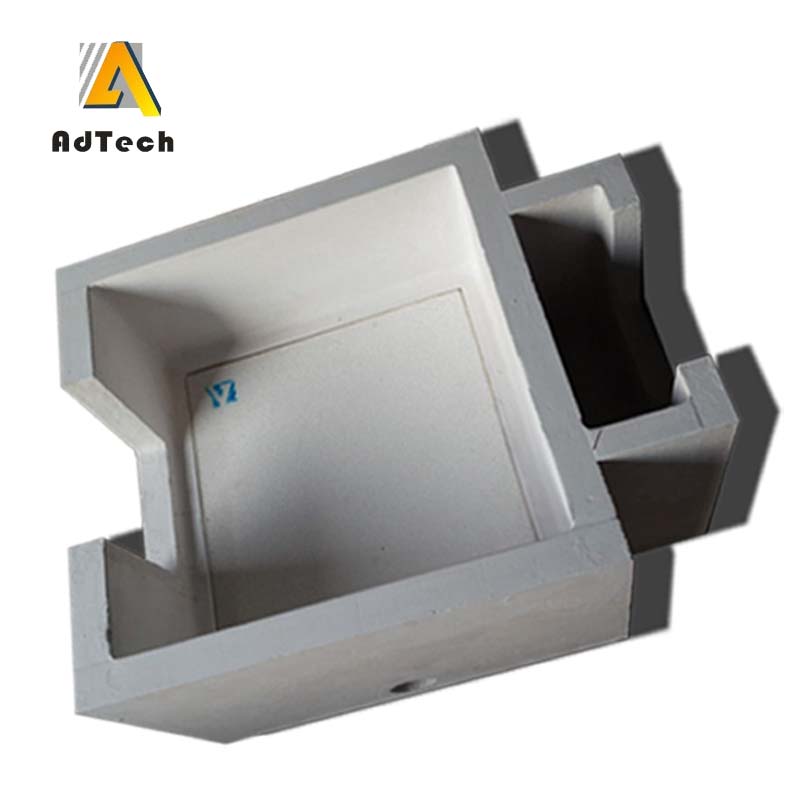
19 6月 Aluminum Ingot Metallurgy Castable Refractory Ceramic Disc Filter
Aluminum Ingot Metallurgy Castable Refractory Ceramic Disc Filter
Ceramic Foam Filter from AdTech Metallurgical Materials Co., Ltd has been focusing on research, development, production and marketing of the adhesive Foam Ceramic Disc Filter(CFF) for aluminum alloy casting Since 2012.
Adopt adsorption principle for filter, can effectively remove big piece inclusions in molten aluminum, and effectively adsorb tiny inclusions.
No broken bits drop out, effectively reduce the pollution of molten aluminum.
Superior thermal shock resistance, improve erosion resistance ability of molten metal.
Automatic flow production,3 calibration procedures,precision size,fit the filter bowl tightly.
Improve the surface appearance and performance, purify molten aluminum.
Natural melting points of various metallic elements are very high. The range of melting point of metals may vary but generally is around few hundred to more than thousand degrees Celsius. It is therefore very necessary that Asian Foundry Filters must have certain properties. Here are some useful properties
Porosity It is the percentage of the pore space in the China Ceramic Foam Filter Cff. This property is very important in operations as a filter with much larger or smaller porosity can hamper the process. Therefore, it is recommended that porosity must be ideal in terms of the types of molten metal used.
Instructions for Aluminum Casting Using Ceramic Disc Filter
Inspect and clean the surface of filter bowl, keep it clean and intact.
Gently lay the filter in the filter bowl, press sealing gasket around the filter by hand to prevent molten aluminum from dispersing or floating away.
Use electric or gas burning to preheat filter bowl and ceramic foam filter evenly for 15-30 minutes, make sure their temperature close to molten aluminum. The preheating temperature for ceramic foam filter should above 260℃. Expanding cotton will seal after preheating. This procedure makes ceramic foam filter steady fixed in molten aluminum. Preheating also leads ceramic foam filter pores open and avoid occlusion caused by thermal expansion and contraction.
Observe the change of molten aluminum height, hold molten aluminum flow in standard needs. Normal starting molten aluminum height is 100-150mm. The height falls down below 75-100mm when molten aluminum flows, and it will slowly increase later.
Do not hit or shake ceramic foam filter in filtration. At the same time, control molten aluminum flow rate in launder, never to be too much or too little.
Take out ceramic foam filter and clean filter bowl in time after filtering.
Features of Aluminum Casting Using Ceramic Disc Filter
-Reduce scrap related to inclusions.
-Reduce costs related to inclusion defects.
-Increase productivity with higher extrusion or rolling speeds.
-Increase casting flexibility with easy alloy changes.
-No holding metal.
Sorry, the comment form is closed at this time.