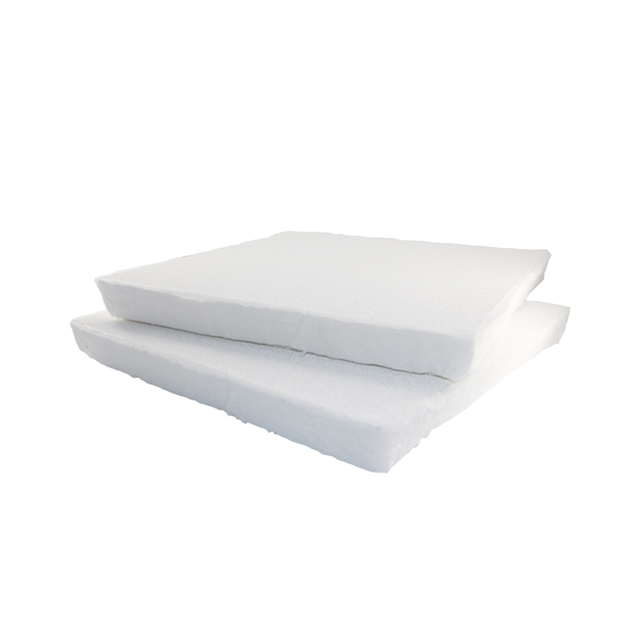
21 7月 Ceramic Foam Filters
Ceramic Foam Filters are used to filter aluminum and aluminum alloy melts
Aluminum surface has a layer of uneven thickness of oxide film, sometimes also adsorbed water, mixed with ash and sand, sticky oil, coated with paint and so on. During melting, the aluminum material is further oxidized in high temperature environment, the thickness of oxide film increases, and reacts with moisture in the atmosphere to form alumina and hydrogen, which increases the content of oxide inclusions and gases. Therefore, after melting, the aluminum must be purified to remove the impurities and gases inside the liquid aluminum.
With the continuous development of domestic industry, the demand for foam ceramic filter plate will further increase in 2011. But for foam ceramic manufacturers, improving foam ceramic production process and improving product performance has become the key for enterprises to compete for the market. Sizing is an important process in the production process of ceramic foam. The degree of sizing directly affects the appearance, through-hole and strength of ceramic filters. The so-called sizing means that the foam ceramic precursor (polyurethane mesh porous sponge) is impregnated in the prepared slurry, and the slurry is evenly adhered to the network of the porous sponge by manual or mechanical equipment. At the same time, through controlling the weight after sizing to ensure the through hole rate and strength of the product.
Sizing principle of sizing machine for foam ceramic filter plate
The porous sponge is immersed in the prepared slurry, and the slurry is attached to the sponge meridians through continuous kneading by the operator, and then rolled back and forth on its surface with a wooden roller until the slurry is evenly distributed on the sponge meridians.
Sorry, the comment form is closed at this time.