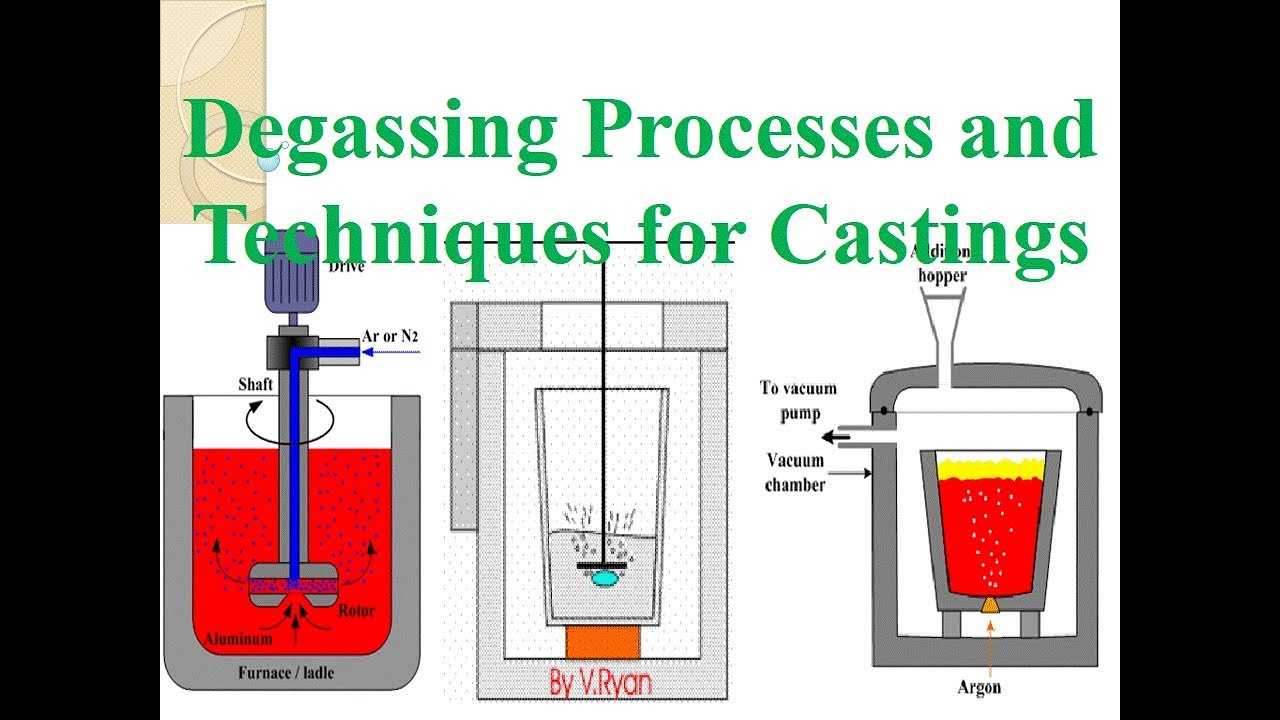
06 7月 Degassing In Aluminium Casting
Degassing In Aluminum Casting
Working principle of the aluminum degassing unit:
The aluminum liquid degassing unit is auxiliary equipment for casting and pouring. It is divided into a fixed aluminum liquid refining machine and a lifting degassing system, which can be customized according to the height of the customer’s furnace equipment.
The high-speed rotating graphite rotor sprays inert gas, breaking up the larger inert gas bubbles (argon or nitrogen) entering the aluminum melt into very fine bubbles, and evenly disperses them in the molten metal.
The rotating rotor can also promote the diffusion of hydrogen and inclusions in the aluminum melt. By reducing the bubble diameter, the total surface area of these bubbles is actively increased, which makes more surface area of the inert bubbles contact with hydrogen and impurities in the molten metal. The bubbles in the melt rely on the gas partial pressure difference and surface adsorption principle to absorb hydrogen in the melt, adsorb oxide slag, and bring these harmful substances to the liquid surface as the bubbles rise, so that the melt is purified.
Graphite rotor:
The graphite rotor can work continuously at a speed of 200r/min~400r/min in aluminum melt at about 750℃.
The quality of graphite itself has a significant impact on the service life of the rotor. If an anti-oxidation coating is applied on the surface, the service life can be extended to 2-3 months.
No Comments