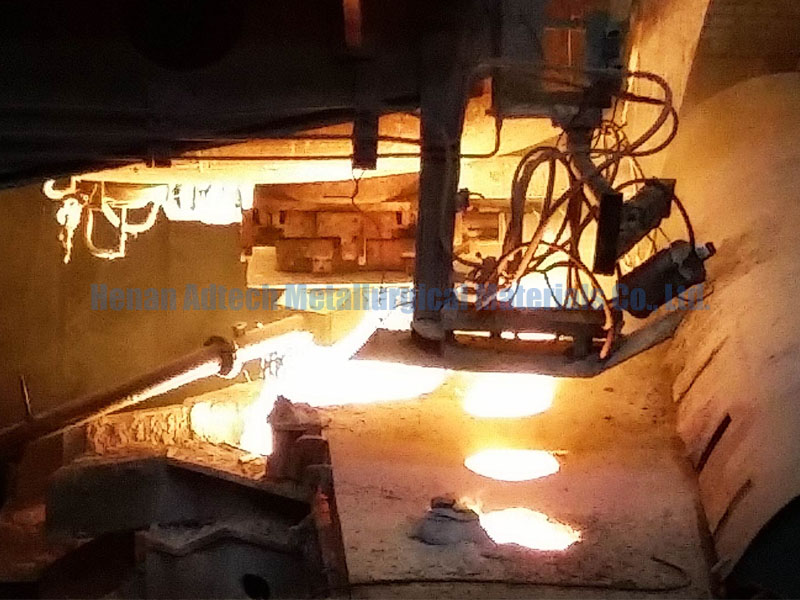
10 1月 Tundish Nozzle
Tundish Nozzle is a complex problem that causes decreased productivity, quality defects, and increased production cost.
The first step in a program aimed at the reduction of nozzle clogging is to implement a real time quantitative analysis that includes a nozzle clogging factor, rate of change of clogging, maximum possible casting speed, and defect or impending defect indicators.
A graphical operator interface with data archiving is a most effective tool.
The next step in the anti-clogging program is to identify die clog material through macroscopic, microscopic and chemical analysis, and then categorize the type of clogging, Remedial procedures must then be implemented using the real time clogging monitor as a measure of effectiveness.
Although the recommended practices will be somewhat site and grade specific, an attempt to summarize them is made in the following list of 20 items: 1. Reduce furnace slag carryover to the ladle;
2. Reduce oxygen potential of ladle slag to around 2 % FeO;
3. Increase ladle slag basicity to approach lime saturation;
4. Use lime concurrently with aluminum deoxidation;
5. Use a controlled rinse stir of several minutes as die last step in ladle refining;
6. Use ladle vibration intensity as the argon stirring control parameter;
7. Avoid slag carryover from ladle to tundish;
8. Use a basic, fluid tundish flux of sufficient thickness for complete coverage;
9. Open each new ladle with the shroud submerged;
10. Avoid surface turbulence and tundish slag entrainment;
11. Flood the tundish with argon at the start of a sequence;
12. Use low FeO nozzle sand and tundish flux;
13. Use minimal nozzle components, and good seals between components;
14. Ensure accurate nozzle component alignment;
15. Use argon injection through pores or channels in the nozzle refractories;
16. Monitor argon back pressure and flow in each input location;
17. Check SENs for signs of chemical reduction of impurities by carbon;
18. Use the correct range of calcium injection for inclusion modification;
19. Add sulfur on resulfurized grades only after calcium treatment and rinse stir;
20. Maintain sufficient oxygen potential to avoid Mg-aluminate spinel formation.
No Comments