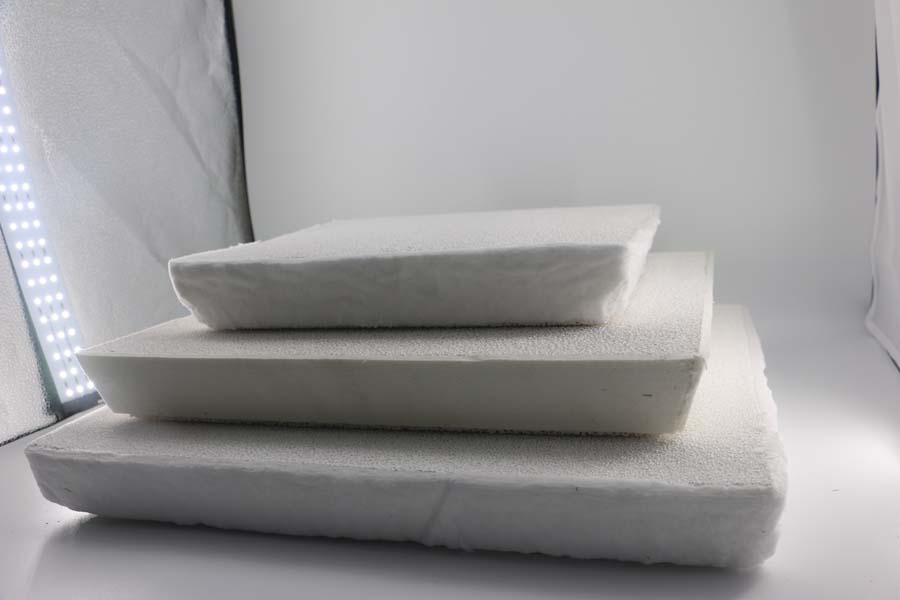
12 5月 5052 Aluminum Ceramic Filter Suppliers
5052 Aluminum Ceramic Filter Suppliers provides CFF for the filtration and purification of aluminum melting and casting plants. The foamed ceramic filter for casting has a multilayer network and multi-dimensional through holes, and the holes communicate with each other.
During the filtration process, molten aluminum carries inclusions and flows along tortuous channels and pores.
When it comes into contact with the foam frame of the filter plate, it directly intercepts, adsorbs, deposits, etc.
When the body flows in the hole, the filter plate channel is curved, the melt flowing through the channel changes the flow direction, and the inclusions collide with the hole wall and firmly adhere to the hole wall.
Inclusions and gases in the metal have a significant impact on the strength, fatigue resistance, corrosion resistance and stress corrosion cracking properties of the material.
Effectively controlling the oxidized inclusions in the cast rod melt and improving the quality of the cast rod are the common goals pursued by the aluminum industry.
At present, ceramic foam filter technology and purification methods are widely used to remove inclusions in aluminum alloy melts.
Some of the inclusions in aluminum alloy come directly from oxide inclusions. All inclusions before casting are called primary oxidation inclusions.
According to the size, it can be divided into two categories
1. The uneven distribution of large inclusions in the macrostructure makes the alloy structure discontinuous, reduces the compactness of the casting, and becomes the source of corrosion and cracks, thereby greatly reducing the strength and plasticity of the alloy.
2. The fine and dispersed inclusions cannot be completely removed after refining, which increases the viscosity of the melt and reduces the feeding capacity of the molten aluminum during solidification.
The secondary oxidation inclusions are mainly formed during the casting process. During the pouring process, liquid aluminum is in contact with air, and oxygen reacts with aluminum to form oxide inclusions.
During the smelting process, the aluminum alloy comes into contact with various components in the furnace gas to form compounds such as Al2O3. The Al2O3 in the molten aluminum will increase the hydrogen content in the aluminum alloy melt. Therefore, the content of Al2O3 in molten aluminum has a great influence on the formation of pores in aluminum castings.
5052 Aluminum Ceramic Filter Suppliers introduced like this
The ceramic foam filter for casting is installed in the filter box between the furnace and the distribution tank. The filter box is made of refractory material. It can experience multiple cooling and heating without cracking, high strength, and good thermal insulation performance.
The closer the filter box is to the manifold, the better, because this can shorten the flow distance of the filtered aluminum liquid and reduce or avoid the regeneration of oxides. The molten aluminum flows out of the furnace mouth, passes through the filter box, and then flows into the manifold through the washing tank. When the filter device is started, the drop before and after the melt filtration is about 50mm, but with the extension of the filtration time, the inclusions on the surface of the filter plate and the hole wall increase, and the drop in the filtration flow increases. At the end of casting, the drop increased to 60-120mm.
No Comments