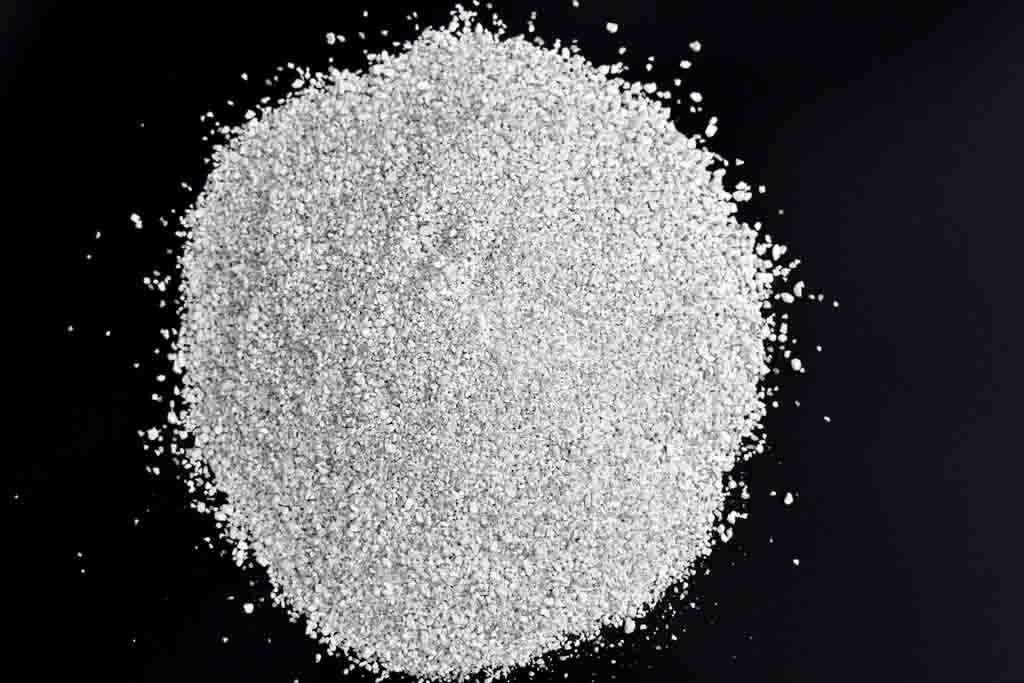
25 3月 Fluoride Free Granulated Cleaning Flux
Fluoride Free Granulated Cleaning Flux is generally composed of chlorides and fluorides of alkali metals and alkaline earth metals.
In addition to the flux produced by using refined flux, it is best to adjust the flux composition ratio according to the composition of the smelted aluminum alloy.
At the same time, strictly control the refining process conditions, such as the amount of aluminum flux and melt flux, contact time, contact area, stirring conditions, temperature, etc.
The use of refining agent can effectively reduce the aluminum content in the slag and reduce the loss of castings.
In the smelting process of aluminum and aluminum alloys, in addition to its own inclusions, aluminum and oxygen can easily form aluminum liquid on the surface of the scum layer caused by aluminum oxide or sub-alumina. It has a certain degree of wettability and aluminum melting, slag There is a large amount of melting, which requires a Granulated Cleaning Flux to change the wettability of the two, increase the surface tension at the interface between the slag and aluminum, and separate the slag and aluminum.
The general refining method is to manually sprinkle Fluoride Free Granulated Cleaning Flux into the furnace, and then stir and refine.
1. For the production of some alloys, nitrogen blowing (about 30 minutes) is needed to drive the aluminum liquid to fluctuate greatly, so it is best to adjust the nitrogen pressure and control the blowing height at 10-15mm.
2. Effectively dispose of aluminum slag generated in the casting process.
3. Aluminum slag is an inevitable part of the melting and casting process. Despite relevant measures, a certain percentage of metallic aluminum will be eliminated.
4. Therefore, smelters need effective treatment of aluminum slag.
5. The simplest and most economical method is to use a grinder to repeatedly grind the aluminum slag, and then screen, so as to effectively recover part of the aluminum beans.
6. Reduce the slag slope of the mixed furnace and fully remove the aluminum slag from the furnace.
7. The size of the mixed slag slope directly affects the amount of aluminum slag.
8. If the slope is too large, most of the slag will not be picked out, resulting in a large amount of aluminum slag and aluminum deposits, and the slag and aluminum deposits cannot be recovered in time when cleaning in the furnace.
9. On the premise of ensuring the capacity of the mixing furnace, try to reduce the slope of the slag slope.
10. Strictly control the quality of slag to prevent molten aluminum from flowing out.
Mucking off after refining
1. The existing slag scraping operation basically uses a large rake to scrape the aluminum slag out of the furnace door.
2. Except for careful operation by personnel during the operation, try not to take out the molten aluminum.
3. At the same time, the design of the large rake also needs to be cautious. It is recommended to make a few rows of small round holes on the surface of the large rake to allow the molten aluminum in the aluminum slag to flow into the furnace, otherwise the excessive molten aluminum will be taken out and returned to the furnace after being taken out. damage.
4. Reduce the amount of bad aluminum and bulk aluminum.
In the production process, strictly follow the process requirements to ensure that one furnace is produced and one furnace is qualified.
Especially in the production of general aluminum materials, try to avoid aluminum materials with flashes, burrs, corrugations, and inconsistent weights.
At the same time, before the end of production, push the molten aluminum in the launder into the mold as much as possible to form a qualified product and reduce the amount of bulk aluminum.
Effectively dispose of bad aluminum that has been produced.
For inferior aluminum, bulk aluminum, aluminum slag, aluminum beans, etc. due to various reasons, the appropriate heating furnace sequence should be added to the mixing furnace.
When necessary, waste can be recycled first to avoid unnecessary incineration.
in conclusion
Through the above analysis, although casting loss is inevitable in the casting process.
While using Fluoride Free Granulated Cleaning Flux, controlling the temperature of the molten aluminum, reducing the strength of the connection between the molten aluminum and the air, controlling the aluminum content of aluminum ash, aluminum and reducing the number of defects will have a significant impact and effectively reduce The melting of aluminum is lost during the casting process. It will bring considerable economic benefits to the enterprise.
No Comments