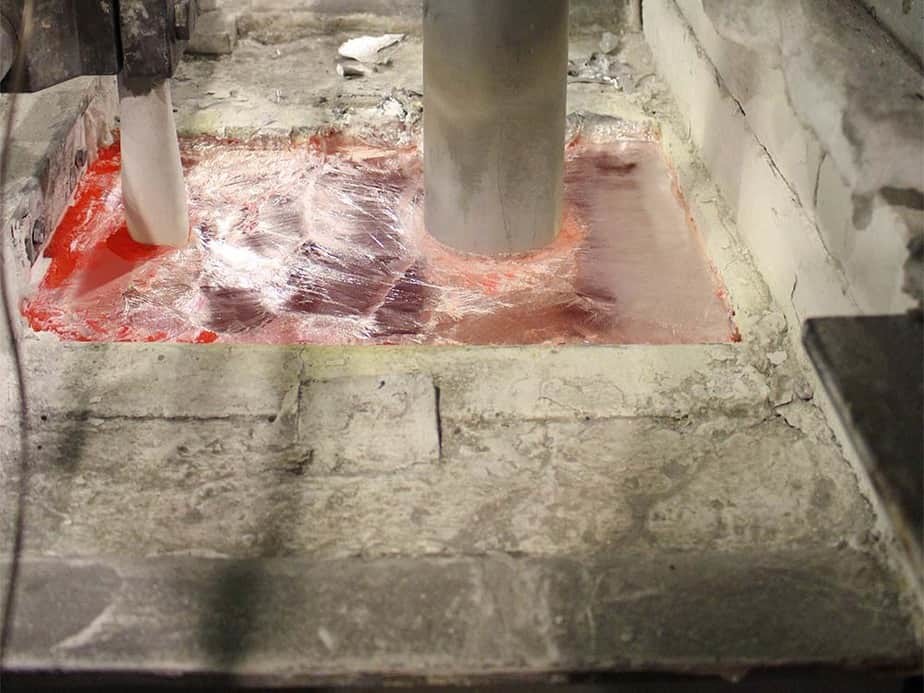
15 10月 Aluminum Degassing Methods
Aluminum Degassing Methods is to reduce the hydrogen (gas content) of aluminum melt before casting is one of the most important components of casting quality control in foundries.
The molten aluminum degasser is placed between the holding furnace and the casting machine.
Nitrogen is blown into the molten aluminum alloy, and then the gas is chopped by a rotating graphite rotor in a degassing tank.
Then, a large number of dispersed bubbles are formed so that the liquid aluminum alloy is in complete contact with nitrogen in the processing tank. According to the principle of air pressure difference and surface adsorption, the bubbles absorb hydrogen and oxidized slag.
The bubbles then rise to the surface of the melt to form scum.
Then, the molten aluminum alloy flows from the outlet of the degassing unit to the degassing machine of the casting machine to achieve the purpose of purifying the aluminum alloy.
The process of removing hydrogen is called degassing. One of the most effective degassing methods is to use inert dry gas nitrogen for rotating inert degassing.
If you want to buy online aluminium degassing machine, contact sales@adtechamm.com
Principle of Degassing
The dissolved hydrogen will move from a high concentration area (in the melt) to a low concentration area (in the inert gas).
Hydrogen will be dispersed in molten metal, just like it is released in any confined space.
It will maintain a constant concentration throughout the melt.
The migration speed of hydrogen in molten aluminum is almost as fast as in air.
Therefore, it is not necessary to expose every ounce of metal to inert gas.
The efficiency of aluminum degassing depends on two factors, the transport rate across the metal/gas interface and the total surface area that can be transported.
Aluminum Degassing Methods——RID device
The larger inert bubbles are divided or cut into smaller bubbles in order to effectively remove hydrogen from the melt.
However, many of these systems use expensive and complex rotor and shaft designs, which increase the cost and life of the shaft and rotor.
A groove is designed at the end of the rotating spray gun, which can effectively cut the inert bubbles into finely dispersed inert bubbles throughout the melt.
In addition to being cheaper than typical shaft and rotor designs, rotary spray guns are more durable and require less downtime.
Aluminum Degassing Methods-bubble size
The principle of rotating degassing is to increase the surface area of the intercalation gas exposed to the metal. The larger surface area increases the transfer rate from metal to inert gas. For a given gas volume, the smaller the bubble size, the larger the surface area. For example, a bubble with a diameter of 1 inch has a surface area of 6 square inches. If the same bubble is divided into bubbles with a diameter of 1/16 inch, the surface area will increase to 96 square inches. In other words, if the same volume of gas is used and the diameter of the bubble is reduced to 1/16 of the original diameter, the total surface area will increase by 16 times. Smaller bubbles have less interference on the surface of the melt, reducing additional hydrogen absorption in humid environments.
Sorry, the comment form is closed at this time.