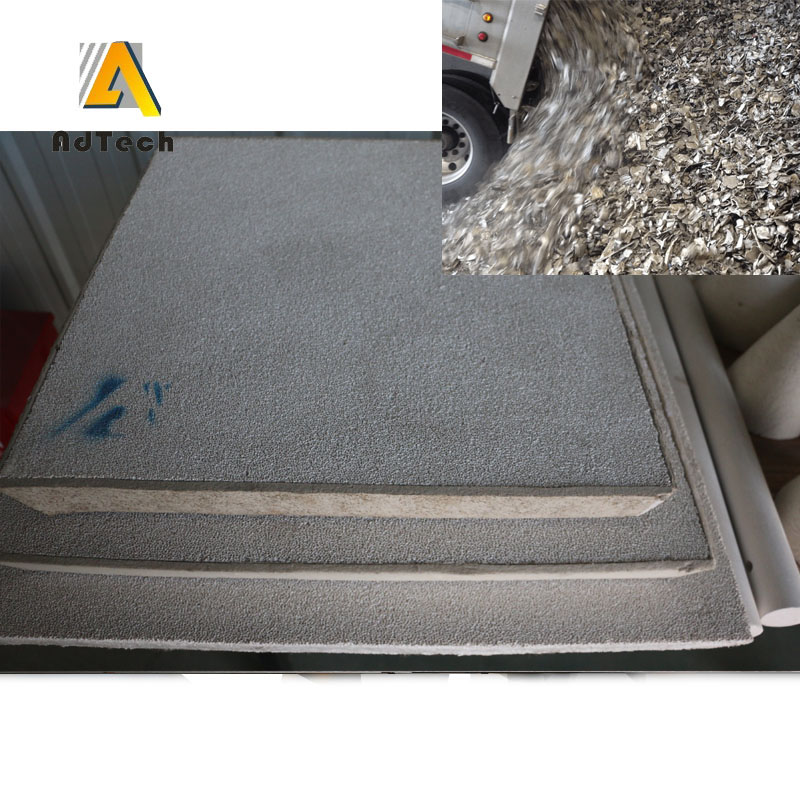
12 9月 What Is Ceramic Foam Filter
In the manufacture of castings, the proportion of defective castings associated with casting defects, such as non-metallic acquired impurities, usually accounts for 50% -60% of the total waste. Acquired impurities not only worsen the strong mechanical properties of the casting but also hurt its working properties and appearance.
Refining a casting molten alloy to reduce or eliminate various non-metallic acquired impurities is a very important technical tool for producing high-quality castings.
The task of cleaning a liquid alloy for casting can be effectively achieved through the use of filtering techniques.
The filtering technique has been used in the foundry industry for several decades.
Initially, only simple filters, such as a thin wire mesh, a porous steel plate, and a porous ceramic insert, were inserted into the casting system to filter out a large block of acquired impurities.
Although a porous sintered ceramic filter, first developed in the USA in the early 1970s, solved the problems of particles passing easily through it and inconvenient use, its porosity was low, usually less than 50%, and the rate of flow of liquid metal was low, as well as in a pressed ceramic cassette filter, developed for the first time in the USA in the early 1980s.
+
What Is a Ceramic Foam Filter?
The foamed ceramic filtration technique has evolved rapidly since the filter for aluminum foamed ceramic alloy was successfully developed for the first time in 1978.
Foam filters are commonly used filtration tools in the aluminum and nonferrous alloy smelting industries.
The ceramic foam filter is milky white and is made from high-purity alumina (AI2O3). It provides deep filtration to remove impurities from the molten aluminum. The porous shape of the filter provides multi-dimensional and deep filtration to remove impurities from the molten aluminum. It has excellent resistance to thermal shock and effectively removes impurities through continuous and thorough filtration. Al2O3 foam ceramic ceramic foam filter is suitable for filtration and purification of 1000C aluminum and alloy solutions.
Ceramic Foam Filter on the market mainly includes an alumina ceramic foam filter for filtering aluminum metal, a silicon carbide filter for filtering cast iron, and a zirconia filter for filtering molten steel.
Among them, an alumina filter and a silicon carbide filter cannot be used to filter molten steel, due to the insufficiently high temperature resistance and thermal shock resistance characteristics. A zirconia filter for filtering molten steel has a high manufacturing cost.
Why choose an Al2O3 foam ceramic foam filter to filter aluminum alloy liquid?
1 Advantages of ceramic foam filter:
Foam ceramics have the characteristics of uniform pores, high-temperature resistance, thermal shock resistance, wear resistance, and good chemical stability. They are widely used in casting processing, water treatment, chemical industry, environmental protection, and other industries. They are ideal aluminum liquid filters; catalyst carriers, and Good sound insulation and heat insulation materials. Product shape, size, and hole size can be designed and manufactured according to requirements.
2 There are many impurities in the aluminum melt:
During the smelting process, aluminum is exposed in the furnace in a molten or semi-molten state, and is easily oxidized, reacts with water vapor, and absorbs argon gas, forming various forms of non-metallic slag.
Lining debris, chloride carbides in the flux, and coarse metal particles constitute part of the waste materials of the furnace charge, bringing some non-aluminum impurities into the cycle.
Since the waste comes from waste from various processes in the factory and waste from outside the factory, it has different pathways, complex composition, and poor quality.
These impurities often cause bubbles and inclusions in the billet, seriously affecting the purity of the aluminum melt, and further affecting the machining performance, mechanical properties, corrosion resistance, and appearance quality of the product.
What is the function of an alumina ceramic filter plate?
The alumina foam ceramic filter plate can effectively remove various micron-level inclusions in the aluminum liquid.
It has unique mullite with good mechanical strength and chemical stability, and excellent resistance to erosion by aluminum liquid to obtain a stable filtration effect.
Foam ceramic filtration products effectively remove solid inclusions from metals, allowing high-quality aluminum to be forged.
From 1oppi coarse porosity to 4oppi ultra-fine porosity, it can be customized according to needs and circumstances.
Product inspection standards:
Our inspection has an experienced and skilled quality inspection team to ensure the best thanks to the considerable experience and professional knowledge accumulated in many years of quality control and improvement.
1. Light transmittance:
Light transmittance refers to the effective filtering area of the foam ceramic filter plate product.
The higher the transmittance, the fewer blind holes, the more effective filter holes (display holes), and the better the filtering effect.
2. Porosity:
Porosity refers to the percentage of the total volume of pores in the filter plate product to the total volume of the filter plate product. The porosity determines the throughput capacity of the foam ceramic foam filter per unit volume. The greater the porosity, the greater the filtration flow rate of the filter plate and the stronger the filtration capacity.
3. Uniform pores:
Porosity uniformity is used to describe the difference between the actual number of pores per 25.4mm length in the plate product and the theoretical required number of pores. The smaller the gap, the better the product quality.
If the pores are too large, the filter plate will reduce the impurity retention capacity and melt filtration speed. The size of the pore size uniformity mainly depends on the foam used in making the filter plate. The better the pore size uniformity of the foam, the better the pore uniformity of the filter plate.
4. It has certain high-temperature resistance, thermal shock resistance, and liquid metal erosion resistance. A refractory material containing carbon-based material can withstand temperatures greater than that of molten metal and prevent metal leakage; for this reason, such material has high strength and a better characteristic of thermal shock resistance at high temperatures.
Sorry, the comment form is closed at this time.