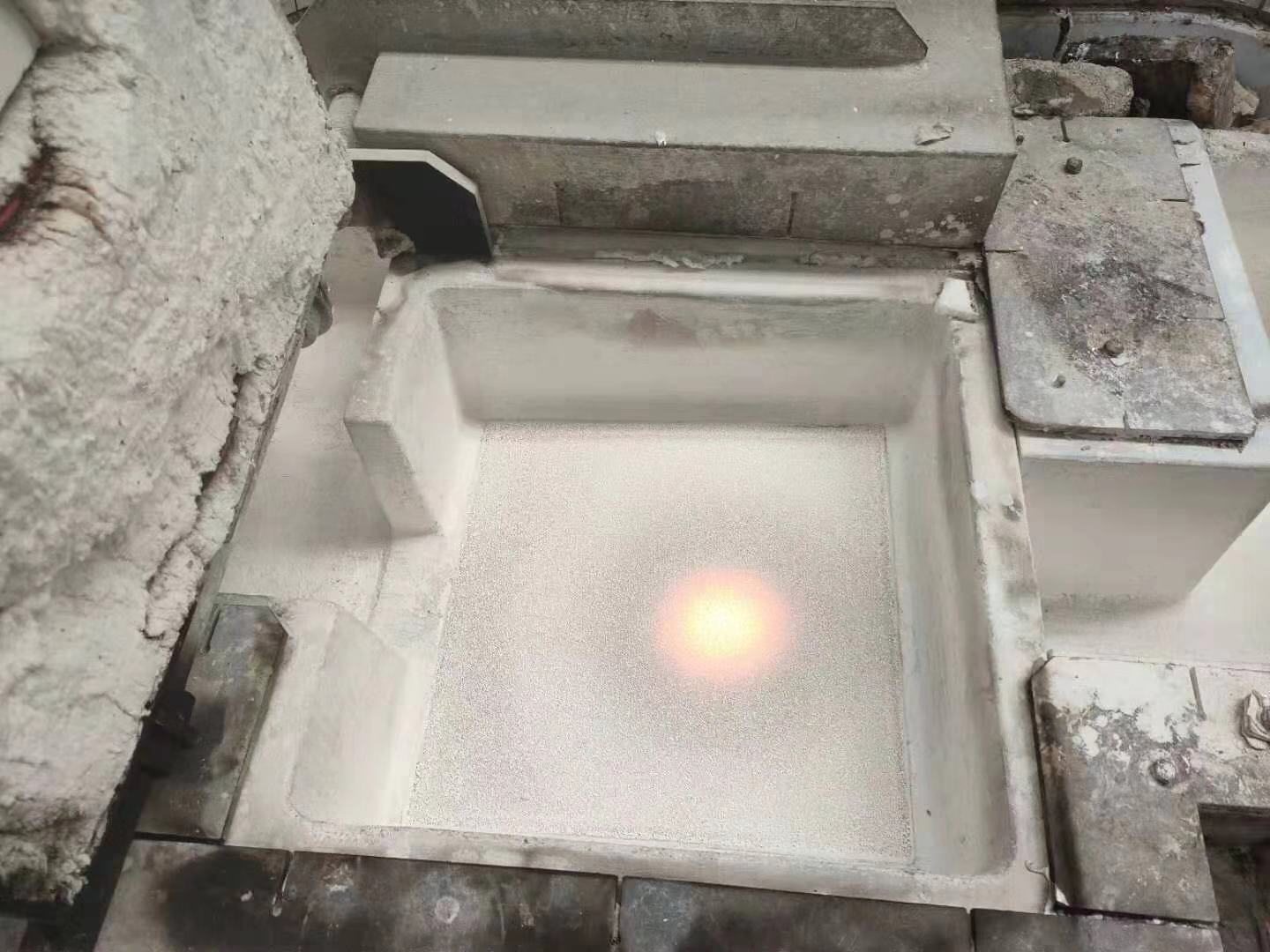
09 9月 Alu Alumina Ceramic Foam Filter
Alu Alumina Ceramic Foam Filter should not be affected by excessive vibration or metal level changes.
These “disturbances” will cause the release of inclusions, which may eventually lead to inclusions in the finished product.
Good process control downstream of the final filtration equipment is especially important.
If repairs are required, this should include careful cleaning preparations and special attention.
In addition, operators in the foundry should take care to minimize turbulence in certain areas, such as turbulence around metal distribution bags.
Even the best Alu Alumina Ceramic Foam Filter, the very dirty metal input will overwhelm you.
Therefore, the importance of correct handling of metals before filtering cannot be overstated.
The cleaner the metal entering the filter, the finer the filter that can be used, resulting in “even cleaner” metal leaving the filter.
If you need further information or support to get good molten metal cleanliness, please feel free to contact our Casthouse experts (sales@adtechamm.com). We can help you optimize the process to meet your metal quality requirements.
The aluminum ingot casting process uses molten aluminum to inject into the mold, and after it is cooled into a cast slab and taken out, the injection process is a key step for the quality of the product.
The casting process is also the physical process of crystallizing liquid aluminum into solid aluminum.
Dubai Aluminum is using Alu Alumina Ceramic Foam Filter and provides the following information to www.adtechamm.com. And recommend this kind of ceramic foam filter to other aluminum melting and casting plants in UAE.
The process flow of casting aluminum ingots is roughly as follows
Aluminium tapping-slagging-weight checking-ingredients-furnace loading-scouring-casting-aluminum ingots for remelting-finished product inspection-finished product inspection-warehousing aluminum discharge-slag slagging-weight testing-ingredients-furnace loading-scouring-casting —Alloy ingot—cast alloy ingot—finished product inspection—finished product inspection—stock in
Commonly used casting methods are divided into continuous casting and vertical semi-continuous casting
The raw materials in our daily industry are called aluminum ingots. According to the national standard (GB/T 1196-2008), they should be called “aluminum ingots for remelting”, but everyone is used to calling them “aluminum ingots”.
It is produced by electrolysis using alumina-cryolite.
After aluminum ingots enter industrial applications, there are two major categories: cast aluminum alloys and deformed aluminum alloys.
Cast aluminum and aluminum alloys are aluminum castings produced by casting methods; deformed aluminum and aluminum alloys are processed aluminum products produced by pressure processing methods: plates, strips, foils, tubes, rods, shapes, wires and forgings.
According to the national standard, “remelting aluminum ingots are divided into 8 grades according to chemical composition, namely Al99.90, Al99.85, Al99.70, Al99.60, Al99.50, Al99.00, Al99.7E, Al99. 6E” (Note: the number after Al is the aluminum content).
Some people call “A00” aluminum, which is actually aluminum with a purity of 99.7%, and it is called “standard aluminum” in the London market.
Everyone knows that my country’s technical standards in the 1950s came from the former Soviet Union. “A00” is the Russian brand in the Soviet national standard. “A” is the Russian letter, not the English “A”, nor the Chinese phonetic alphabet. If “A” is in line with international standards, it is more accurate to call “standard aluminum”. Standard aluminum is an aluminum ingot containing 99.7% aluminum, which is registered on the London market.
Sorry, the comment form is closed at this time.