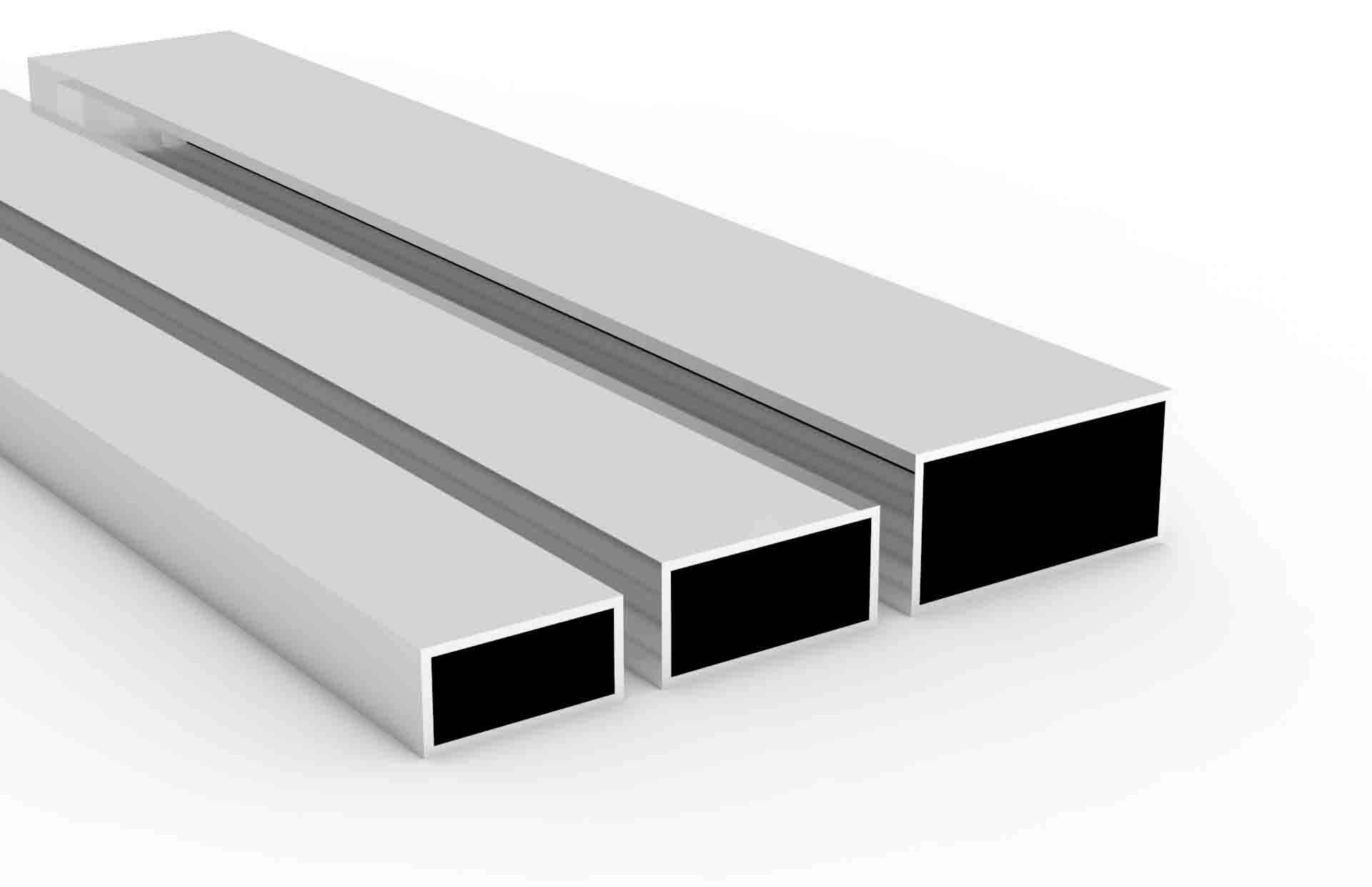
11 6月 Production process of aluminum alloy doors and windows
Production process of aluminum alloy doors and windows includes casting preparation, extrusion molding, heat treatment, surface treatment.
Casting preparation
The process includes the main steps of batching, smelting, casting, soaking and so on to form an ingot with a certain chemical composition and shape.
The prepared raw materials are smelted in a gas stove or an electric stove.
The smelted melt passes through the static furnace, launder, flow plate, filter to the crystallizer, and then water cooled to form a certain shape of ingot.
In order to ensure the surface of the ingot is smooth, magnetic casting or hot top casting method is used to perform multi-mode (multi-crystallizer) casting.
The soaking of the ingot is to homogenize the metallurgical structure in the cast state and dissolve the main strengthening phase.
Soaking is performed in a soaking furnace.
Soaking improves the plasticity of the ingot, helps to increase the extrusion speed, extend the life of the extrusion die, and improve the surface quality of the extruded profile.
Extrusion
Extrusion molding is performed on an automatic production line composed of ingot heating, extrusion, cooling, tension straightening, sawing and other processes.
The equipment on the production line includes induction heating furnace, extruder, furnace table, material conveyor, profile lifting and transferring device, cooling bed, tension leveler, storage table, tractor, sawing machine, etc.
The heating temperature of the ingot is generally controlled at 400 ℃ ~ 520 ℃, too high or too low will directly affect the extrusion molding.
Extruders generally use single-action hydraulic presses, whose tonnage is between 1200 tons and 2500 tons.
The diameter of the extruder barrel of the extruder changes with the tonnage of the extruder, the tonnage of the extruder is large, and the diameter of the extruder barrel is also large.
The diameter of the extrusion cylinder is generally in the range of 150mm~300mm. The working temperature of the extrusion tool is 360℃~460℃, and the extrusion speed is 20m/min~80m/min. Extrusion tools mainly include molds.
Extrusion dies are divided into flat dies, split dies, tongue dies, and shunt combined dies according to structural characteristics. The production of aluminum alloy door and window profiles is multi-purpose flat die and split combination die.
The discharge table receives the profile extruded from the extruder and transitions the profile to the discharge work table.
The discharge table is mostly a horizontal bar transport model, and its horizontal bar movement speed is synchronized with the extrusion speed.
The cooling bed is mostly a walking beam type, and a considerable number of fans are installed below to ensure uniform cooling of the profile, so that the temperature of the profile before straightening is below 70 ℃.
The tension straightening machine is equipped with torsion jaws, which can stretch and straighten while torsion correction. Behind the tension leveler is the storage table, which provides profiles to the working table of the sawing machine, and the sawing machine cuts the profiles according to a fixed length.
Heat treatment
The aluminum-magnesium-silicon aluminum alloy used for aluminum door and window profiles is a strengthenable aluminum alloy.
Through different quenching and aging systems, the profiles can get their due mechanical properties.
Aluminum door and window profiles are supplied by RCS, that is, the heat treatment is rapid cooling and artificial aging after high temperature molding.
Surface treatment
The surface treatment of aluminum door and window profiles is mostly anodized to make the profile surface silver-white.
Surface treatment can enhance the appearance of profiles and prolong the service life of aluminum doors and windows profiles.
Anodizing process flow: loading → degreasing → water washing → alkaline etching → warm water washing → cold water washing → neutralizing light output → water washing → anodizing → cold water washing → warm water washing → sealing → drying → unloading → finished product inspection → packaging The thickness of the oxide film after anodizing aluminum door and window profiles is not less than 10 μm.
The surface treatment of aluminum doors and windows can also be colored. Aluminum profiles requiring other colors can be obtained by natural oxidation coloring method, electrolytic coloring method and dipping coloring method.
Sorry, the comment form is closed at this time.