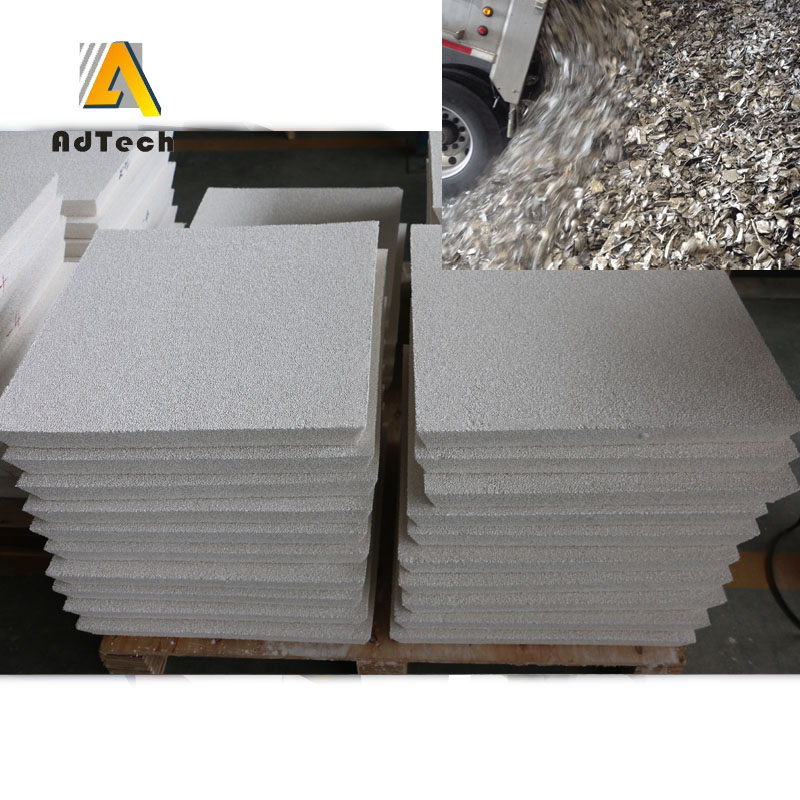
03 9月 Reticulated ceramic foam filters
Reticulated ceramic foam filters
Reticulated ceramic foam filters used in aluminum oxide granular material should seem an obvious choice to any person skilled in the art of refractory materials used to contain molten aluminum and its alloys.
Alumina is relatively chemically inert in molten aluminum and its common alloys, including alloys containing magnesium.
Reticulated ceramic foam filters is also widely used as a granular material in refractories used in furnaces, both for melting and for containing molten aluminum alloys.
In addition, before the advent of disposable replaceable ceramic foam filters for filtering molten aluminum, filters with lamellar alumina filler were used. Filters with a filler are large heated vessels containing unbound grains of lamellar alumina, used for repeated castings for several days or even weeks. The long exposure time of molten metal with unbound aggregated materials, such as in ceramic foam filter with fillers and refractories, requires the use of a chemically inert granular material such as aluminum oxide.
However, alumina has a relatively high coefficient of linear thermal expansion (8.0 × 10-6 / ° C), and monolithic forms of alumina, such as ceramic foam filters, have low heat resistance due to high thermal stresses created by a combination of thermal gradients in the result of uneven heating and a high coefficient of thermal expansion.
In the process of preheating and initial contact with molten metal, the Reticulated ceramic foam filters material may crack or crack, as a result of which the filter material enters the ingot or billet, where it becomes an inclusion.
In addition, when the alumina-based foam ceramic filter is held in the filter bowl during preheating and use, high transverse compressive stresses can be generated as a result of the high coefficient of thermal expansion of the filter, resulting in destruction of the filter during compression.
Below are the requirements for the ideal material for a ceramic foam filter.
1. High temperature resistance – the material should not crack or crack during pre-heating or contact with molten metal. The material should have a low thermal expansion to minimize lateral compression stresses while in the filter bowl.
2. Corrosion resistance – the filter material should not have significant chemical activity in the intended range of application (time, temperature, alloy content) and should not be wetted by molten aluminum and its conventional alloys.
3. Appropriate bending and compressive strength.
4. Profitability in manufacturing.
5. The filter material after use should be safe for handling and disposal.
6. Low density or light weight, facilitating the work of the pouring span operator.
Sorry, the comment form is closed at this time.