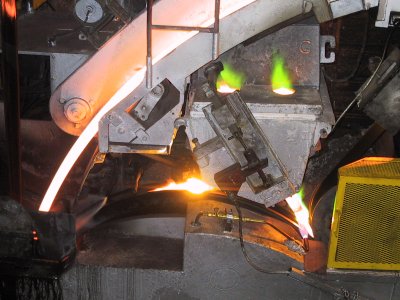
15 12月 Continuous Casting and Rolling for Aluminum Alloy Wire and Rod
Continuous Casting and Rolling for Aluminum Alloy Wire and Rod
Since the Continuous Casting and Rolling of the non-ferrous metal by Illario Properzi have invented in 1944, the various non-ferrous rod, wire and sheet are produced at present.
Although there is long research and trials for producing the wire or rod of commercial the high-strength aluminum alloy, there are few companies with the success in producing commercial hard-aluminum alloys wire and rod by CC&R process.
The application of the high-strength aluminum alloy rod or wire is various parts such as rivet, bolt, sports leisure supplies, high-tension power transmission wire, machinable and forgeable materials.
However, it is very difficult to produce the high-strength aluminum alloy wire and rod by CC&R process because of the wide mushy zone and high strength compared with the pure or low strength aluminum alloy.
Additionally, it is easy to crack and breakout in Continuous Casting and Rolling process due to tiny internal defects of the castings.
The object of this project is to design the most suitable equipments for CC&R and optimize the experimental condition of Continuous Casting and Rolling condition of the high-strength aluminum alloy.
The facilities of CC&R process in RIST are composed of the melting furnace, the wheel casting machine, the automatic machine for moving of castings bar, the 15-step rolling machine with three rolls, the induction heater for reheating the castings bar and the coiling machine.
In the present work, through the numerical computer simulation, in first, we have developed the thermal model of the solidification behavior of the casting bar.
Finally, using finite element code, Marc, the temperature distribution of each rolled bar and effective strain are obtained during Continuous Casting and Rolling.
This application includes companies engaged in rolling, drawing, and extruding aluminum alloy basic shapes such as plate, sheet, strip, bar, and tubing.
In the process of continuous casting of aluminum, coolants and industrial water are used to cool the caster wheel or caster belt, lubricate mill components and transfer aluminum particulate and contaminants to filtration systems using gravity filters or vacuum filters.
Particulate and contaminants are removed by the filter and system pumps transfer clean coolant back to the work.
Continuous casting produces aluminum rod, sheet and rolled products as well. Complete system packages including tanks, pumps, heat exchanger and controls.
No Comments