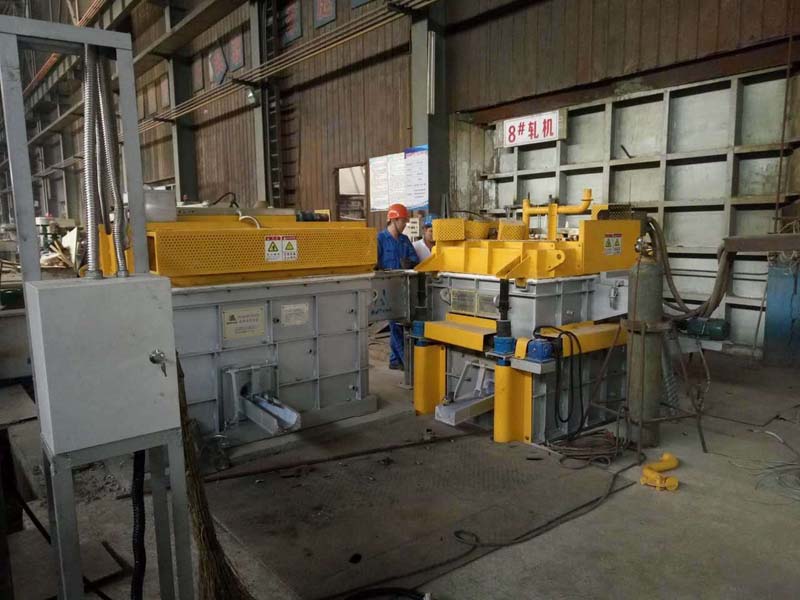
06 8月 Aluminium Degass
Aluminium Degass
Aluminium Degass unit is a degassing and purification treatment equipment which cleans metal by removing physical (hydrogen gas inclusions), chemicals (alkali metals) & metallurgical (alkali salts & sludge inter-metallic) impurities.
Adtech offers patented gas preheating and other sophisticated features for optimal molten aluminum refining.
The system operation is based on the proven principle of high-energy diffusion and chemically driven mass transfer. Liquid Aluminum Refining System have been available in the industry for years.
Attrition mixing of the melt and gas bubbles controls vortexing and reduces “carry-over”.
Vortexing is controlled by generating cross and reverse velocity vectors in the melt.
Through specialized design of the degassing bowl and placement of the gas dispersing mechanisms, the velocity vectors have no vortexing tendency.
The benefit of this design is that vortexing prevents reentry of dross into the upper layer of the melt and reduces bubble carryover at the lower exit end of the reactor.
Each reactor’s shape and internal slope prevents bubble agglomeration and improves efficiency.
Additionally, the reactor volume is increased from the bottom to the top in a controlled manner to accommodate increase in the gas bubble’s volume (which results from reduced metallostatic pressure).
This prevents bubble coalescence and keeps gas surface area higher for a longer duration of the gas’ total residence time in the reactor.
Preparation before Aluminium Degass
1. Check the mechanical system, electrical system and hydraulic system of the degassing device carefully before use, and deal with problems in time to ensure normal production.
2. Check the gas pipeline of the degassing device for leaks or blockage before use. If there is any problem, it should be treated in time to ensure the degassing effect.
3. Check carefully whether the rotor vent hole is unblocked, whether the graphite rotor rotates normally, and whether the gas flow is normal before casting.
4. Check whether the discharge ports are blocked before casting to prevent the aluminum melt from running.
5. Each white shift will open the upper cover of the deaerator and clean the slag and inspect the rotor. It must be replaced when the rotor head etches more than 50%.
6. Before each casting, clean the dust and other debris on the degassing device, clean all the aluminum scraps everywhere, and ensure the equipment is clean.
Preheat the Tank before Aluminium Degass
1. Check the wear of the refractory parts and repair parts of the container to prevent heat loss or metal leakage.
2, ceramic fiber cotton plugged in addition to the cylinder inlet and outlet.
3. The console heating program is set to preheat the cabinet and automatically control the heating.
Aluminum liquid handling operation when Aluminium Degass
1. Set the temperature of the aluminum liquid according to the requirements. When the casting is ready, the temperature control table of the degassing box should be insulated at 730 °C. If there is no material in the degassing box for any reason such as alloy transfer or shutdown, it is necessary to ensure the filling of aluminum. The temperature inside the cabinet reaches 750 ° C and can be filled with aluminum.
2. Before the furnace material enters the degassing box, the baffle in the front trough of the deaeration tank should be put down to properly raise the liquid level, so that the oxidation slag on the surface of the trough melt can enter the degassing chamber to float up, which is beneficial to be cleaned.
3. After the start of casting, the degassing gas is switched to argon gas, and the working state of the deaeration tank is set to the processing state.
4. Inject inert gas into the molten metal through the rotor, add chlorine gas to the inert gas, the flow rate of the inert gas is 4Nm3/h, and the flow rate of the chlorine gas is 0.5%-2% of the flow rate of the inert gas. Check the flow and pressure in the gas control cabinet, gas pressure The chlorine gas is 3 Bar and the argon gas is 6 Bar.
5. When the argon gas is suddenly unstable during the casting process, the rotation speed is reduced, or a certain rotor cannot work normally, it is decided to continue casting or returning to the furnace according to the measured hydrogen content on the line; if two or three rotors suddenly fail to work normally Must be processed immediately.
If you want to know more about the Aluminum Degassing Process, pls contact sales@adtechamm.com
Sorry, the comment form is closed at this time.