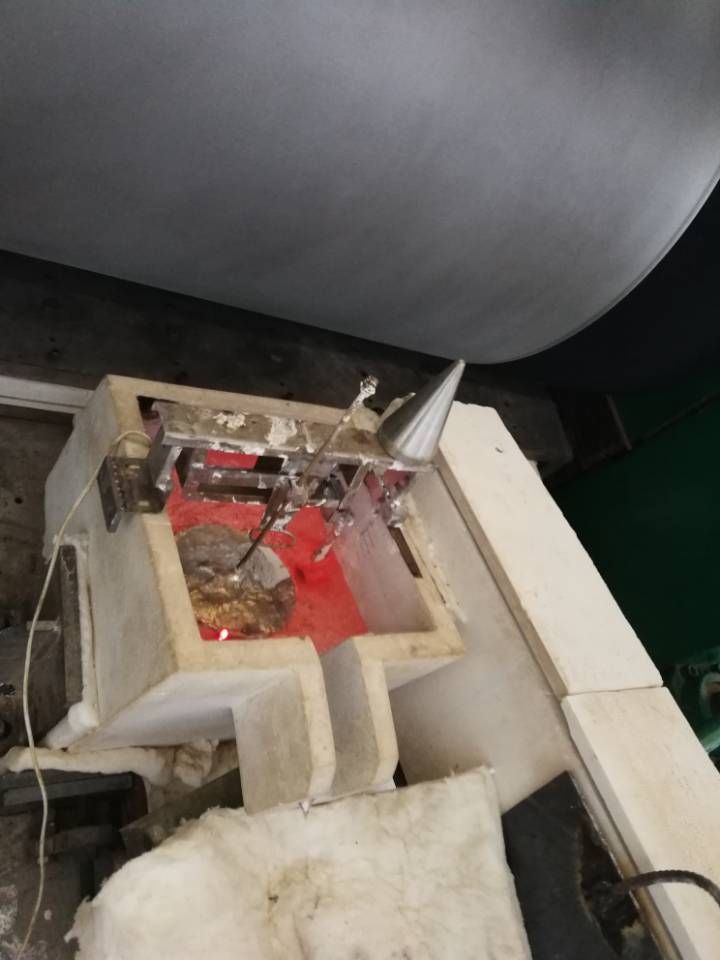
13 11月 Controlled Pouring of Aluminum Castings
Controlled Pouring of Aluminum Castings
Controlled Pouring of Aluminum Castings and rolling mill front tank aluminum liquid level control system and method, the control system includes aluminum liquid level detecting device and aluminum liquid level automatic control device.
The aluminum liquid level detecting device comprises a swinging bracket, the swinging bracket is rotatably mounted on the fixed bracket, and the angular displacement sensor is mounted on the swinging bracket.
The input end of the angular displacement sensor is connected with the middle portion of the transverse guiding rod, the output end of the angular displacement sensor is connected with the corresponding signal end of the controller, and the weight guiding block is installed at one end of the horizontal guiding rod.
The other end is connected with the upper end of the vertical guiding rod, and the lower end of the vertical guiding rod is connected with floating float. The aluminum liquid level automatic control device comprises a control plug corresponding to the aluminum liquid flow control outlet on the front box.
The flow control plug is connected to the plug opening and closing control mechanism. The control method is implemented based on the control system. The invention can automatically control the liquid level of the aluminum liquid in the front box of the aluminum strip casting and rolling mill, and the control precision is high.
This product is made of a special non-stick aluminum fused silica as the aggregate material and is fired. It has good thermal shock resistance, high strength, durability and low thermal conductivity.
Product application: Suitable for casting occasions using mesh ceramic foam filtration.
Controlled Pouring of Aluminum Castings Product Advantages
1.Can be used directly at room temperature, no need to worry about thermal shock.
2.No thermal expansion, low thermal conductivity.
3.Can float in aluminum, reducing the possibility of refractory inclusions.
Controlled Pouring of Aluminum Castings is an essential accessory for forming a smooth filter cavity when using a ceramic filter plate to filter aluminum and aluminum alloy solutions. It has good thermal shock resistance, high strength, strong resistance to mechanical shock, and low thermal conductivity.
Controlled Pouring of Aluminum Castings Use Method
1. Clean the filter box.
2. Gently put the filter plate into the filter box and press the sealing gasket around the filter plate by hand to prevent the aluminum liquid from flowing. 3. Preheat the filter box and filter plate evenly to bring it close to the temperature of the aluminum liquid. Preheat to remove moisture and facilitate initial transient filtration. Preheating can be carried out using electrical or gas heating. Under normal circumstances, it takes about 15–30 minutes.
4. Pay attention to the change of the aluminum hydraulic head during casting. The normal starting pressure head is 100-150mm. When the aluminum liquid begins to pass, the pressure head will drop below 75–100mm, and then the pressure head will slowly increase.
5. During the normal filtration process, avoid knocking and vibrating the filter plate. At the same time, the launder should be filled with aluminum water to avoid too much disturbance of the aluminum water.
6. After the filtration is finished, remove the filter plate in time and clean the filter box.
No Comments