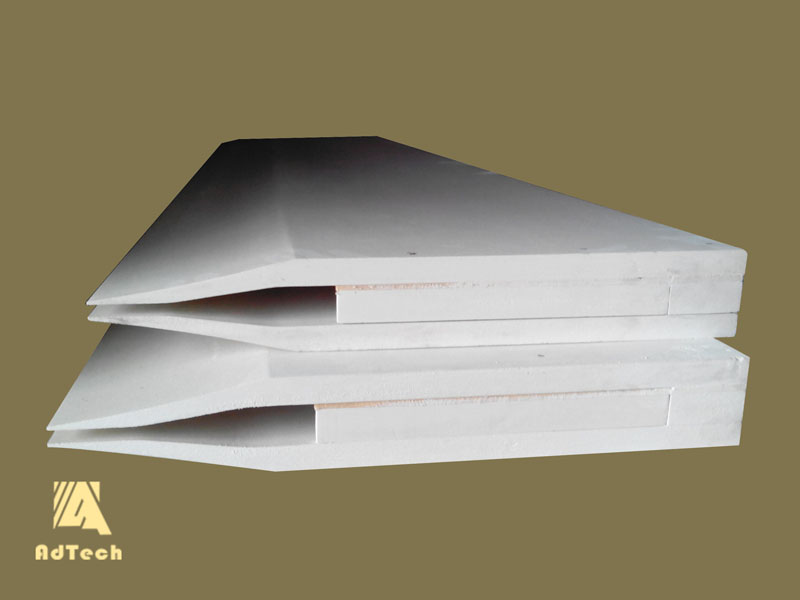
07 5月 Foundry Feed Casting Nozzle
Foundry Feed Casting Nozzle is calcined at high temperature, does not contain organic matter, and has zero shrinkage at 800°C. It can be used in various double-roll continuous casting mills.
The distribution of the flow field and temperature field in the Feed Casting Nozzle cavity directly affects the shape of the plate, especially the exit velocity of the high-temperature shallow aluminum melt in the Feed Casting Nozzle cavity and the uniformity of the exit temperature distribution determine whether the casting and rolling process can proceed smoothly. And whether high-quality cast slabs can be obtained.
The surface of the aluminum silicate casting nozzle material is specially treated with aluminum titanate coating. Its special process can effectively prevent the aluminum liquid from eroding the Feed Casting Nozzle and avoid carbonization; the fracture structure is a fine and uniform layered fiber structure to prevent flakes The existence of flocculent structure; the working surface coating is uniform and smooth, preventing the occurrence of granular cracks and coating shedding, and providing protection for high-quality cast-rolled plates. We can produce Feed Casting Nozzle of various models and supply methods according to customer requirements.
In the process of aluminum alloy casting and rolling, the nozzle made of refractory materials is indispensable. The adjustment of the opening degree of the nozzle and the adjustment of the plate shape are important and reused in the production of aluminum products.
Casting nozzle includes an upper pressing plate and a lower pressing plate arranged oppositely, and a plurality of shunt blocks are arranged between the upper pressing plate and the lower pressing plate. When you need to adjust the opening degree, you need to tighten or loosen the threaded connection.
Since the upper splint and the lower splint are each an integrated structure, there are the following shortcomings
1. It is impossible to adjust the asymmetric plate shape by the opening degree.
2. The opening degree of the casting nozzle cannot be adjusted differently in different regions.
3. The opening degree of the casting nozzle cannot be adjusted online. Therefore, the straightness of the nozzle is required to be higher
4. It has high requirements for vertical board skills, and it is difficult for the casting and rolling area.
Adtech (www.adtechamm.com), the manufacturer of Foundry Feed Casting Nozzle, studies the effects of casting speed, Feed Casting Nozzle cavity exit height, and total cavity length.
The numerical simulation results of variable density and constant density melts are compared, and the flow field and temperature field distribution of high-temperature shallow aluminum melt are revealed.
The melt flow direction and outlet temperature increase with the increase of the casting speed. Changing the inlet velocity distribution can improve the uniformity of the melt outlet temperature and velocity in the cavity.
Changing the number of shunt blocks can improve the outlet velocity distribution and temperature distribution uniformity.
Appropriately reducing the opening degree of the cavity can obtain a more uniform outlet velocity distribution and temperature distribution.
Increasing the length of the cavity can obtain a more uniform melt outlet velocity distribution and a more uniform temperature distribution.
In practical engineering applications, it is reasonable to regard the variable density as the constant density, and the numerical simulation results and analysis conclusions provide an important basis for the best matching parameters of continuous casting and rolling, especially rapid casting and rolling.
No Comments