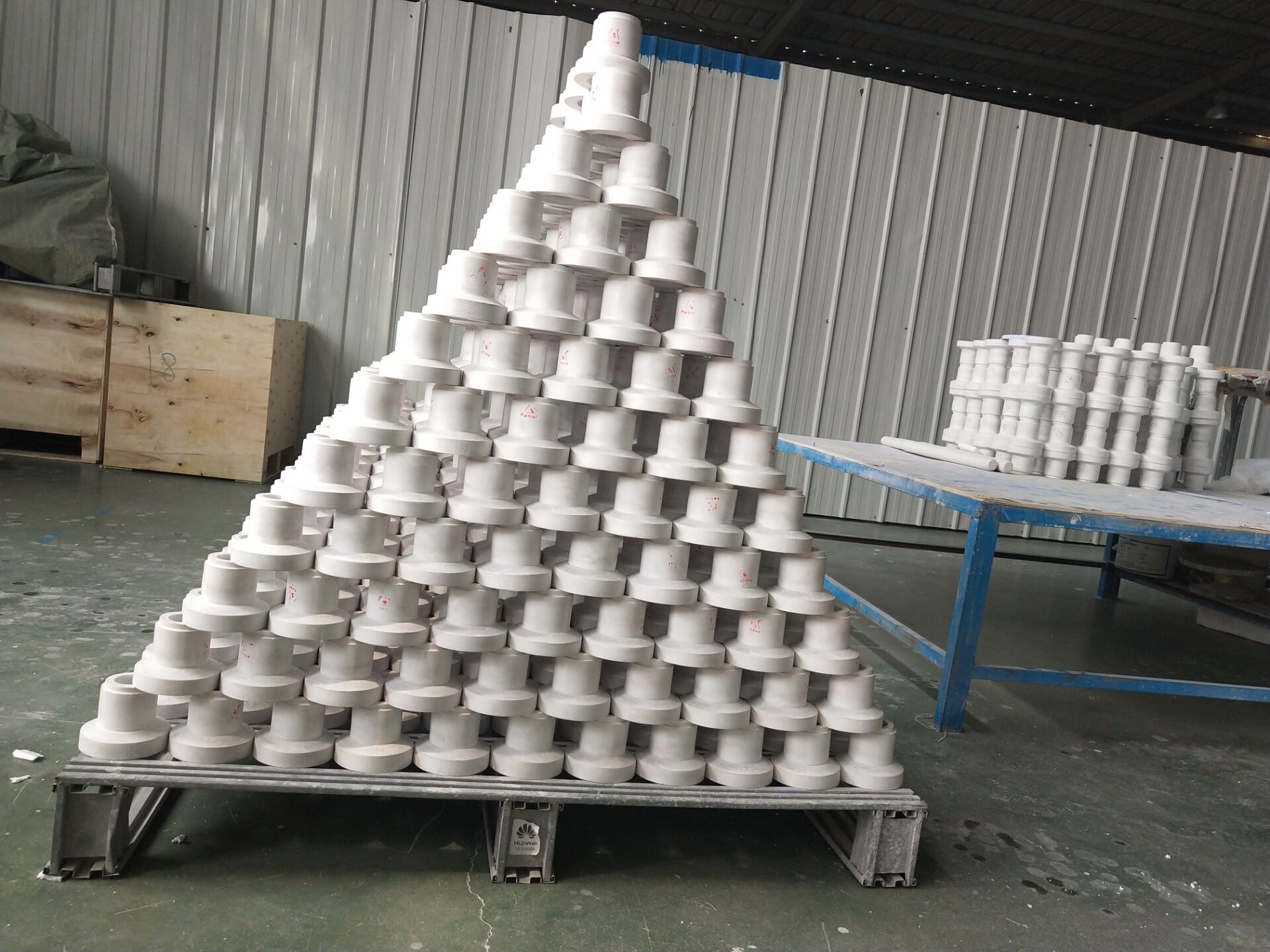
02 11月 Pouring Basin
Pouring Basin is one of the more important parts before molten aluminum enters the mold. Hot-top casting refers to a casting method in which there is a section with good heat preservation performance on the top of the mold, which is used to slow down the primary cooling of the upper part of the mold, rather than slow down the primary cooling of the entire mold.
Working principle of hot top casting
With the help of the coolant used under the water-cooled mold, it is ensured that the solidified metal is not locally remelted on the surface of the ingot, so that the entire ingot can obtain the required shape of the solidification front.
The main process parameters of hot top casting
The height of the cooling part of the mold, the protruding distance inside the insulating layer, the casting speed, the casting temperature, the cooling water pressure, and the height of the liquid level in the hot top tank.
The surface of the produced ingot is smooth, and the degree and depth of inverse segregation around the ingot is greatly reduced.
Because the countercurrent cooling effect of the secondary cooling water is relatively sufficient when the hot top is made, it effectively prevents the secondary remelting of the condensate, thereby inhibiting the formation of segregation tumors.
At the same time, during the casting process, the head of the ingot always maintains a stable liquid column, which reduces the solidification position of the melt in the copper plate manufacturer, effectively prevents the premature cooling of the metal liquid level, and makes the meniscus become Stable, thus also inhibiting the formation of cold barriers.
Pouring Basin is made of two materials
high silicon melting 140 and Al-Si.
It has strong corrosion resistance, high geometric accuracy, smooth casting surface, long life, low maintenance cost, and no pollution to molten metal. It is the best choice for hot top casting , To meet the technical needs for the production of aluminum alloy precision casting products such as aviation, transportation, and electronic products that require high added value and high technical performance.
In the open end of the upper part of the inner sleeve of the mold, there is a graphite sleeve which can reduce the primary cooling effect, reduce the friction between the ingot and the mold wall, and improve the segregation of the ingot.
Aluminium silicate fiber felt with good flexibility is pasted on it to form a liquid metal insulation layer.
There is a heat preservation cap made of heat preservation material on the top of the mold, so that the exposed melt part is always in the “hot cap”.
For the use of gas pressurization and oil ditch device between the mold and the “hot cap” junction, we think it is more suitable for a single production workshop for casting 40-080 mm small round ingots.
As for the large-diameter workshop of semi-continuous production, the effect is not necessarily obvious except for the extensive auxiliary equipment of the operating table.
Sorry, the comment form is closed at this time.