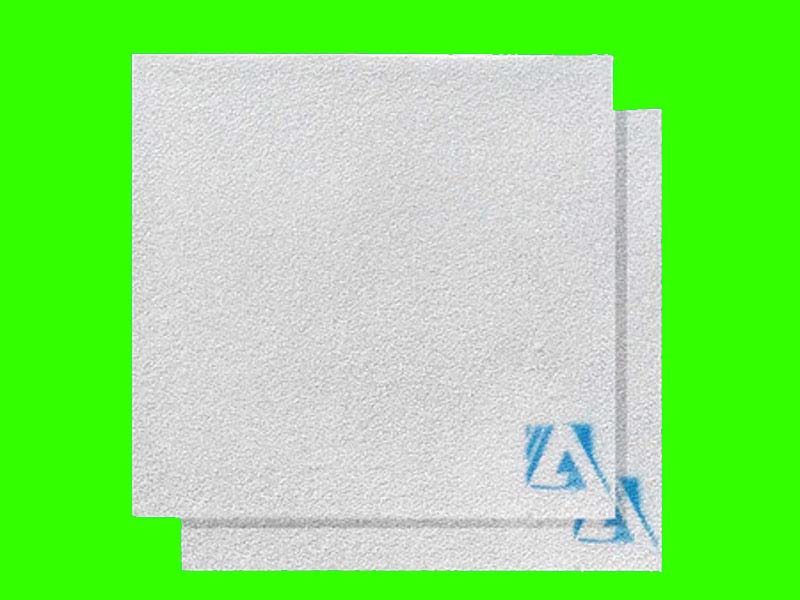
23 1月 Molten Metal Filtering
Molten Metal Filtering is a filter medium made of porous ceramic material not readily wetted with the molten metal is arranged, a lag occurs between the time the molten metal reaches the upper side of the filter medium and the time the molten metal begins to pass the filter medium and a head greater than the head of the molten metal during the filtration is required.
A filtration process to remove entrained solids therefrom. The liquid is completed by passing the solid-laden liquid through a porous filter medium that does not pass through the solid. Usually filtering molten metal, especially molten aluminum, will cause special problems because the liquid is highly corrosive and it is difficult to find a medium that the filter can withstand.
Generally, two filtration methods are used to remove entrained solids from molten aluminum alloys before casting.
The most common filter medium is an open woven glass cloth screen that is placed in a metal transfer tank, near the nozzle or even in the molten metal pool on top of the solidified ingot.
These filters can only remove large-sized inclusions from the metal, and are easily broken during use, because the glass fibers become very weak at the temperature of molten aluminum.
In another prior art procedure, molten aluminum is filtered through a bed of loose alumina particles (such as plate alumina), but it often suffers from the disadvantages usually associated with bed filters, namely that it passes too much solid , It is easy to form a channel, which hinders effective use, and a filter with a large pore size is not easy to control, but the conditions of use are so easy to change, even when initially the appropriate size, it cannot be effectively maintained.
In addition, when the filter is not used, the metal must be kept in a constant molten state.
Therefore, the main object of the present invention is to provide an improved molten metal filter.
Molten Metal Filtering is made of an open-cell hydrophilic flexible foam material with a plurality of interconnected voids surrounded by a mesh of the flexible foam material.
Typical materials that can be used include polymer foams, such as polyurethane foams, and cellulose foams.
Generally, any combustible organic plastic foam that has elasticity and the ability to restore its original shape can be used.
The foam must be burned or volatilized below the firing temperature of the ceramic material used.
Likewise, a foam material with 5 to 100 pores per inch should be used to provide the necessary filtering surface.
Of course, the size of the foam material can vary according to the desired end size.
The resultant product is a molten ceramic foam with an open-cell structure, which is characterized in that a plurality of interconnected voids are surrounded by the ceramic net, wherein the density of the ceramic foam material is less than 30% of the theoretical density of the ceramic material. The same size.
Naturally, the ceramic foam can have any desired configuration based on the configuration required for a particular molten metal filtration process.
The molten aluminum launder between the molds transfers molten aluminum. The hollow cylindrical structure is preferable for filtering the molten aluminum through the downpipe. In either case, the height of the filter medium must exceed the height of the molten metal to be filtered.
Sorry, the comment form is closed at this time.