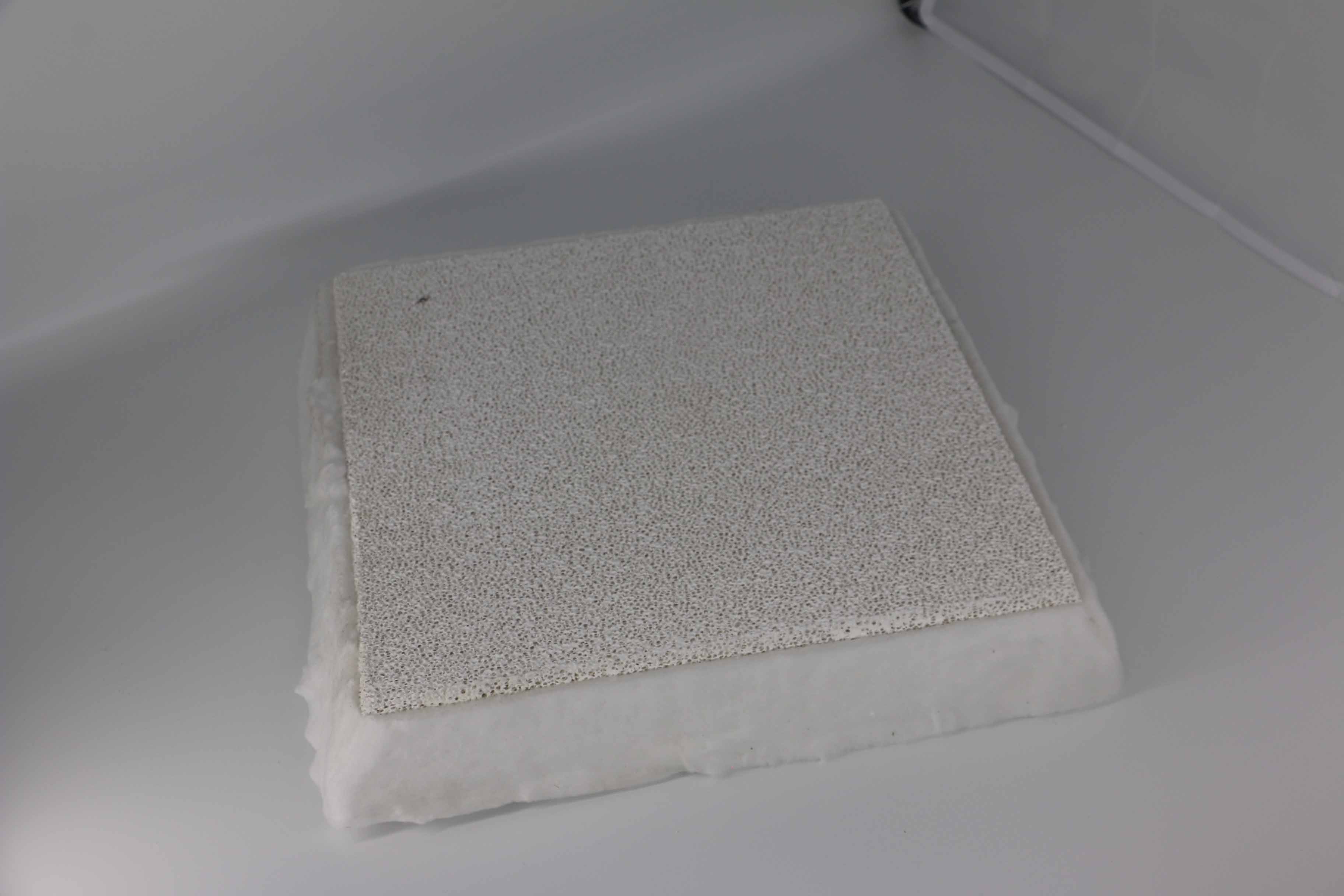
27 7月 Ceramic Foundry Filters
Ceramic Foundry Filters are widely used in aluminum and its alloy casting industry.
At present, with the continuous improvement of the performance requirements of aluminum and aluminum alloy products, new requirements are also put forward for the filtration of aluminum liquid.
The molten aluminum is required to have good casting characteristics such as high purity, less floating impurities, and a gentle flow rate of the molten aluminum, so that the cast aluminum products have excellent physical and chemical properties and machining properties, so as to meet more demanding conditions of use and extend the aluminum products Life.
Features of Ceramic Foundry Filters
1. The top, middle and bottom three-dimensional mesh has no dead holes or blind holes.
2. Sintering temperature>1450℃.
3.The main crystalline phase a-A1203, mullite, no quartz glass phase.
4. High strength (more than three times that of the first generation), excellent thermal shock, and no slag.
5. There are microscopic gaps and strong adsorption of slag.
6. The three-dimensional network high-temperature ion sputtering activation treatment improves the affinity for inclusions in aluminum.
7. Screening, collision sedimentation, adsorption, accumulation, and deeper purification.
8. The initial filtration and adsorption purification effect is significant.
9.All performance indicators have reached the performance indicators of ceramics sintered at 1200 degrees.
10. Achieve a low-carbon economy and reduce emissions by more than 60%.
With the development of modern technology and the demand of modern industry, materials science, as the three pillar industries of the 21st century, is developing in the direction of high specific strength, high strength, high toughness and other comprehensive properties.
For a long time, cast aluminum alloys have achieved great development in industrial applications due to their low price, light weight, and reliable performance.
Especially with the increasing demand for lightweight rail transit materials in recent years.
As the most widely used A356 aluminum alloy in cast aluminum alloys, it has good casting fluidity, good air tightness, small shrinkage rate and small hot cracking tendency. After modification and heat treatment, it has good mechanical properties, physical properties, and corrosion resistance. With better machining performance, aluminum alloy wheels are lighter in weight, safer, more comfortable, and energy-saving compared with steel wheels and valleys. They are increasingly used in the automotive and aviation industries.
During the casting process, due to incomplete slag removal and improper crystallization and cooling conditions during the solidification process, inclusions, shrinkage porosity and shrinkage cavities are easily generated17.
The plate-like eutectic between the secondary dendrite arms of the a-AI dendrite is the weakest area in the material, and the largest Si particles in this area fracture first to form the source of cracks.
Due to the above factors, A356 aluminum alloy is prone to fracture, which affects its strength, plastic toughness and mechanical properties.
If the eutectic Si is gray needle-like and flake-like, distributed disorderly on the a-Al aluminum matrix, the casting shrinkage cavity, casting porosity, oxide film and other defects can be seen in the casting process with an optical microscope. If you need metallurgical material Ceramic Foundry Filter, contact sales@adtechamm.com
6082 is a heat-treatable alloy with good formability, weldability, and machinability.
Medium strength, it can still maintain good operability after annealing. It is mainly used in mechanical structure, including bars, plates, tubes and profiles.
This alloy has similar but not exactly the same mechanical properties as 6061 alloy, and its T6 state has higher mechanical properties.
Alloy 6082 is a very common alloy product in Europe, and also has a high application in the United States. It is suitable for processing raw materials, seamless aluminum tubes, structural profiles and customized profiles.
6082 alloy generally has good processing characteristics and good anode reaction performance.
The most commonly used anode reaction methods include removing impurities and dyeing, coating, etc.
Contact sales@adtechamm.com to buy Ceramic Foundry Filters
Heat treatment process.
1. Smelting
6082 alloy is characterized by containing Mn, which is a refractory metal, and the melting temperature should be controlled at 740-760℃.
Stir evenly for more than two times before sampling to ensure that the metal is completely melted, the temperature is accurate, and the composition is uniform.
After stirring, take a sample in the middle of the molten aluminum depth and on the left and right sides of the furnace for analysis, and the converter can be converted after the analysis is qualified.
2. Purification
After the casting melt is transferred to the static furnace, it is sprayed with nitrogen and refining agent and refining by air jet. The refining temperature is 735-745℃ for 15 minutes. After refining, it is allowed to stand for 30 minutes.
Through this process, gas removal, slag removal, and melt purification. There are two filtering devices between the mold and the furnace mouth during casting. The furnace mouth is filtered by a foam ceramic filter plate (30PPI). Before casting, it is filtered with 14 mesh glass fiber cloth to fully filter out the oxides and slag inclusions in the melt.
Sorry, the comment form is closed at this time.