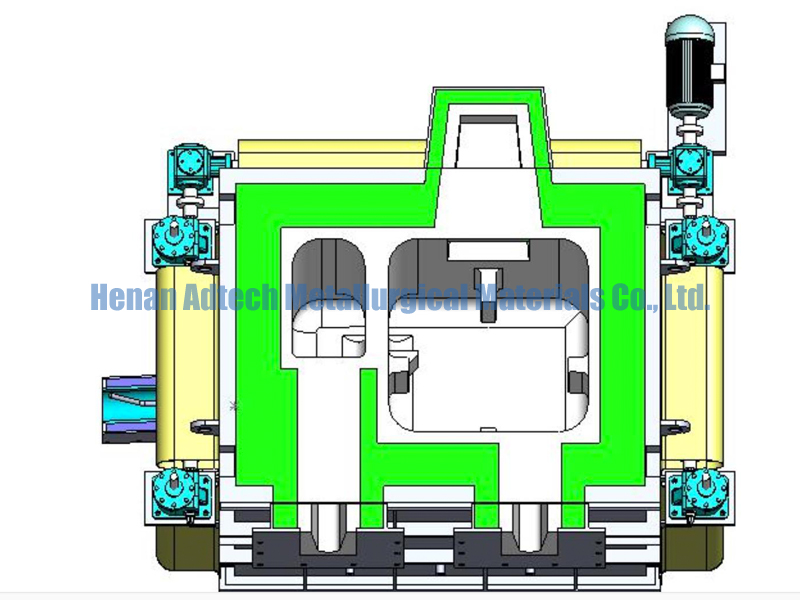
09 9月 Degassing Methods In Casting
Degassing Methods In Casting
During smelting, aluminum melts are purified from dissolved metal impurities (sodium, magnesium, iron and zinc), suspended oxide (non-metallic) inclusions and dissolved hydrogen.
For these purposes, various methods of purging the melts with inert and active gases, sedimentation, treatment with chloride salts and fluxes, evacuation and filtering through mesh, granular and sintered ceramic filters are used.
Degassing Machine in Degassing Methods In Casting from aluminum and aluminum alloys AMg2 and AMgb can be carried out by blowing the melt with chlorine, a mixture of inert gas with chlorine (per 100 volume parts of inert gas, 1-10 volume parts of chlorine), chloride vapors (CrC1b. CC14, TiCl4), freon (CCI2F2 ) and filtration through granular filters from AlFj or ABO3 activated with chlorine or fluorine.
The consumption of refining gas is 0.2 … 0.5 m ‘per 1 ton of melt. Duration of blowing through ceramic nozzles or porous ceramic inserts 10 … 15 min at melt temperature.
Degassing Methods In Casting, impurities of lithium, potassium and calcium are also removed from the melt and up to 0.2% Mg is lost.
Melts are filtered through filters with a thickness of 150 … 200 mm from grains with a diameter of 4 … 6 mm. The above refining methods make it possible to bring the residual sodium content in the melt to (2 … 3) -1 () ’4%.
The harmful effect of sodium on the technological properties of the AMgb alloy can be suppressed by introducing bismuth or antimony additives (0.2 … 0.3% of the mass of the melt) into the melt, forming intermegallides with sodium, melting at 775 and 856 ° С, respectively.
Gas purging is widely used for degassing melts and cleaning them from non-metallic inclusions.
Refining is carried out the more successfully, the smaller the size of the bubbles of the purged gas and the more uniform their distribution over the volume of the melt. Purge, as a rule, is carried out through porous inserts from sintered alumina, which ensure the production of gas bubbles with a diameter of 1.5 … 2.0 mm.
This refining method is widely used in foundries for the production of ingots.
The purge is carried out in special lined containers installed on the nougat of overflow of metal from the mixer into the mold or in the buckets.
A porous ceramic insert is installed in the bottom of the bucket or container.
For refining aluminum melts, nitrogen, argon, helium, chlorine and a mixture of nitrogen (90%) with chlorine are used, purified from moisture and oxygen.
Degassing Methods In Casting with nitrogen or argon is carried out at 720 … 730 ° C.
The duration of the purge, depending on the volume of the melt, ranges from 5 … 20 min; gas flow rate is 0.5 … 1.0 m ‘per 1 ton of melt.
Such processing allows to reduce the content of non-metallic inclusions to 0.5 … 0.1 mm2 / cm2 according to the technological sample of Dobatkin-Zinoviev, and the hydrogen content to 0.20 … 0.15 cm per 100 g.
When using special tuyeres for blowing melts, the gas velocity at the nozzle exit is 200 … 250 m / s, which ensures dispersion of gas bubbles in the melt volume up to 3 … 5 microns; while the purge duration does not exceed 5 minutes, and the gas flow rate per 1 ton of melt is 0.05 m ‘.
The treatment of melts with chlorine is carried out in sealed chambers or buckets having a lid with the removal of gases into the ventilation system. Chlorine is introduced into the melt through tubes with nozzles at 7 ° … 720 ° C.
The refining duration of Degassing Methods In Casting at a chlorine pressure of 0.11 … 0.12 MPa is 10 … 12 min; chlorine consumption 0.3 … 0.5 m3 per 1 ton of melt.
The use of chlorine provides a higher level of purification in comparison with technical nitrogen and argon.
However, the toxicity of chlorine, the need to process melts in special chambers and the difficulties associated with its purification, significantly limit the use of chlorination of melts in an industrial environment. Replacing chlorine with a mixture of it with nitrogen provides a fairly high level of purification, but does not solve the problems associated with toxicity and drying.
Gassing is accompanied by a loss of magnesium. When treated with nitrogen, 0.01% Mg is lost; chlorine degassing increases these losses to 0.2%.
The necessary operation after purging is the exposure of the melt for 10 … 30 minutes to remove the smallest gas bubbles. The use of melts immediately after purging without holding is always associated with the formation of a large number of gas defects in castings.
During the purge process, a significant amount of foam is formed, which is carried away by the metal flow into the casting. The suppression of pricing is achieved by applying a layer of salt granules with a diameter to the surface of the melt in the purge chamber.
Sorry, the comment form is closed at this time.