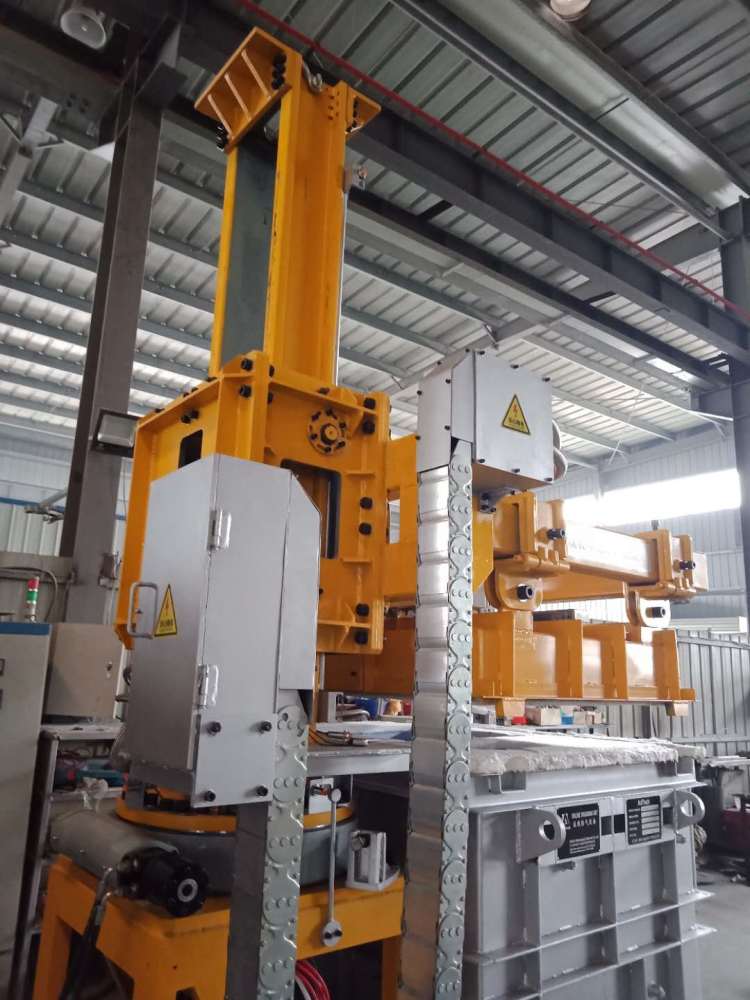
14 11月 Rotary Degassing And Fluxing Unit For Aluminum Alloys
Rotary Degassing And Fluxing Unit For Aluminum Alloys
Rotary Degassing And Fluxing Unit For Aluminum Alloys uses a three-dimensional network structure and an organic bubble connected to the pores as a carrier, invading it into the thixotropic alumina material slurry, and using a square-corrected center-distance automatic extrusion process to make the slurry It is uniformly applied to the foam skeleton of the carrier, and is baked and solidified at a high temperature for firing. It is installed in the filter box for the impurity filtration of aluminum alloy liquid, and it can meet the high-value-added and high-tech aluminum alloy precision casting of aviation and transportation. Such as: computer hard disk, PS board base for printing, cans, jet turbine engine fan blades and other products.
Rotary Degassing And Fluxing Unit For Aluminum Alloys adopts a variety of high temperature resistant chemical materials and is refined by a special process. It has the advantages of high strength, high temperature resistance and uniform mesh. It is suitable for filtration and purification of various metal liquids, and can remove inclusions in castings. Porosity, refinement of grains, improvement of casting pass rate and mechanical properties, improvement of casting quality and cost reduction, with significant technical and economic value, and can be customized according to user requirements.
Rotary Degassing And Fluxing Unit For Aluminum Alloys Technical field
The utility model relates to an aluminum water impurity removing filtering device, in particular to an aluminum liquid filtering device which is simple in structure, convenient in maintenance, convenient in operation, good in purifying effect of aluminum liquid and high in yield.
Rotary Degassing And Fluxing Unit For Aluminum Alloys Background technique
At present, the existing aluminum water decontamination filter box production line, in the remelting aluminum ingot smelting process, mostly adopts a filter box directly from the melting furnace through the launder to the casting package, or in the launder between the casting packages.
In the casting process, the aluminum liquid must be completely discharged due to temporary parking, otherwise the filter plate will be scrapped due to the solidification of the aluminum liquid on the filter plate in the filter box.
A new filter plate must be replaced when starting the casting again, resulting in wasted work time and increased production costs.
By providing a filter dam plate in the filter device to protect the filter plate, and at the same time, according to the buoyancy principle in physics, the technology is used together with the aluminum liquid purification device applied by our company. The final purification of the aluminum liquid is achieved by a combination of two sets of devices.
Rotary Degassing And Fluxing Unit For Aluminum Alloys Advantages
It has extremely excellent corrosion resistance (except hydrofluoric acid) for all corrosive liquids, and has good heat resistance and no deformation.
The pores are evenly distributed and the interstitial rate is high, which can be customized according to requirements. The mechanical strength is high, and it does not cause the change of the open pores and the deformation of the micropores under the action of the fluid pressure.
It has numerous micropores with uniform network state distribution, and the aperture is slender and curved, with good penetrability and capillary characteristics. The solid particles form an arch bridge in the micropore diameter, which has little effect on the filtration rate and will not block under normal pressure. Micropores.
It adopts the principle of adsorption to filter, which can effectively remove large inclusions in aluminum liquid and effectively adsorb fine inclusions of small size; it has good thermal shock resistance and improves corrosion resistance to molten metal.
No Comments