Adtech casts launders in several different materials depending on the specific operating conditions. Different materials may even be used in the same installation according to the requirements of different “zones”.
Adtech’s engineering department has developed a system of non-steady state heat transfer calculations that permit it model and optimize the thermal performance of casting lines based on different refractory, insulation and pre-heat configurations. They can also design the launder geometry to specific flow rate, maximum velocity and time of retention criteria.
All of the above allow Adtech to provide high performance casting line launders, and complete casting line launders solutions, adapted specifically to client needs.
Filtration Equipment Casting Line
Ceramic Foam Filter (CFF) Bowls
“bowls” incorporated into casting lines. They are used for relatively coarse filtration of molten metal.
Adtech designs and fabricates CFF bowls and/or the complete steel shell/refractory bowl system together.
Bowls can be fabricated in different refractory concretes, selected according to clients criteria, e.g. long life time, insulating value, metal penetration resistance (non-wetting).
Very smooth, non-porous surface finish.
Adtech’s specialized forming techniques reduce stresses on the filter bowls during deforming. This reduces the occurrence of micro-cracks and permits the filter bowls to retain their maximum mechanical and thermal shock resistances.
Degassing equipment Casting Line
Degassing is an important step in the production of aluminium. Aluminium quality can be improved by removing hydrogen gas, the only gas soluble in molten aluminium. Degassing equipment is inserted into the launder line between the furnace and the casting machine. Degassers are commonly lined with refractory tiles similar to the rest of the launder line. However, because of the added turbulence of degassing processes, these tiles are subject to more wear.
Baffles are used at the entrance and the exit of the degasser to create a gas pocket above the molten metal within the degassing unit. The air in this gas pocket is replaced with an inert gas, often argon, to limit oxidation of the aluminium during the degassing process.
Adtech fabricates the refractory launder tiles and baffles to line degassers that provide:
High wear resistance
Resistance to chemical attacks (i.e. non-wetting to aluminium)
Low maintenance and easy cleaning
No Comments