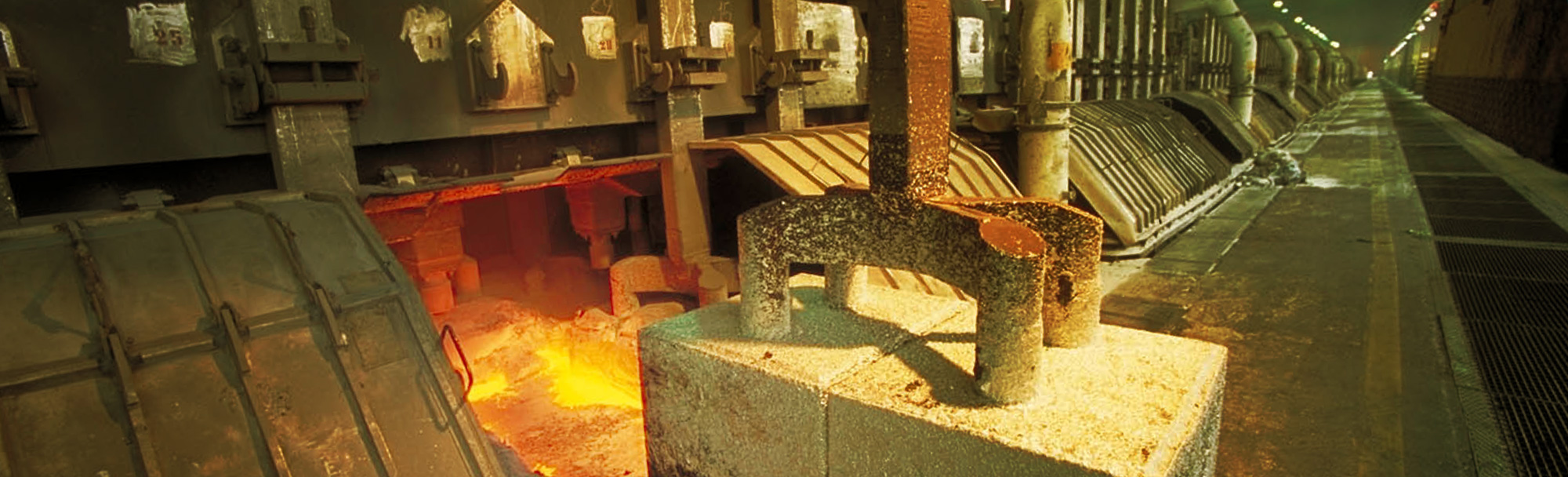
04 12月 Aluminum Smelting and Refining
Aluminum Smelting and Refining
Aluminum is primarily used to produce pistons, engine and body parts for cars, beverage cans, doors, siding, and aluminum foil. It may also be used as sheet metal, aluminum plate and foil, rods, bars and wire, aircraft components, windows, and door frames. The leading users of aluminum include the container and packaging industry, the transportation industry, and the building and construction industry.
Aluminum can either be produced from bauxite ore or from aluminum scrap. Refinement of aluminum ore is sufficiently expensive that the secondary production industry commands much of the market. About 40% of aluminum in the US is recovered for secondary refining (USEPA, 1995).
Due to high energy requirements, the major primary aluminum producers tend to be located in areas with low energy costs, including the Northwest and Ohio River Valley. Secondary producers tend to locate near industrial centers, including southern California and the Great Lakes.
Both primary and secondary aluminum producers refine and melt the aluminum and pour it into bars called ingots. The ingots are shipped to metal casting plants or other shaping plants for molding or rolling.
Of course, before aluminum products are pressed and formed, the aluminum and aluminum alloy liquid must be filtered (Ceramic foam filter absorbs and filters impurities) and degassed (the degassing equipment removes inert gases) to meet the requirements of cast aluminum.
Primary Aluminum Refining
Aluminum production from bauxite ore is a three-step process. First, the alumina is extracted from bauxite ore usually using the Bayer Process. In the Bayer Process, finely crushed bauxite is mixed with sodium hydroxide and placed in a `digester.’ High temperatures and pressures in the digester cause reactions in the ore/sodium hydroxide mixture. The result is dissolved aluminum oxide and ore residue. The residues, which include silicon, lead, titanium, and calcium oxides, form a sludge in the bottom of the digester. The aluminum oxide is evaporated off and condensed. Starches and other ingredients are added to remove any remaining impurities from the oxide.
The solution is then moved to a precipitation tank where the aluminum oxide is crystallized. Aluminum hydroxide and sodium hydrazide are the products of the crystallization. The crystals are washed, vacuum-dewatered, and sent to a calculator for further dewatering.
Aluminum oxide from the Bayer Process is then reduced to the aluminum metal usually using the Hall-Heroult process. In this process, the aluminum oxide is placed in an electrolytic cell with molten cryolite. A carbon rod in the cell is charged and the reaction results in carbon monoxide, carbon dioxide, and aluminum. The aluminum sinks to the bottom where it is removed from the tank and sent to a melting or holding furnace.
The molten aluminum is then mixed with desired alloys to obtain specific characteristics and cast into ingots for transport to fabricating shops. In the fabrication shops, the molten aluminum or aluminum alloys are remelted poured into casts, and cooled. Molten aluminum may be further heated to remove oxides, impurities, and other active metals such as sodium and magnesium, before casting. Chlorine may also be bubbled through the molten aluminum to further remove impurities.
Waste Sources and Pollution Prevention Opportunities
Air emissions come from a number of sources. The grinding of the bauxite, calcinating the aluminum oxide, and handling materials produce particulates. Air emissions equipment is used extensively to capture these particulates.
The particulates may be metal-rich. If the metallic content is sufficient, the emissions control dust can be remelted to capture any remaining metals or it may be otherwise reused or sold for its metallic content. If the dust is not sufficiently metal-rich, it is usually landfilled.
Another source of air emissions from primary aluminum production processes occurs during the reduction of aluminum oxide to aluminum metal. Hydrogen fluoride gases and particulates, fluorides, alumina, carbon monoxide, sulfur dioxide, and volatile organics are produced. Electrolytic baths often use anode pastes in the cell. The paste must be continually fed into the cell through a steel sheet with an opening. This continual feed allows the gas to escape.
One method for reducing gas emissions is the use of pre-baked anodes. Pre-baked anodes must be manufactured in an on-site plant. The pre-baked anodes allow the electrolytic bath to be sealed, allowing gas to be captured. The anodes are then replaced every 14-20 days, containing the gasses for collection. Anode baking furnaces produce fluorides, vaporized organics, and sulfur dioxide emissions. The emissions are often controlled using wet scrubbers.
Liquid waste is not a great concern in aluminum processing. Wastewater is produced during clarification and precipitation; however, much of the water is directly reused.
Solid phase wastes include bauxite refining waste, called red mud, and reduction waste from spent pot liners. Red mud contains iron, aluminum, silica, calcium, and sodium, depending on the ore used. Usually, red mud is managed on-site and is not hazardous.
The refractory lining from the pots used to refine the aluminum is the other solid waste concern. The refractory breaks down with continuous use to produce RCRA K088 hazardous waste.
Secondary Aluminum Production
In the secondary aluminum production industry, scrap aluminum is melted in gas- or oil-fired reverberatory or hearth furnaces. Impurities are removed using chlorine or other fluxes until the aluminum reaches the desired purity.
Other aluminum production plants use dross in addition to scrap. Dross is a by-product of primary aluminum melting. This process further reduces the pollution resulting from primary aluminum production. It contains fluxes and varying concentrations of aluminum. “Skim,” “rich,” or “white dross” refers to aluminum dross with high aluminum content. “Black dross” or “salt cakes” refer to aluminum dross from practices that use salt fluxes.
The dross is crushed, screened, and melted in a rotary furnace where the molten aluminum is collected in the bottom. The resulting salt slag is a waste product. To reduce this waste more of the remaining metallics may be leached into water and collected.
To eliminate the need for salt fluxes, a new plasma torch treatment has been developed to heat the rotary furnace. High concentrations of aluminum are recovered from this procedure.
Pollution Prevention in Secondary Aluminum Processing
Air emissions and solid-phase wastes are the primary concerns in the aluminum processing industry. Air emissions depend largely on the quality of scrap used. Emissions can come from smelting, refining, and the furnace effluent gases. Gases can include combustion products, hydrogen chloride and metal chlorides, aluminum oxide metals, and metal compounds. To reduce emissions regardless of the type of scrap used, aluminum fluoride can be substituted for chlorine to remove impurities from the molten metal. All systems are usually connected to emissions control equipment, typically a baghouse for collecting fluorine and other gases.
Solid-phase waste from secondary aluminum production is slag formed during smelting. The slag contains chlorides, fluxes, and magnesium. The metallics may be separated and reused or sold.
Liquid wastes include water that is added to the slag to help separate the different metals. The wastewater may be contaminated with salt and fluxes, but can often be recovered and reused.
No Comments