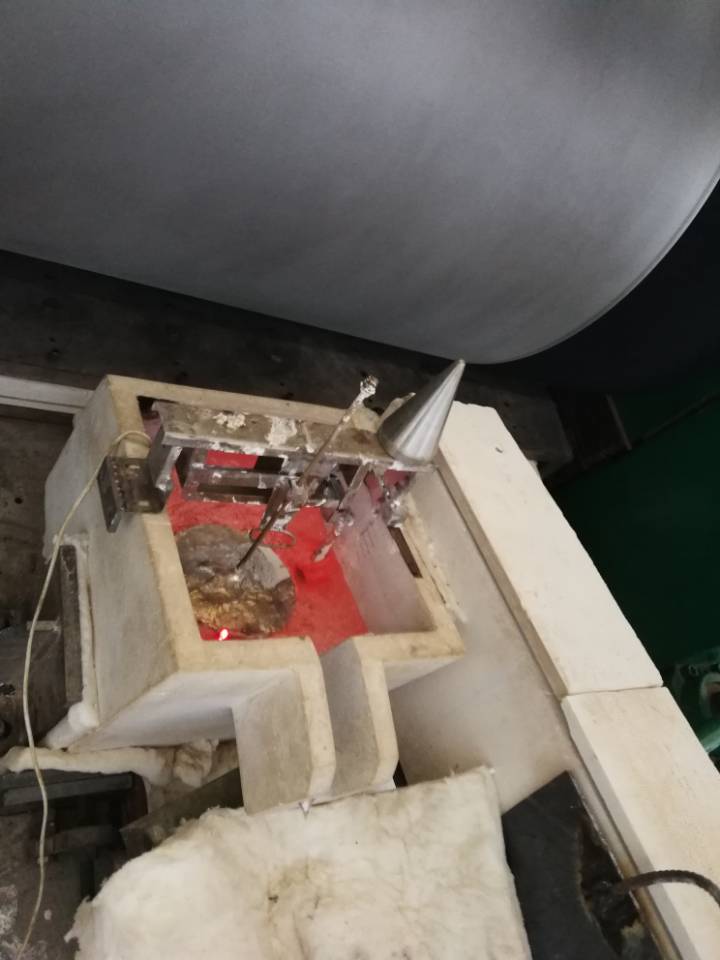
15 10月 High Aluminum Casting Nozzle
High Aluminum Casting Nozzle
In the process of aluminum alloy casting and rolling, the High Aluminum Casting Nozzle made of refractory material is indispensable, the adjustment of the opening degree of the casting nozzle, the adjustment of the plate type, and the important reuse in the production of aluminum products, therefore, the product quality is extremely Great impact. In the related art, the casting nozzle includes an upper clamping plate located at an upper portion of the casting nozzle, and a lower clamping plate located at a lower portion of the casting nozzle, and the upper clamping plate and the lower clamping plate are clamped by the threaded connecting member to be reasonably performed.
High Aluminum Casting Nozzle includes opposite upper and lower pressing plates, and a plurality of diverting blocks are disposed between the upper pressing plate and the lower pressing plate. When it is necessary to adjust the opening degree, it is necessary to tighten or loosen the threaded connecting piece.
Since the upper clamping plate and the lower clamping plate are each of an integral structure, the following disadvantages exist:
1. The asymmetric plate type cannot be adjusted by the opening degree.
2. The nozzle opening The degree cannot be adjusted differently in different regions.
3. The opening degree of the nozzle cannot be adjusted online. Therefore, the straightness of the casting nozzle is required to be high. the technical requirements of the vertical board vertical board are high, and it is difficult for the casting and rolling area.
Therefore, it is necessary to choose a powerful nozzle manufacturer, and we are one of the first choices.
The influence of AdTech High Aluminum Casting Nozzle on the casting speed, the height of the cavity of the High Aluminum Casting Nozzle, and the total length of the cavity, and the numerical simulation results of the variable density and the constant density melt were compared, revealing the high-temperature shallow-thin melt flow. The distribution law of field and temperature field shows that the numerical simulation should adopt three-dimensional model.
The two-dimensional model is unreasonable and does not conform to the reality. The melt flow velocity and outlet temperature increase with the increase of casting speed, and the change of inlet velocity distribution can be improved.
Uniformity of temperature and velocity of the cavity melt outlet; changing the number of splitting blocks can improve the outlet velocity distribution and temperature distribution uniformity.
Appropriately reducing the cavity opening degree can obtain a more uniform outlet velocity distribution and temperature distribution. Increasing the cavity length energy Obtain a more uniform melt exit velocity distribution and a more uniform temperature distribution; in the practical application of the project, the apparent density is the rationality of the constant density, and the numerical simulation results and analysis conclusions provide the best matching parameters for continuous casting and rolling, especially rapid casting and rolling. An important basis.
Combining the experimental results, the experimental results of the surface temperature of the casting nozzle were carried out, and the relevant data were collected. The results show that the numerical simulation conclusion is consistent with the experimental test data conclusion. The temperature test experiment establishes the basis for the simulated temperature boundary conditions, thus verifying The correctness of the relevant conclusions.
On the basis of the simulation calculation of the convection field and the temperature field, the high aluminum casting nozzle cancels the fixed diversion block of the existing nozzle cavity, and sets a row of positionally controllable gate blocks in the front box close to the casting nozzle. The invention realizes a cloth flow control device for synergistically regulating the flow field of the aluminum melt, the temperature field, the concentration field of the solute (alloy element) and the quality of the strip, and creates favorable conditions for improving the quality of the cast strip. The utility model has the advantages of simple equipment, convenient operation, strong function, safety and reliability, and is suitable for industrial production and the like.
No Comments