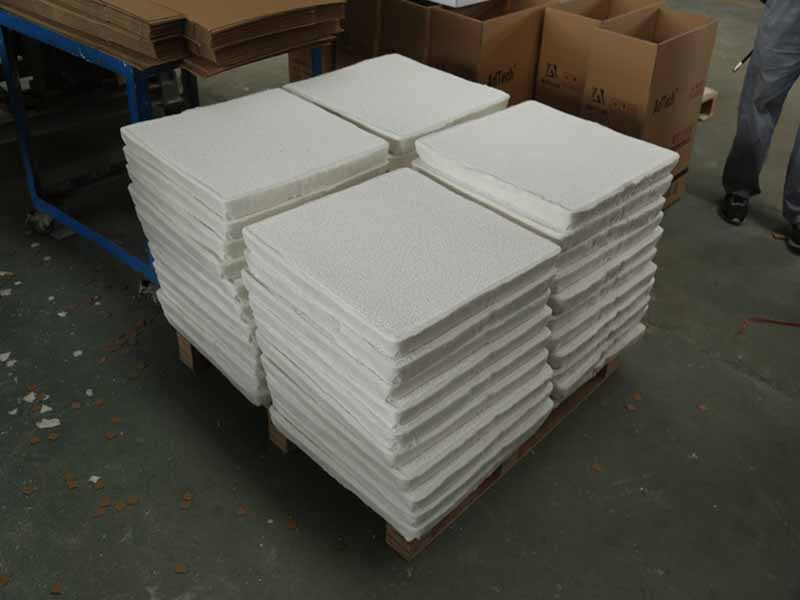
01 4月 Alumina Filter Filtration
Alumina Filter Filtration is widely used in the foundry industry to filter gas and non-metallic impurities in the process of melting and forming castings for aluminum alloys, thereby reducing the performance and processing performance of the castings.
The currently developed ceramic foam filter provides a new type of high efficiency filter for the production of aluminum alloy castings.
Different from the usual single-layer drilling screen and glass fiber screen, it has a multi-layer mesh and curved through holes, which can fully filter out the small non-metallic inclusions in the aluminum alloy melt, thereby improving the quality of castings.
In the process of Alumina Filter Filtration, the filter flatly filters out small inclusions, and the number of effective crystal nuclei in the aluminum liquid is reduced.
Therefore, the liquid nucleus grows under large super-condensation conditions, the solidification time is shortened, and the structure is optimized: the hydrogen content in the aluminum liquid is reduced.
Hydrogen atoms can absorb some oxidized inclusions, and the oxidized inclusions can serve as the core of bubble growth, so the inclusions are protected and the gas on them is also removed.
By adding, the harmful elements (sodium and potassium) in the aluminum liquid can be removed. According to different customer requirements or on-site environmental conditions, selecting a filter plate suitable for ensuring product quality can effectively control the slag content.
The ceramic foam filter plate is installed on the Filter Liner between the furnace mouth and the manifold.
The closer the filter box is to the manifold, the better. The reason is that the flow distance of the filtered aluminum liquid can be shortened, thereby reducing or avoiding the regeneration of oxides.
The molten aluminum flows out from the furnace mouth through the filter box, and then flows into the distribution plate through the flow trough. When the filtering device is activated, the drop before and after the melt filtering is approximately 30 mm.
With the extension of the filtration time, the inclusions on the surface of the filter plate and the hole wall increase, the filtration flow decreases, and the front and rear drop increases, and the drop increases to 50-100mm at the end of pouring.
Ceramic fiber filtration technology is one of the filtration technologies that has developed rapidly in recent years.
Compared with the traditional particle filter material, the fiber filter material has a larger specific surface area, has a larger interface adsorption and can retain suspended solids, and has a good filtering effect.
Compared with organic fiber filters, ceramic fibers have good thermal stability, chemical stability and thermal shock resistance.
In recent years, some new technologies for purifying aluminum liquid at home and abroad have also been studied, such as vacuum dynamic processing, ultrasonic continuous degassing purification and corundum ceramic filters, which have received good results, but these process methods are more complicated and expensive, and it is difficult to promote A large number of people in the industry.
The metal filters and fiber cloth filters used by low-end customers can only remove the larger inclusions in the aluminum alloy melt, but cannot remove the inclusions below the micron level, and the metal filter can also contaminate the aluminum alloy.
The use of foam ceramic filter plates can filter out fine inclusions, and significantly improve the mechanical properties and appearance quality of the product.
No Comments