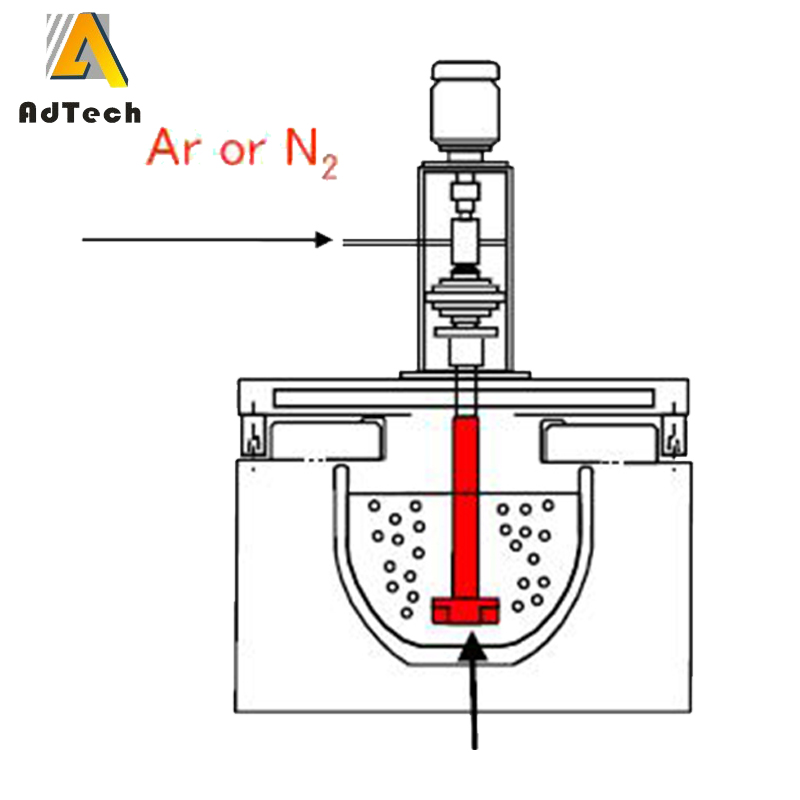
19 6月 Castable Refractory Degassing Molten Aluminum With Nitrogen
Castable Refractory Degassing Molten Aluminum With Nitrogen
Degassing Molten Aluminum With Nitrogen is fully lowered into the liquid metal with the shaft in place, the degassing operation can begin. The best shaft location is slightly off the centerline of the crucible or ladle to help avoid vortex formation with its circular rotation in the liquid metal. An offset distance of 2-4 in. from the centerline is usually sufficient. The use of a baffle plate also is a good idea, because the baffle opposes the circulation movement of metal and reduces vortex formation.
With the RID in the proper location, the unit should be turned on and the shaft speed should be set to 300 RPM. The inert gas flow also should be on and operators should then adjust the gas flow rate and shaft speed. Gas flow should be increased until see gas bubbles are visible as they float to the surface of the liquid metal. As the gas flow increases, the size of the bubbles should increase.
The desired result is a good dispersion of small bubbles while maintaining a relatively quiet surface. When an optimal combination of flow rate and shaft rotation speed is found, note the parameters for future use. Also note the total degassing time, which normally falls somewhere between four and eight minutes, unless the temperatures are very high or the amount of gas needed is low.
Classification of cast aluminum alloys.
Each cast aluminum alloy is designated by a four digit number with a decimal point separating the third and the forth digits.
Molten Aluminum Degassing Unit Characteristic
1.It is tilting type without the need of draining.
2.It is rotating titling and don’t need heat-preservation
3.Totally molten aluminum casting and can change the alloy rapidly.
4.Portable and movable type, preheated by liquefied gas automatically fast heating-up
5.Hydraulic operation, humanized program management
6.Less easy worn parts, safe and reliable
7.Low operating cost, and thoroughly resolves the intensity of labor
Degassing Molten Aluminum With Nitrogen, typically introduced into the melt by a rotary degassing unit. This degassing process is limited by thermodynamic laws; when purge gas bubbles are introduced to the melt, they collect hydrogen as they float toward the surface. The best possible situation is these hydrogen-saturated bubbles leave the melt and reduce hydrogen levels. In this case, the process efficiency is 100% from the thermodynamic point of view. But as the gas content in the melt drops, so does the equilibrium pressure of hydrogen in the bubbles, so the amount of purge gas required to remove the remaining hydrogen must increase.
The equilibrium gas removal ratio for pure aluminum above 1,400F (760C). A gas removal ratio of 200, for example, means it will take 200 liters of inert gas to remove one liter of hydrogen. This behavior limits a metalcaster’s ability to degas to a very low level of hydrogen. The solubility also increases exponentially with temperature, meaning an increase of 200F (111C) doubles the solubility. All things being equal, a higher temperature of an aluminum melt will increase the necessary degassing time.
Alloying elements also can have an effect on hydrogen solubility. The effect of alloying elements is characterized by changes in the alloy correction factor, with some common casting alloys show in Table 1. Alloys having greater values are more difficult to degas, so, for example, aluminum 535 will take four times longer to degas than pure aluminum. Fortunately, these factors can be controlled and the gas content and process required to eliminate excessive porosity in aluminum castings can be achieved without undue difficulty in most cases.
Sorry, the comment form is closed at this time.