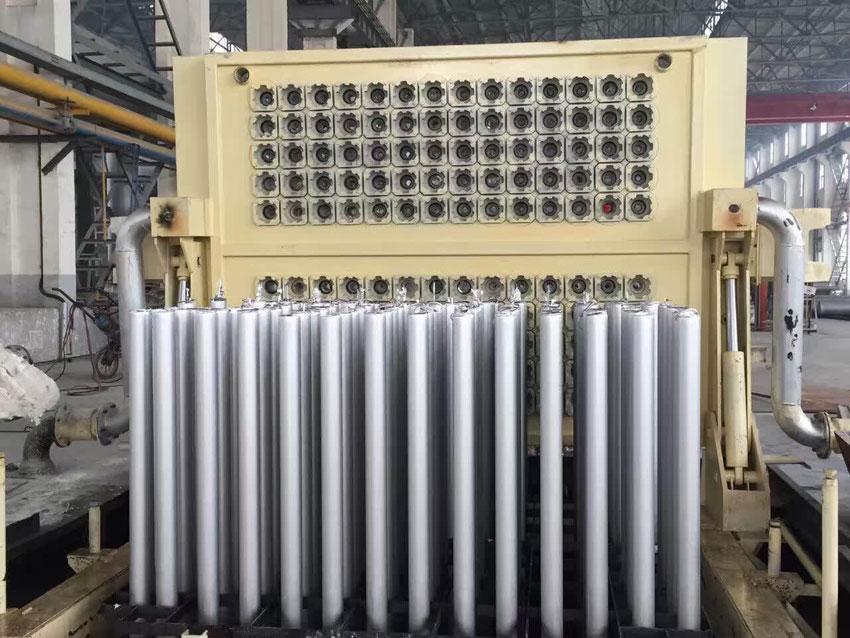
28 5月 Denmark Aluminium
Denmark Aluminium introduces related equipment related to the aluminum casting industry.
The casting nozzle is one of the most critical parts of the double-roll continuous casting and rolling of aluminum strip, through which the aluminum or aluminum alloy melt is input into the casting roll gap. The casting nozzle is also called the feed nozzle, and its quality directly affects the quality and output of the strip, so the structure and material requirements of the casting nozzle are very high. The nozzles are divided into wide and narrow types, and some of them are larger than 2100mm as extra wide. The structure of the casting nozzle plays a key role in stabilizing the process and improving the quality of the product. In terms of structure, it should be ensured that the flow line of the melt is reasonable and there is no dead zone; the melt is evenly distributed over the entire length of the roll gap; the temperature of the fluid flowing into the roll gap should also be uniform. The casting nozzle is composed of several workpieces, and there is a block of a specific shape between the two upper and lower aligned pieces to ensure that the melt can be evenly distributed in the entire casting nozzle.
Aluminum and aluminum alloy ingots must be pre-heated to a certain temperature before extrusion. In China, natural gas is still used for heating, and a few use oil heating, and almost all industrialized countries use electric induction furnaces. Most of the extrusion production lines ≥45MN in the world are heated by electric induction furnaces, and only a few are heated by fuel oil. Because the operating rate of large extruders is often around 70%, and some are even lower, of course, there are also 85%. It takes a long time to heat with natural gas, and it will take a long time to start the machine once it is shut down, and it will consume more oil. Heating by induction is very flexible. At the same time, due to the increasing requirements for product quality, the original heating method can no longer meet the requirements. If isothermal extrusion is required, the ingot must be heated in a gradient. The gradient heating methods include:
Denmark Aluminium introduces related equipment related to the aluminum casting industry.
Permanent magnet heating
Permanent magnet heating is a more advanced heating method. It was invented by Finnish nuclear physicist P. Suonninen and patented in 2011. Shanghai Ruiman Energy Technology Co., Ltd. obtained the exclusive right to operate in the Chinese market in 2012.
Its basic principle is that the aluminum ingot is located between two high-speed rotating high-performance permanent magnets, and the alternating magnetic field generated induces eddy currents in the ingot to be heated. The ingot gradually enters the high-speed rotating magnetic field, and the front end temperature is high. , The back end temperature is low, so as to achieve gradient heating. The advantage of this method is that it does not emit pollutants, consumes paper, and is more than 40% more efficient than traditional induction heating.
Single billet hot shear heating
This method was developed by Langdun Aluminum Processing Equipment Co., Ltd., Foshan City, China. It has low energy consumption and natural gas consumption is 20m3/t aluminum ~ 24m3/t aluminum.
It can achieve a gradient such as heat. German automation components are used to control the heating intensity. The front is high and the back is low, so that the temperature of the front end is higher than that of the back end, forming a temperature gradient of 20℃-50℃.
Electric induction gradient heating
The basic principle of electric induction gradient heating is similar to the principle of electric induction heating, but the induction heating is divided into several sections. The voltage V front> V middle> V, the ingot advances from back to front in order, because the front voltage is higher than the back , So the front end temperature is higher than the rear end, thus forming a temperature gradient. This heating method is often used for reverse extrusion ingots.
Friction-free induction heating
This heating method is considered to be the leading one at present. The extrusion temperature is always kept within the set range, which can ensure the uniform quality of the extruded material before and after, and completely eliminate defects such as tearing. At the same time, during the entire extrusion process, each All process parameters are under automatic control.
No Comments