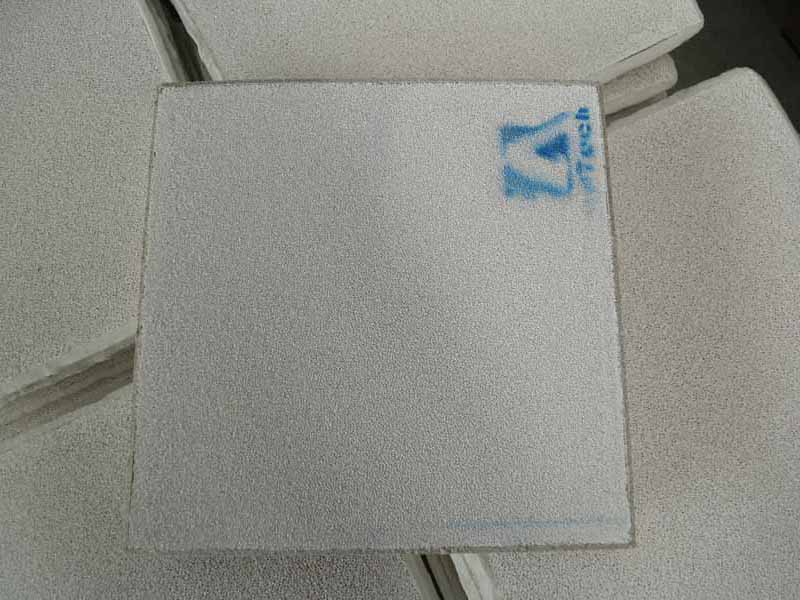
20 10月 Ceramic Foam Filter Casting
Ceramic Foam Filter Casting is mainly used for the filtration and purification of aluminum and alloy liquid in foundries with excellent resistance to corrosion and corrosion of aluminum liquid.
It can effectively remove inclusions, reduce trapped gas, provide laminar flow, and the filtered metal is significantly cleaner.
Cleaner metals result in higher quality castings, less scrap and fewer inclusion defects, all of which contribute to the bottom line of profit.
Purpose:Ceramic Foam Filter is used to filter aluminum slag
●Reduce waste related to inclusions
●Reduce costs related to inclusion defects
●Increase the speed of extrusion or rolling and increase productivity
●Increase casting flexibility, easy to replace alloy
●It is forbidden to clamp metal
Ceramic Foam Filter Casting product features
●Superior dimensional tolerance
●Stable chemical composition
●Highest filtration efficiency
●Excellent strength
●Resistant to corrosion of molten aluminum and alloys
●Bevel and compressible gasket
Ceramic foam filter Dimention
660x660x50(26″)
584x584x50(23″)
508x508x50(20″)
432x432x50(17″)
381x381x50(15″)
305x305x50(12″)
228x228x50(9″)
178x178x50(7″)
Physical properties
Main material: Al2O3
Working temperature: ≤1100℃
color: White
Hole density: 10/20/30/40/50/60PPI (PPI = aperture per inch)
Porosity (%): 78 90
Compressive strength (MPa): ≥1.0 (room temperature)
Bulk density (g/cm3): 0.35 or 0.45
Thermal shock resistance: ≥2 times/800℃-room temperature
Casting is one of the most widely used industries for foam ceramic filters. Its function is to make the turbulent and churning metal liquid become a stable, uniform and clean metal liquid after passing through the foam ceramic honeycomb holes.
Thereby greatly reducing the casting scrap rate due to casting defects such as non-metallic inclusions, saving production costs.
Aluminium Cff uses polyurethane foam as a carrier and is immersed in ceramic slurry made of ceramic powder, binder, sintering aid, suspending agent, etc.
Then squeeze out the excess slurry, so that the ceramic slurry is evenly coated on the carrier skeleton into a green body.
The green body is dried and sintered at high temperature. This process is also known as the organic foam impregnation method, and is currently a common domestic foam ceramic production process.
Alumina foam ceramic filter?is an important branch of three categories of foam ceramics (alumina, silicon carbide, zirconia), and it is also the earliest type of foam ceramics. It is widely used in the aluminum and alloy casting industry .
At present, with the continuous improvement of the performance requirements of aluminum and aluminum alloy products, new requirements have been continuously put forward for aluminum liquid filtration, which requires casting characteristics such as high purity, less float, and smooth aluminum liquid flow rate to achieve Aluminum products have better physical and chemical properties and machining performance, so as to meet more stringent use conditions and achieve the purpose of extending the service life of aluminum products.
Every technological process in the production of foamed ceramics has an impact on the quality of foamed ceramic products, of which the key process ingredients, sponge processing and sintering have the greatest impact on product quality. The spraying process mainly affects the product quality and appearance, and at the same time, it also has a certain influence on the internal quality.
Sorry, the comment form is closed at this time.