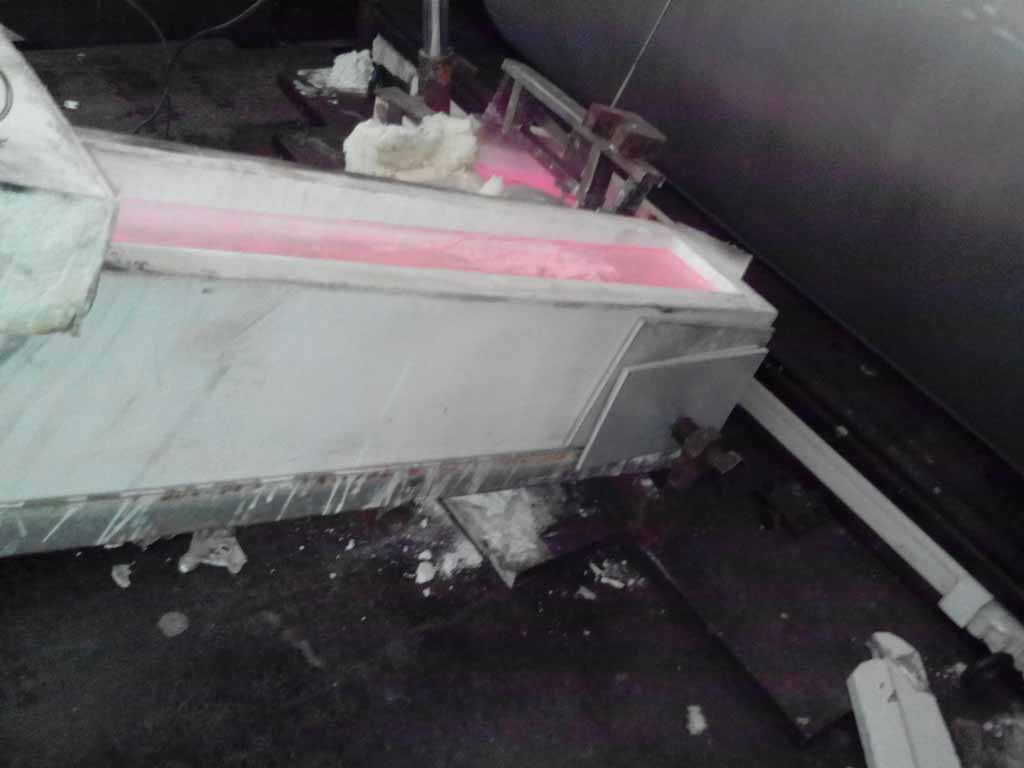
07 5月 Foundry Feed Nozzle Cavity
Foundry Feed Nozzle Cavity is a key component of the aluminum strip casting and rolling mill, and its quality directly affects the thickness, quality and yield of the strip.
Foundry Feed Nozzle Cavity has other names in practical applications, such as Castertip, Tip Cavity, Nozzle Cavity, Caster Tip, Casting Tip, Casting Nozzle, Caster Nozzle, Feed Tip, Feeding Tip.
Installation steps of Foundry Feed Nozzle Cavity
1. Preparation of casting nozzle plate
1. The casting nozzle plate includes the upper and lower plates, side plates and the middle dividing plate. The shape, size and position of the middle dividing plate have been arranged.
2. The casting nozzle plate makes the liquid metal evenly distributed along the width direction of the casting nozzle plate, flowing at a constant speed, and the temperature change does not exceed ±2℃.
3. The inner cavity of the casting nozzle plate and the shunt plate are all specially treated with boron nitride, which can effectively protect the melting of high-temperature aluminum liquid, increase abrasion resistance, make the casting nozzle plate achieve high performance, and effectively prevent the aluminum plate from being caused by silicon and aluminum. Reflect the appearance of black spots and underworlds, and increase the smoothness of the surface of the aluminum plate.
4. The front box and the casting nozzle plate assembly are pre-dried for two hours in a drying oven at about 200°C, and stored in the drying box at about 110°C.
Feed Nozzle Cavity position adjustment
1. The casting nozzle plate is installed on the steel structure casting nozzle plate fixture, and the casting nozzle plate fixture is fixed on the casting nozzle plate platform.
2. After the casting nozzle plate is assembled and preheated and before it is assembled in the casting and rolling mill, all preparations should be made, and the casting nozzle plate should be installed at the fastest speed to avoid heat loss and inhalation of moisture.
The preparation of the casting-rolling production line should be properly completed before the casting nozzle plate assembly is taken out of the drying box.
3. When the casting nozzle plate assembly suspension arm is hoisted from the bracket and placed on the casting nozzle plate platform, the operation must be small
Do not damage the casting nozzle plate, the roll cannot rotate at this time.
4. After the casting nozzle plate is placed on the platform, tighten the fixing screws. No debris is allowed on the casting nozzle plate platform, casting nozzle plate fixture and the outer surface of the casting nozzle plate, otherwise the position of the casting nozzle plate will be inaccurate. Therefore, before the casting nozzle plate is fixed on the platform, it should be thoroughly cleaned.
5. The table is driven by an oil cylinder
Large stroke advance and retreat; confirm that the top plate of the spiral elevator adjusted in the horizontal direction of the casting nozzle plate platform is at the maximum stroke position, and the oil cylinder drives the casting nozzle plate to move quickly to the rolling mill. When the front end of the casting nozzle plate and the roll center line are 120mm, the nozzle platform The baffle is pressed against the top plate of the screw jack. Start the servo motor to adjust the position of the casting nozzle plate slightly. Driven by a servo motor, it can be adjusted left and right in the horizontal direction and up and down in the vertical direction. Both sides can be adjusted at the same time, or it can be fine-tuned on one side.
Extend the casting nozzle plate into the roll gap, while one person monitors with a flashlight. The position of the casting nozzle plate is not allowed to be set by visual inspection only.
Extend the casting nozzle plate into the roll gap as close as possible to the surface of the roll, but not contact with the roll, raise or lower the casting nozzle plate platform according to the center position of the roll gap, so that the upper and lower nozzle fans on the casting nozzle plate are arranged symmetrically on the center line of the roll gap.
The distance between the exit end of the casting nozzle plate and the surface of the roll is about 0.5-0.8mm.
Then, at the exit end of the rolling mill, measure the distance between the nozzle plate and the tangent position of the two rolls on both sides with a ruler. If the dimensions of the two sides are different, adjust the position of the nozzle plate on one side to make the distance between the two sides the same.
After the workers are proficient in various positions, several positions can be exchanged for erecting the slab, and the roller cleaning staff and the slag runner staff can assist in the installation and adjustment of the above casting nozzle plate.
No Comments