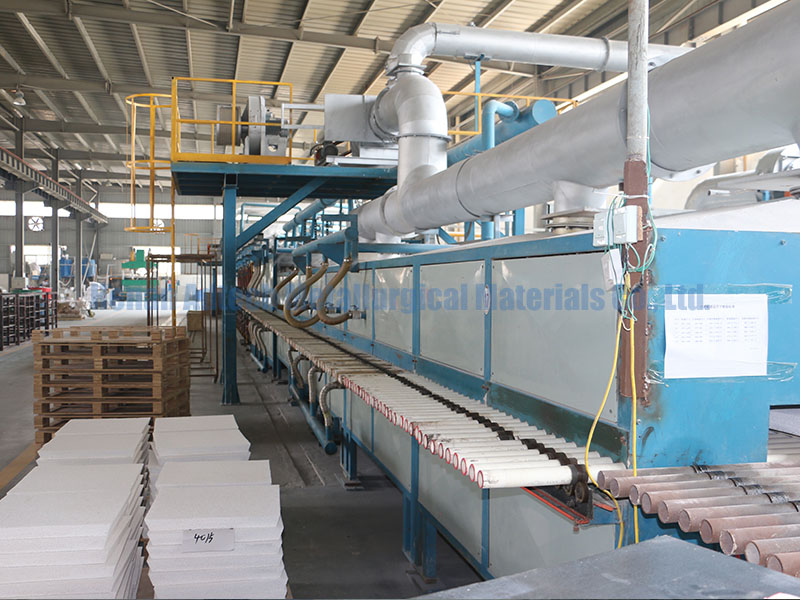
16 11月 Ceramic Foam Filter Manufacturing Process
Ceramic Foam Filter Manufacturing Process
Ceramic foam filter is manufactured in several different ways. The polymeric-sponge method produces open-cell structures by impregnating a polymeric sponge with a ceramic slurry, which is then burned out to leave aporous ceramic filter.To create a honeycomb or cellular structure, a plastic-forming method called extrusion is used, where a mixture of ceramic powder plus additives is forced through a shaped die (like play dough).
(AdTech Metallurgical Materials Co., Ltd. is a Ceramic Foam Filter Manufacturers China Suppliers, who is focused on Ceramic Foam Filter Technology For Aluminum Foundries, one of Alumina Ceramic Foam Filters For Aluminum. Adtech has been Making A Porous Ceramic Filter since 2012 year)
There are several methods used to make Ceramic Foam Filters For Casting Foundry. The polymeric sponge method, which will be described in more detail here, produces open-cell structures by impregnating a polymeric sponge with a ceramic slurry, which is then burned out to leave a porous ceramic. The direct foaming method can produce both open-cell and closed-cell structures, with the foam structure more common. In this method, a chemical mixture containing the desired ceramic component and organic materials is treated to evolve a gas. Bubbles are then produced in the material, causing it to foam. The resulting porous ceramic material is then dried and fired. For the honeycomb or cellular structure, a plastic-forming method called extrusion is used, where a mixture of ceramic powder plus additives is forced through a shaped die (like play dough). The cellular structure can also be produced using a pressing method.
Selecting the sponge
1 First, a polymeric sponge must be selected with suitable properties. The pore size of the sponge determines the pore size of the final ceramic after firing. It must also be able to recover its original shape and convert into a gas at a temperature below that required to fire the ceramic. Polymers that can satisfy these requirements include polyurethane, cellulose, polyvinyl chloride, polystyrene, and latex. Typical polymeric sponges range in size from 3.94-39.4 in (10-100 cm) in width and 0.394-3.94 in (1-10 cm) in thickness.
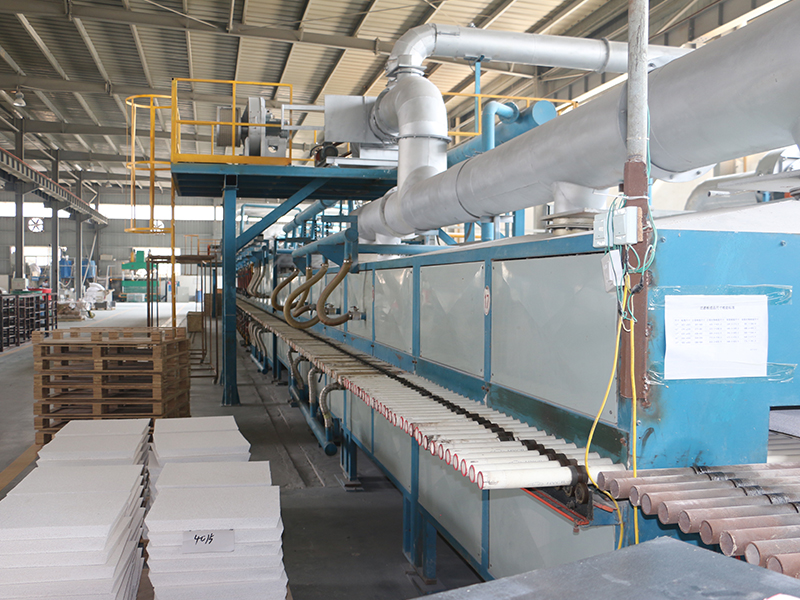
Ceramic Foam Filter Manufacturing Process
Preparing the slurry
2 After the sponge is selected, the slurry is made by mixing the ceramic powder and additives in water. The ceramic powder usually consists of particles less than 45 microns in size. The amount of water can range from 10-40% of the total slurry weight.
Immersing the sponge
3 Before immersion, the sponge is usually compressed to remove air, sometimes using a mechanical plunger several times. Once it is immersed in the slurry, the sponge is allowed to expand and the slurry fills the open cells. The compression/expansion step may be repeated to achieve the desired density.
Removing excess slurry
4 After infiltration, between 25-75% of the slurry must be removed from the sponge. This is done by compressing the sponge between wooden boards, centrifuging, or passing through preset rollers. The gap between rollers determines the amount removed. Sometimes the impregnated foam goes through another shaping step since it is still flexible.
Drying
5 The infiltrated sponge is then dried using one of several methods—air drying, oven drying, or microwave heating. Air drying takes from eight to 24 hours. Oven drying takes place between 212-1,292° F (100-700° C) and is completed in 15 minutes to six hours.
Burning out the sponge
6 Another heating step is required to drive off the organics from the slurry and burn out the sponge. This takes place in air or inert atmosphere between 662-1,472° F (350-800° C) for 15 minutes to six hours at a slow and controlled heating rate to avoid blowing apart the ceramic structure. The temperature depends on the temperature at which the sponge material decomposes.
Firing the ceramic
7 The ceramic structure must be heated to temperatures between 1,832-3,092° F (1,000-1,700° C) to densify the material at a controlled rate to avoid damage. The firing cycle depends on the specific ceramic composition and the desired final properties. For instance, an aluminum oxide material may require firing at 2,462° F (1,350° C) for five hours.
Adtech | Foundry Ceramic Foam Filter
Posted at 09:35h, 16 11月[…] Choosing the right size of a Ceramic foam Filter […]
admin
Posted at 03:30h, 22 11月Hi, man , how r u.