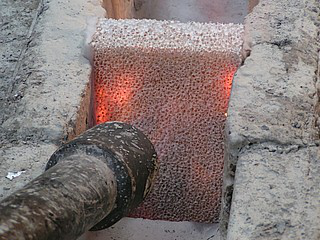
03 4月 Specifics of Aluminium Alloys Filtration
Specifics of Aluminium Alloys Filtration
Filtration of aluminium can be broken down into several parts, depending on the type of the applied technology of cast production or on the method of liquid metal preparation.
Primary and secondary aluminium manufacture
Manufacture of aluminium alloys meets the requirements for higher purity of the cast metal in order to increase quality of the manufactured intermediate for the final production (foils, blocks, ingots, rods, sections, …). The filtration thus contributes by the lower reject rate of manufacture of the final product and by its higher quality.
Metal casting takes place in these sites by continuous or discontinuous campaigns of the order of some tons up to some hundreds of tons and therefore the large-area filters are used for filtration; they are placed in the liquid metal distribution system. We recommend to place the filters seated in the ceramic filtration boxes utilizing horizontal or vertical filter layout.
The filters ADTECH adapted for long-time temperature load, can be used for filtration. The filters are usually used in the standardized dimensions shown in inches with the porosity from 10 to 60 ppi (pores per linear inch). The filter size depends on its porosity and is selected with respect to the filtration capacity, time of casting and layout solution of the filtration box. Selection of filter porosity is determined by the specific alloy, temperature of casting, metal pollution and requested output quality.
Prior to casting itself, the filter has to be preheated adequately to secure its correct functioning. After completion of the campaign the filter can be reused, if the filtration box is equipped by permanent heating. If the metal sets up in the filter, it has to be replaced for the next casting campaign.
Filtration in foundries
Pollution of the molten metal by hard oxides, causing problems with cast finishing, is the main reason for introduction of cast filtration in the foundries. Elimination of undesirable defects, e.g. cast untightness, porosity (blowholes), low homogeneity, etc., often occurring only during the casting itself, under the impact of liquid metal turbulence in the mould, is the second main reason for filtration.
There is a number of different types of foundries which can be briefly broken down by the technology of casting into:
- Die / pressure casting
high-pressure casting
low-pressure casting - Gravity casting
chill casting
sand casting
ceramic mould casting
The die and chill foundries are not always able to incorporate the filter into the gating system of the mould, where filtration is most effective and therefore different solutions of application of the filtration in the technological steps, preceding the process of mould filling by metal, are searched for.
Insulating filtration sprue cup
During the process of molten metal pouring a simple system of the insulation sprue cup with filter can be used; the filter is specified for single filtration of ca 100 – 500 kg of the molten metal. The sprue cup should be provided with the sprue pin, calming metal filling into the holding furnace and preventing creation of further inclusions as the consequence of metal turbulence. Whilst the filter is intended for a single use only, the sprue cup can be reused for some tens of pouring campaigns. We offer two sprue cup types for 3“ and 5“ filters.
Filtration boxes
Use of the filtration box with electric or gas heating is recommended for larger metal volumes. The foundry filter ADTech provided with the bevel and expansion paste-over, is inserted inside the box. Capacity of such filters reaches some tens of tons and is used in the process of metal pouring from the melting furnace into the transfer ladles or into the holding furnaces. Nowadays we offer two solutions for 9“ and 12“ filters. Capacity of each filter is some tens of tons. Their replacement is usually carried out once a week.
Filtration partitions in holding furnaces
The filtration partition in the holding furnace is usually the most effective method of introduction of the filtration in the die foundries. The filter is inserted into the chamber holding furnaces in the form of a partition separating the extraction point from the polluted metal. In case of the crucible furnaces the filtering partition is of U-section. The optimally chosen filter is able to filter some hundreds of tons of the molten metal during its service life. Its replacement is carried out during regular maintenance of the refractory furnace lining. For this very purpose the filters ADTECH of special dimensions and shapes adapted to furnace sizes are used.
Ashraful Ameen
Posted at 14:43h, 17 5月Dear Sir
We Aquila Shipping & Trading Limited is Hong Kong Registered company and based in Hong Kong.
We are in a position to supply Good Quality Aluminium Scrap CFR delivery terms up to Malaysia.
Please contact us by email: aquilashippinghk@yahoo.com or Mob/WhatsApp: +852 5335 2585
Appreciate to receive your kind response.
Best Regards
Ashraful Ameen