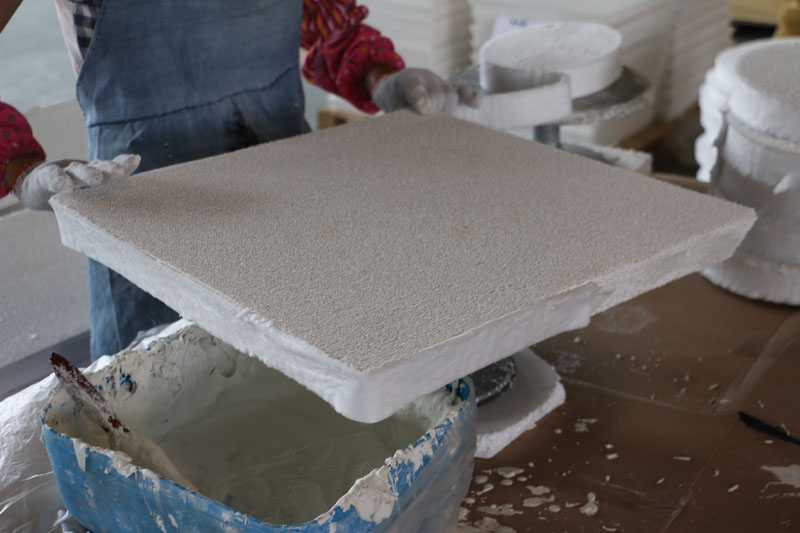
23 12月 Ceramic Filter Foundry for Casting
Ceramic Filter Foundry for Casting is mainly used to filter aluminum and aluminum alloys in foundries and foundries. The filter mechanism of ceramic foam filters used for casting is usually described as diffusion interception and inertial collision interception or screening, sedimentation and deep Bed filtration.
Because Ceramic Filter Foundry has excellent resistance to molten aluminum erosion and corrosion, it can effectively remove inclusions, reduce residual gas and provide laminar flow. It is suitable for improving the quality of aluminum alloy and other non-ferrous alloy castings. Improve the metallurgical structure and enhance the mechanical properties to transform turbulent flow into laminar flow.
The molten aluminum filtered by Ceramic Filter Foundry is significantly cleaner. Cleaner aluminum can produce higher quality castings in industries such as aerospace, automotive, electronics, etc., all of which help increase profits.
Advantages of Ceramic Filter Foundry
1. Ceramic Filter Foundry adopts the principle of adsorption to filter, which can effectively remove large impurities in molten aluminum and effectively absorb small and small impurities;
2. Ceramic Filter Foundry has no slag, effectively reducing the pollution of molten aluminum;
3.Ceramic Filter Foundry has good thermal shock resistance and corrosion resistance to molten metal;
Ceramic Filter Foundry supplier AdTech (sales@adtechamm.com) provides all standard sizes and different thickness products. We provide all porosities from PPI 10 to PPI 60 (PPI = number of holes per inch). The size of the filter can also be customized.
Common sizes of ceramic foam filter suppliers
Suppliers of ceramic foam filters have various common sizes:
7″, 9″, 12″, 15″, 17″, 20″ and 23″.
Tsinghua University has a state key laboratory to establish a three-dimensional physical model and a two-phase flow model for the foam ceramic filtration mechanism.
And carried out simulation calculation, which is very helpful for us to study the purification of aluminum liquid filtration. However, the process of filtering and purifying molten aluminum by ceramic foam is very complicated, and it is also a complex process of high temperature physical chemistry and metallurgical dynamics.
Tsinghua University explains the working principle of Ceramic Filter Foundry for Casting
1. The influence of the sediment layer or filter cake layer, the deposition of particles in the melt and the interweaving and curved joints of the grid, the ability to capture phase particles is improved.
2. The rough surface formed by the surface gap of the mesh truss body increases the interface between the molten aluminum flow and the surface of the Ceramic Filter Foundry, thereby promoting particles in the molten aluminum flow.
3. Due to the fine cracks and pinholes on the surface of the network framework, the flux of fluoride which has a strong affinity for Al2O3 and other particles is pre-deposited.
Ceramic Filter Foundry’s entire filter cake effect and strong chemical adsorption power enhance the ability to capture retained foreign particles.
Sorry, the comment form is closed at this time.