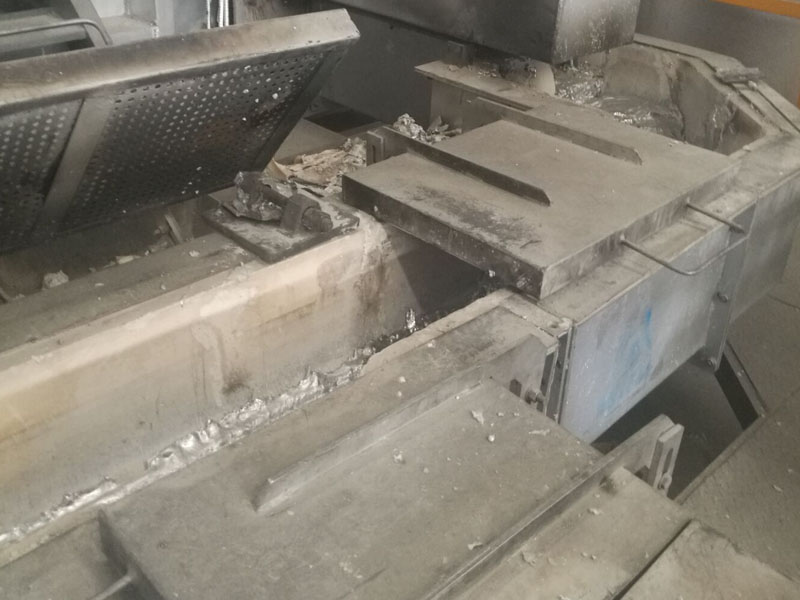
06 5月 Ceramic Launder System
Ceramic Launder System
Ceramic Launder System from Adtech China is mainly used for aluminum alloy transportation between aluminum alloy precision casting aluminum melting furnace, purification furnace, casting platform, degassing and filtration outside the furnace.
Ceramic Launder System lining
Adtech uses an advanced monolithic lagging lining process: greatly improving the erosion and erosion resistance of the launder lining.
Effectively extend the service life of the runner lining. In combination with our boron nitride coatings, the non-stick aluminum effect is excellent, and the inner lining can be independently produced according to the needs.
Ceramic Launder System Lining can only be baked with flame if it does not have electric heating and baking conditions. The key one is to control the flame temperature, and the other is to avoid direct flame grilling and avoid the thermal stress generated by local heat, causing the liner, tube body, disc body or filter plate to burst.
Ceramic Launder System Advantages
Good insulation performance, reasonable design and long service life;
It is integrally molded with noble molten material and has high dimensional accuracy;
The lining has high strength, erosion resistance, heat shock resistance and smooth surface;
The inner liner has strong corrosion resistance to aluminum, zinc and magnesium alloys, enhances the use effect of the molten metal transfer equipment, and strengthens the service life of special alloys;
The temperature drop of the metal liquid during use is 2 ° C per meter, resistant to erosion, heat shock and smooth surface.
Ceramic Launder System Instructions for Use
Corresponding to the drawing structure, the flow cell is installed to ensure that the overall flow path is clean, no damage, no gap.
Uniformly preheat the installed flow path, heat up at a constant speed for 6-8 hours, check the surface of the lining red, ie 800 °C, to remove the adsorbed crystal water, close to the casting temperature, safe and efficient use.
If the tank flow tank does not have electric heating baking conditions, it must be baked with flame.
The key one is to control the flame temperature, and the other is to avoid direct flame grilling and avoid the thermal stress generated by local heat, causing the liner, tube body, disc body or filter plate to burst.
Sorry, the comment form is closed at this time.